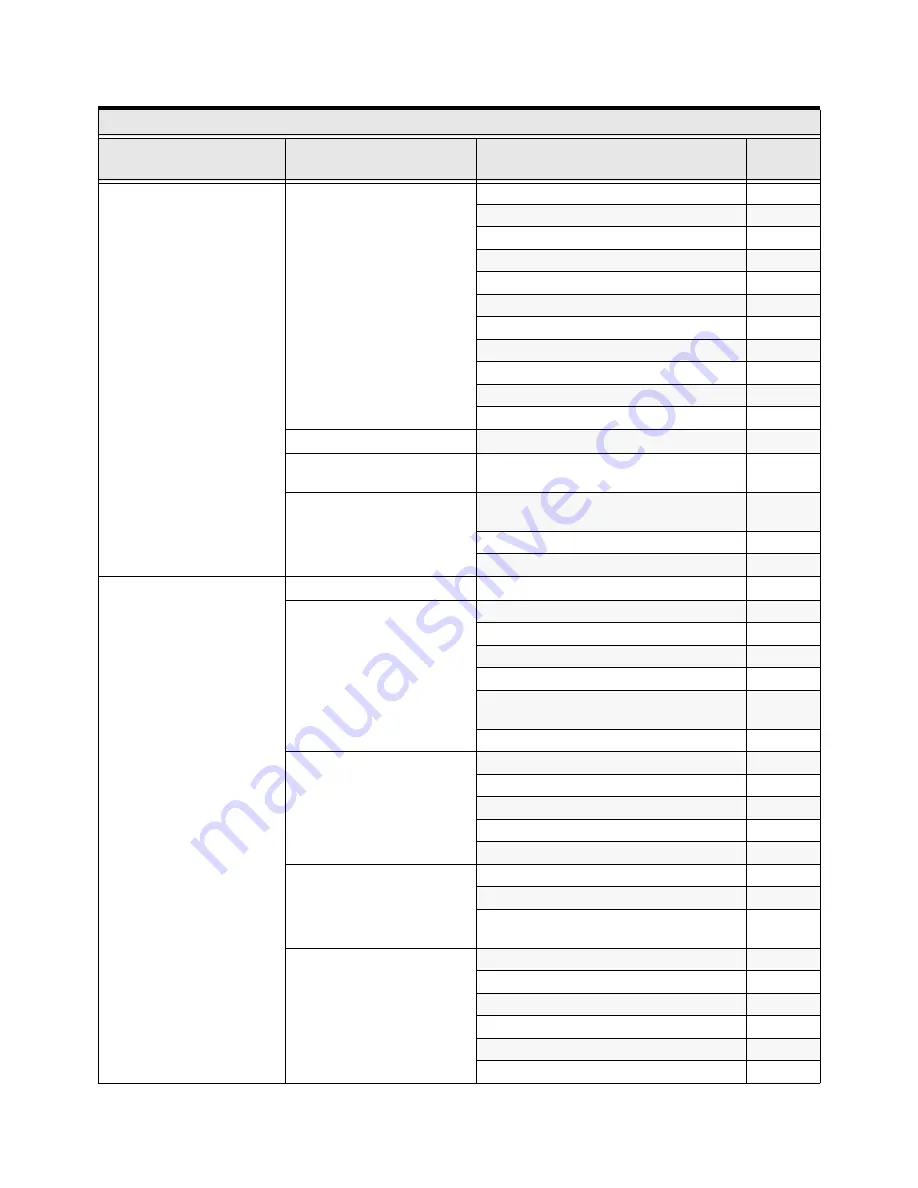
44
GX7R ASD Quick Start Guide
F
REQUENCY
S
ETTING
Preset Speeds
#5 Frequency & Characteristics
F022
#6 Frequency & Characteristics
F023
#7 Frequency & Characteristics
F024
#8 Frequency & Characteristics
F287
#9 Frequency & Characteristics
F288
#10 Frequency & Characteristics
F289
#11 Frequency & Characteristics
F290
#12 Frequency & Characteristics
F291
#13 Frequency & Characteristics
F292
#14 Frequency & Characteristics
F293
#15 Frequency & Characteristics
F294
Preset Speed Mode
Use Preset Speed (check box)
F380
Fwd/Rev Disable
Disable Forward Run/Disable Reverse Run
(check box)
F311
Motorized Pot Settings
Motorized Pot Setting Disposition at Power
Down
F108
Minimum Frequency
N/A
Maximum Frequency
N/A
P
ROTECTION
Dynamic Braking
Dynamic Braking Configuration (Not Used)
F304
Stall
Over-Current Stall Level
F601
Over-Voltage Stall
F305
Over-Voltage Stall Level Configuration
N/A
Over-Voltage Stall Level (Fast)
F625
Continuing Stall Period (During Positive
Torque/Speed)
F452
Stall Prevention During Regeneration
F453
DC (Injection) Braking
DC Injection Start Frequency
F250
DC Injection Braking Current
F251
DC Injection Braking Time
F252
Motor Shaft Fixing Control (check box)
F253
Motor Shaft Stationary Control (check box)
F254
Emergency Off Settings
Emergency Off Mode Configuration
F603
DC Injection Braking Time
F604
Emergency Off Activation of the FL Output
(check box)
N/A
Retry/Restart
Number of Retries
F303
Restart Conditions (check box)
F301
Scan Rate
F312
Lock-on Rate
F313
Search Method
F314
Search Inertia
F315
Program Menu Navigation
Primary Menu
Sub Menu
Parameter Name
Parameter
Number
Summary of Contents for GX7R ASD
Page 1: ...GX7R ASD Quick Start Guide TOSHIBA GX7R ASD Quick Start Guide DN 68986 002 September 2014 ...
Page 2: ...GX7R ASD Quick Start Guide DN 68986 002 September 2014 ...
Page 76: ...68 GX7R ASD Quick Start Guide Figure 23 480 Volt 30 100 HP GX7R ASD ...
Page 77: ...GX7R ASD Quick Start Guide 69 Figure 24 480 Volt 125 150 HP GX7R ASD ...