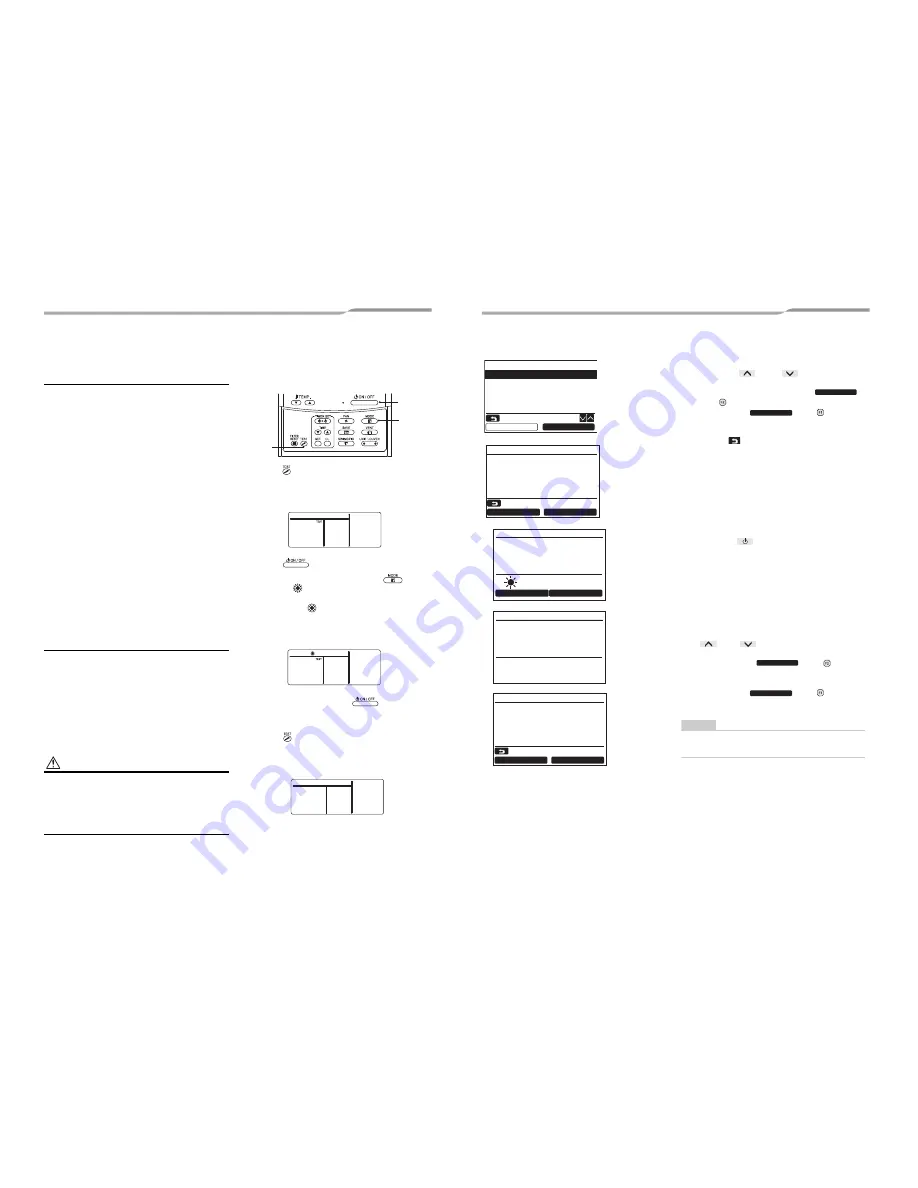
– 29 –
11
Test run
Before test run
• Before turning on the power supply, carry out the
following procedure.
1) By using 500 V-megger, check that resistance
of 1 M
Ω
or more exists between the terminal
block L to N and the earth (grounding).
If resistance of less than 1 M
Ω
is detected, do
not run the unit.
2) Check the valve of the outdoor unit being
opened fully.
• To protect the compressor at activation time, leave
power-ON for 12 hours or more before operating.
• Do not press the electromagnetic contactor to
forcibly perform a test run. (This is very dangerous
because the protective device does not work.)
• Before starting a test run, set addresses by following
the Installation Manual supplied with the outdoor
unit.
• Before carrying out a test run, complete the water
supply (10 °C or more) to the water pipe system and
the wiring for the pump.
The entire system stops by detecting a check code
(check code: A01) when the water is not supplied to
the Hot Water Module and when the water does not
circulate.
Execute a test run
Operate the unit with the wired remote controller as
usual.
For the procedure of the operation, refer to the
attached Owner’s Manual to the outdoor unit.
A forced test run can be executed in the following
procedure even if the operation stops by thermostat-
OFF.
In order to prevent a serial operation, the forced test
run is released after 60 minutes have passed and
returns to the usual operation.
CAUTION
Do not use the forced test run for
cases other than the test run
because it applies an excessive
load to the devices.
<RBC-AMT32E>
1
Push
button for 4 seconds or more.
[TEST] is displayed on the display part and
the selection of mode in the test mode is
permitted.
2
Push
button.
3
Select the operation mode with
button, [
Heat].
• Cannot select the hot water module in a mode
other than [
Heat].
• The temperature controlling function does not
work during test run.
• The detection of trouble is performed as usual.
4
After the test run, push
button to
stop a test run.
(Display part is same as procedure
1
.)
5
Push
check button to cancel (release
from) the test run mode.
([TEST] disappears on the display and the status
returns to a normal.)
2, 4
3
1,5
<RBC-AMS55E-ES/EN>
1
Push the [
∧
] / [
∨
] button to
select “1. Test mode” on the “Field setting
menu” screen, then push the “
Set” [
F2] button.
Pushing the “
Yes” [
F1] button
sets the test mode and the screen returns to the
“Field setting menu” screen.
Push [
CANCEL ] twice, the screen (2)
appears.
2
Push the [
ON / OFF ] button to start the
test mode. The screen
(1)
shown in the left
appears. (The screen
(2)
appears when the
operation is stopped.)
Perform the test mode in the “Cool” or “Heat”
mode.
Temperature setting cannot be adjusted during
the test mode.
Check codes are displayed as usual.
3
When the test mode is finished, push the
[
∧
] / [
∨
] button to select “1. Test
mode” on the “Field setting menu” screen,
then push the “
Set” [
F2]
button.
The screen
(3)
appears.
Pushing the “
Yes” [
F1] button
stops the test mode screen and continues the
normal operation.
NOTE
The test mode stops after 60 minutes and the screen
returns to the normal / detailed display.
1.Test mode
2.Register service info.
3.Alarm history
4.Monitor function
5.Setting louver position
Field setting menu(1/2)
Return
Set
Set
Yes
Return
Test mode start.
No
Yes
Test mode
Test
(1)
Room A
12:00
Mode
Fan Speed
Heat
Set
Yes
Test
(2)
Room A
12:00
Return
Test mode stop.
No
Yes
Test mode
(3)
57-EN
58-EN
Summary of Contents for MMW-AP0481CHQ-E
Page 38: ...EB99829001 ...