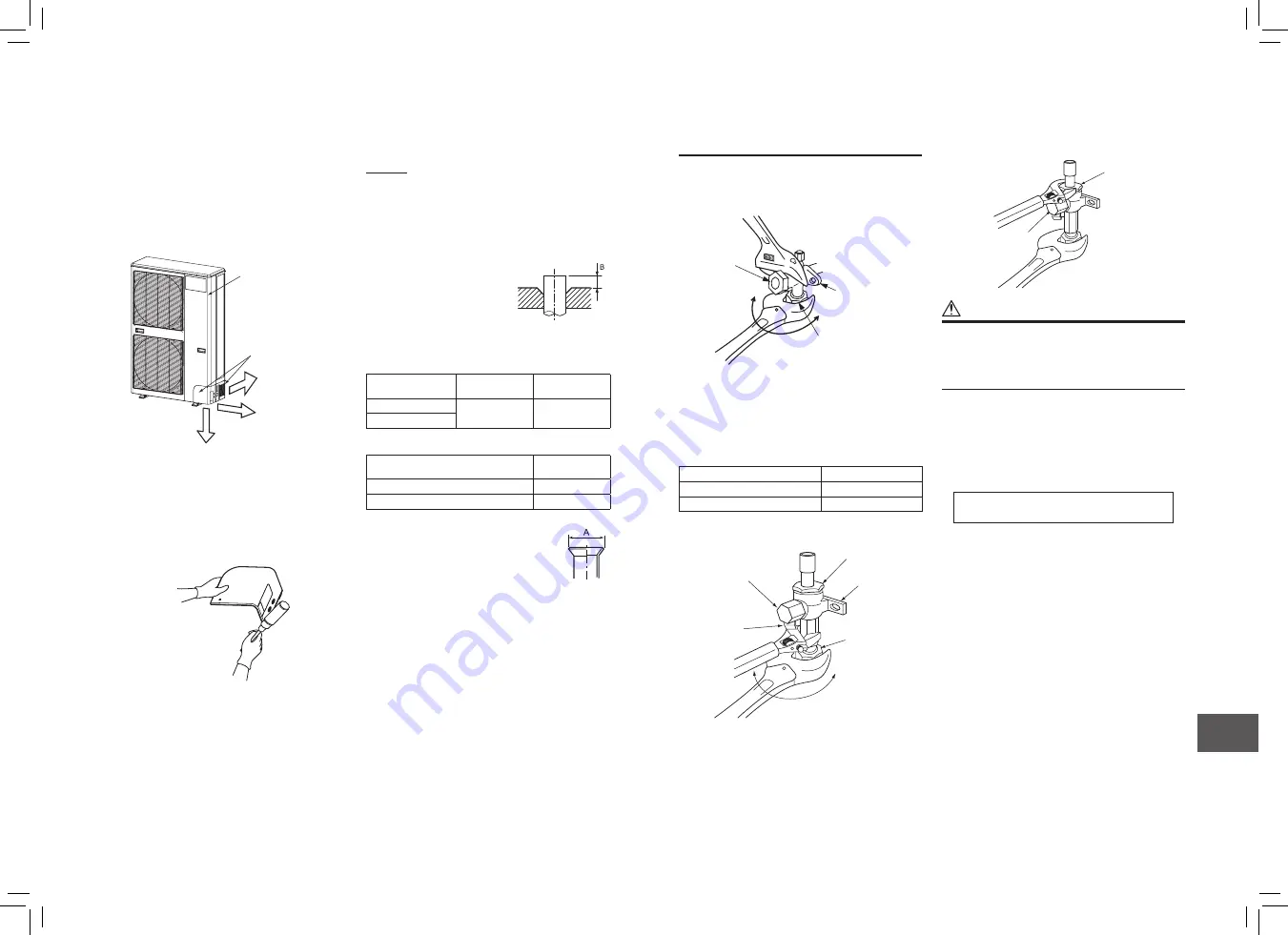
– 10 –
5
Refrigerant piping
Piping connections are inside the front panel of the
unit and the front panel and pipe cover needs to be
removed before piping and wiring connections are
made.
Piping can enter the outdoor unit from the back, from
the side or from the bottom as shown
Flaring
1. Cut the pipe with a pipe cutter.
Be sure to remove burrs that may cause a gas
leak.
2. Insert the supplied flare nut into the pipe, and then
flare the pipe. The flare tools newly manufactured
for R410A are recommended.
However, the conventional tools
can be used by adjusting the
projection margin of the copper
pipe.
▼ Projection margin in flaring : B (Unit : in (mm))
Rigid (Clutch type)
Outer diameter of
copper pipe
R410A tool
used
Conventional
tool used
3/8” (9.5)
0 - 0.02”
(0 - 0.5)
0.04” - 0.06”
(1.0 - 1.5)
5/8” (15.9)
▼ Flaring diameter size : A (Unit : in (mm))
Outer diameter of copper pipe
A
+0
-0.02”(–0.4)
3/8” (9.5)
0.52” (13.2)
5/8” (15.9)
0.78” (19.7)
* In case of flaring for R410A with the
conventional flare tool, pull the tool out
approx. 0.02” (0.5 mm) to adjust it to the
specified flare size.
The copper pipe gauge is useful for
adjusting the projection margin size.
1. Remove the front panel of the unit.
2. Remove the pipe cover.
3. Remove the appropriate knockout depending
on the orientation of the piping.
The pipe cover is easily mounted by cutting off
the slit at the lower part of the pipe cover.
* Be sure to wear heavy work gloves while working.
4. Remove the burrs from the knockout opening
and use the factory supplied protective edge
guard material around the opening to protect the
piping and the wiring.
5. Remove the flare nut from the service valve on
outdoor unit. Insert the flare nut into the field
piping, and flare the pipe.
Bend the pipe approx. 90 degree with a pipe
bender for side and rear piping.
6. When the piping connections are complete
reinstall the pipe cover.
Front panel
Pipe cover
Rear
Side
Bottom
Tightening of Flare
Connections
1. Align the centers of the flare connections and fully
tighten the flare nuts with your fingers.
2. Use two wrenches to loosen or tighten the flare nut
on the gas service valve as shown in the figure.
Use only one wrench to loosen or tighten the flare
not on the liquid service valve.
The final tightening with a torque wrench should be
to the specifications shown in table below.
Unit : ft•Ibs (N•m)
Outer diameter of copper pipe
Tightening torque
3/8” (9.5 mm)
24 - 31 (33 - 42)
5/8” (15.9 mm)
50 - 60 (68 - 82)
• After the installation work, be sure to check for gas
leaks of the pipe connections with nitrogen.
Valve at liquid side
Cap
Loosened
Piping valve
Tightened
Flare nut
Valve at gas side
NO GOOD
Cap
Charge orifice
Cover
Charge orifice
Loosened
Cover
Piping valve
Flare nut
Tightened
CAUTION
1. Do not put the crescent wrench on the charge
orifice or cover.
The valve may be broken.
2. If applying excessive torque, the nut may break
according to some installation conditions.
• Pressure of R410A is higher than that of R22
(Approx. 1.6 times).
Therefore, using a torque wrench, tighten the flare
pipe connecting sections that connect the indoor/
outdoor units at the specified tightening torque.
Incomplete connections may cause not only a gas
leak, but also trouble with the refrigeration cycle.
Do not apply refrigerant oil to the flared
surface.
19-EN
20-EN
EN
1131501101-00_S01_297x210_60p_S_p70_220425.indd 10
25/4/2565 15:23:35