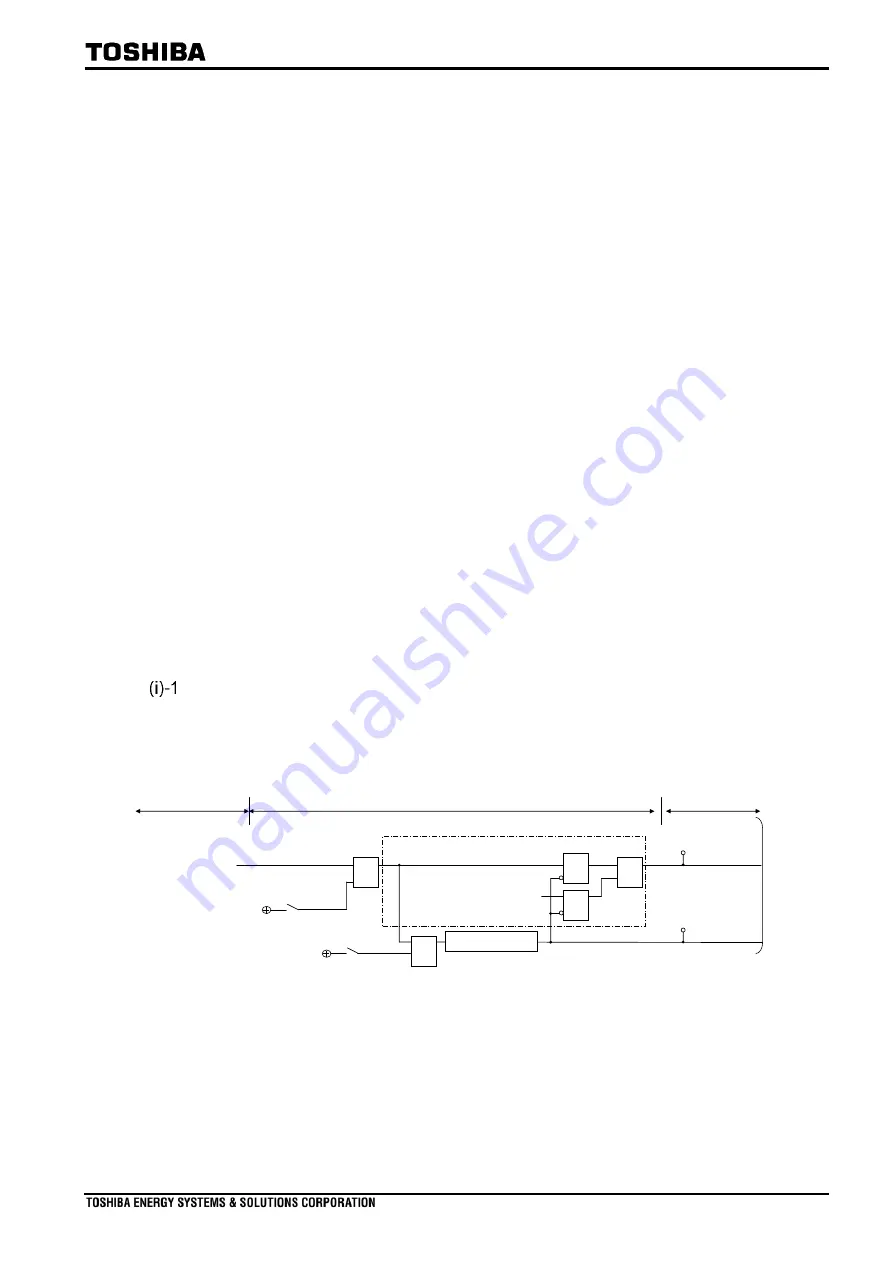
6F2S1915 (0.46)
GRZ200 (Soft 031 & 032)
- 532 -
4.1.4
Setup for BIO module
The user should connect the SPOS input/output points with the BI and the BO circuits;
subsequently, the SPOS function is able to issue select and operate commands. The user should
execute the following four steps below.
i
BI connection for status-signals
ii
BO connection for “Select command On/Off”
iii
BO connection for “operate command”
iv
Note that the SPOS01 function commences operation when the scheme switch [
SPOS01-EN
]
is set to
On
.
(i)
BI connection for status-signals
Figure 4.1-30 exemplifies the reception of signals at the SPOS01 function; the user can set a
input-point using the setting [
SPOS01-NOPSG
]†.
†Note: Normally an input-signal corresponding to phase-A is generated using a normally-
open contact (NO). If the signal is generated by the normally-closed contact, the
user is required to set scheme switch [
SPOS01-NSOSGI
]
On
in order that the
input-signal should be decided in inversion.
Connection with Binary input circuit
Suppose an input signal is provided on the first BI circuit at IO#1 slot. In this case, the user
should set the input point (200B01 8001001110†) for the setting [
SPOS01-NOPSG
], otherwise,
the SPOS01 function cannot run correctly.
Signals by Binary input circuits
Output
‡
Signal acquisition logic in SPOS01
“SPOS01_F_QLT_SPP”
(510001
_
8101011F59)
Event suppression detector
Chattering detector
Status before chattering
S
R
BI signal connected by
setting [
SPOS01-NOPSG
]
[
SPOS01-EN
]
On
[SPOS01-SPPEN]
On
&
&
&
“SPOS01_STATE”
(510001
_
0001011001)
1
≥
To select and operate
condition logics
Figure 4.1-30 Acquisition of binary input signal in SPOS01
†Note: The user should set the actual input-points. For Input points see in Chapter
Technical description: Binary IO module.
‡Note: In Figure 4.1-30 two signals can be issued: “SPOS01_STATE” and
“SPOS01_F_QLT_SPP”. One is used in the select condition logic and the operate
condition logic (see Figure 4.1-13 and Figure 4.1-29). Another is used for operation
Summary of Contents for GR 200 Series
Page 1047: ...6F2S1915 0 46 GRZ200 Soft 031 032 1026 Figure 8 3 4 Screen shot from GR TIEMS ...
Page 1354: ...6F2S1915 0 46 GRZ200 Soft 031 032 1333 Appendix 1 Signal list for common function ...
Page 1410: ...6F2S1915 0 46 GRZ200 Soft 031 032 1389 This page is intentionally blank ...
Page 1480: ...6F2S1915 0 46 GRZ200 Soft 031 032 1459 Appendix 6 Ordering ...
Page 1497: ...6F2S1915 0 46 GRZ200 Soft 031 032 1476 Appendix 7 Technical data ...
Page 1518: ...6F2S1915 0 46 GRZ200 Soft 031 032 1497 Appendix 8 Manufacture setting ...
Page 1523: ...6F2S1915 0 46 GRZ200 Soft 031 032 1502 Appendix 10 CT requirement ...
Page 1531: ...6F2S1915 0 46 GRZ200 Soft 031 032 1510 Appendix 12 Engineering exercise ...
Page 1563: ......