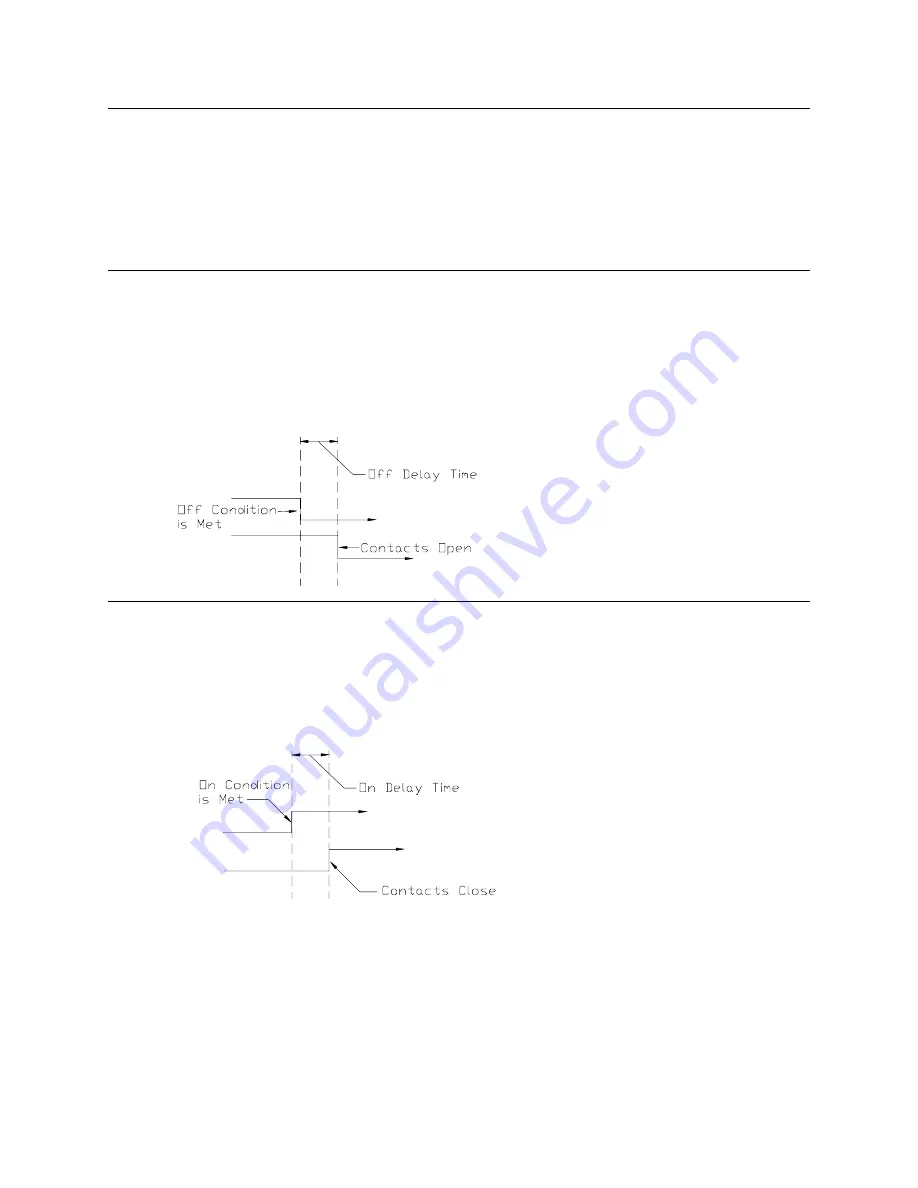
72
W7 ASD Installation and Operation Manual
Fault Detect Station Number
Program
⇒
Communication Settings
⇒
Fault Detect Station Number
In a multiple-ASD configuration this setting determines the ASD responsible
for fault notification.
Parameter Type — Selection List
Factory Default — 0
Changeable During Run — Yes
Minimum — 0
Maximum — 64
FL Off Delay
Program
⇒
Terminal Settings
⇒
Terminal Delays
⇒
Output Terminal
Delays
⇒
FL
⇒
FL Off Delay
This parameter delays the response of the FL output terminals by the
programmed value.
The on and off delay times of the FL terminals may be adjusted to provide
more response time to the device that is connected to the output terminals.
Parameter Type — Numerical
Factory Default — 2.0
Changeable During Run — No
Minimum — 2.0
Maximum — 200.0
Units — mS
FL On Delay
Program
⇒
Terminal Settings
⇒
Terminal Delays
⇒
Output Terminal
Delays
⇒
FL
⇒
FL On Delay
This parameter delays the response of the FL output terminals by the
programmed value.
The delay may be increased to prevent relay chatter.
Parameter Type — Numerical
Factory Default — 2.0
Changeable During Run — No
Minimum — 2.0
Maximum — 200.0
Units — mS
Fault Detect Station Number
FL On Delay