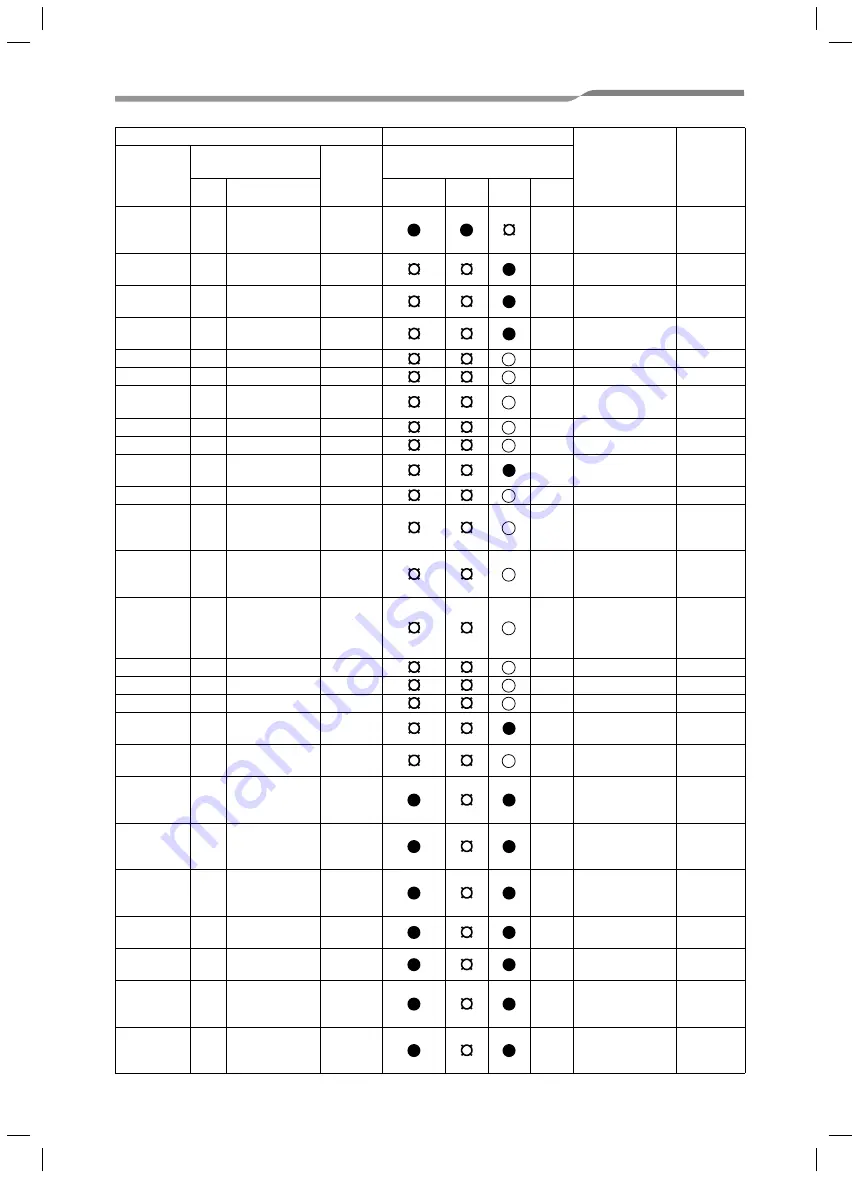
102
SMMS High-Wall Type
Installation Manual
E31
E31
Number of IPDU
(*1)
CF
IPDU
communication
error
I/F
F01
—
—
0F
ALT
Indoor unit TCJ
sensor error
Indoor unit
F02
—
—
0d
ALT
Indoor unit TC2
sensor error
Indoor unit
F03
—
—
93
ALT
Indoor unit TC1
sensor error
Indoor unit
F04
F04
—
19
ALT TD1 sensor error
I/F
F05
F05
—
A1
ALT TD2 sensor error
I/F
F06
F06
01:TE1 sensor
02:TE2 sensor
18
ALT
TE1 sensor error
TE2 sensor error
I/F
F07
F07
—
18
ALT TL sensor error
I/F
F08
F08
—
1b
ALT TO sensor error
I/F
F10
—
—
OC
ALT
Indoor unit TA
sensor error
Indoor unit
F12
F12
—
A2
ALT TS1 sensor error
I/F
F13
F13
01:Comp. 1 side
02:Comp. 2 side
03:Comp. 3 side
43
ALT TH sensor error
IPDU
F15
F15
—
18
ALT
Outdoor unit temp.
sensor miscabling
(TE, TL)
I/F
F16
F16
—
43
ALT
Outdoor unit
pressure sensor
miscabling (Pd,
Ps)
I/F
F22
F22
—
B2
ALT TD3 sensor error
I/F
F23
F23
—
43
ALT Ps sensor error
I/F
F24
F24
—
43
ALT Pd sensor error
I/F
F29
—
—
12
SIM
Indoor unit other
error
Indoor unit
F31
F31
—
1C
SIM
Indoor unit
EEPROM error
I/F
H01
H01
01:Comp. 1 side
02:Comp. 2 side
03:Comp. 3 side
IF
Compressor break
down
IPDU
H02
H02
01:Comp. 1 side
02:Comp. 2 side
03:Comp. 3 side
1d
Compressor
trouble (lock)
IPDU
H03
H03
01:Comp. 1 side
02:Comp. 2 side
03:Comp. 3 side
17
Current detect
circuit system
error
IPDU
H04
H04
—
44
Comp. 1 case
thermo operation
I/F
H05
H05
—
—
TD1 sensor
miswiring
I/F
H06
H06
—
20
Low pressure
protective
operation
I/F
H07
H07
—
d7
Oil level down
detective
protection
I/F
Check code
Wireless remote controller
Check code
name
Judging
device
Wired
remote
controller
display
Outdoor unit 7-
segment display
AI-NET
central
control
display
Sensor block display of
receiving unit
Auxiliary code
Operation
Timer Ready
Flash
1111058901_EN.indb 35
1111058901_EN.indb 35
11/19/14 3:34 PM
11/19/14 3:34 PM
FILE NO. SVM-1
40
7
8