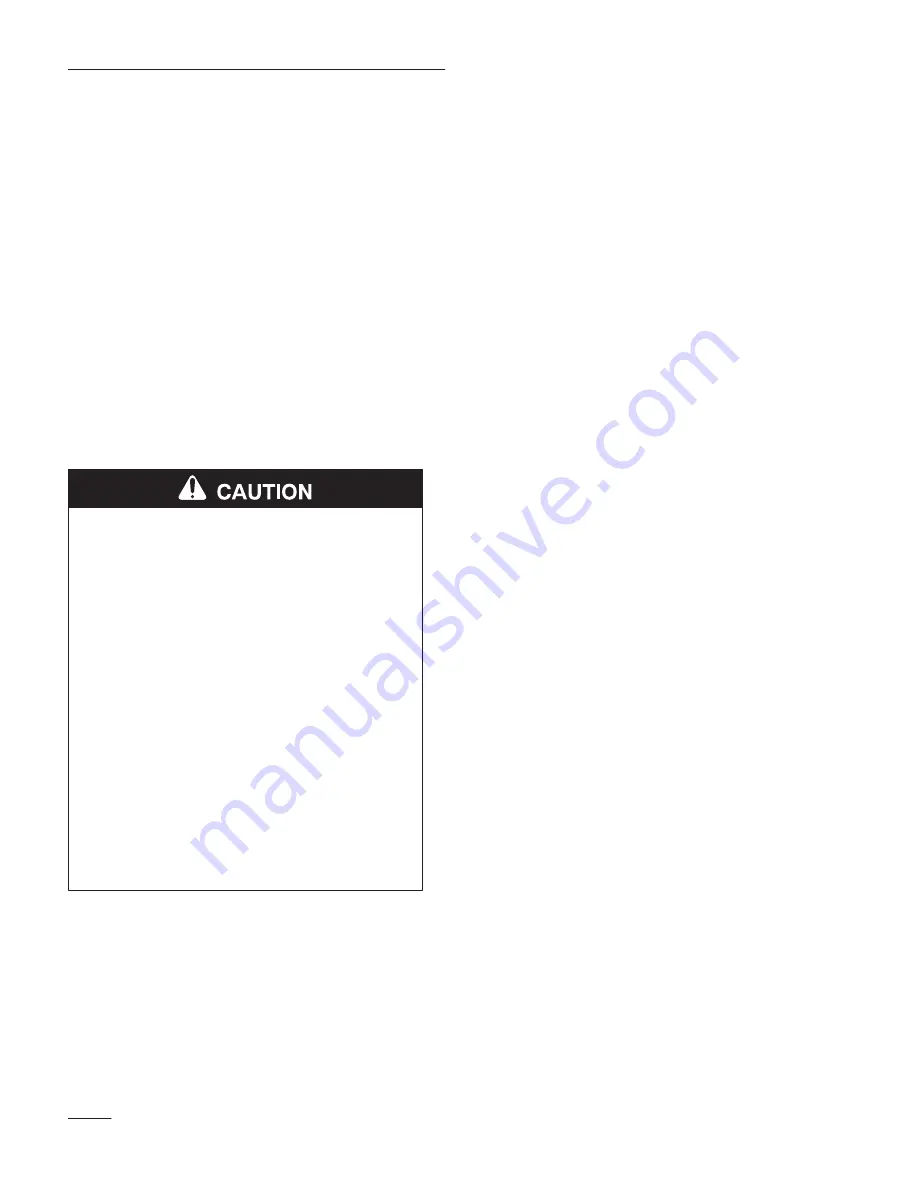
Operation
32
Transporting Machines
Use a heavy–duty trailer or truck to transport the
machine. Ensure that the trailer or truck has all
necessary lighting and marking as required by law.
Please carefully read all the safety instructions on
pages 3–13. Knowing this information could help
you, your family, pets or bystanders avoid injury.
To transport the machine:
•
Lock brake and block wheels.
•
Securely fasten the machine to the trailer or
truck with straps, chains, cable, or ropes.
•
Secure a trailer with a safety chains to towing
vehicle.
POTENTIAL HAZARD
•
This unit does not have proper turn signals,
lights, reflective markings, or a slow
moving vehicle emblem. These items are
required to drive on a public street or
roadway.
WHAT CAN HAPPEN
•
Driving on a street or roadway without
such equipment is dangerous and can lead
to accidents causing personal injury.
•
Driving on a street or roadway without
such equipment may also be a violation of
State laws and the operator may be subject
to traffic tickets and/or fines.
HOW TO AVOID THE HAZARD
•
Do not drive machine on a public street or
roadway.
Loading Machines
Use extreme caution when loading units on trailers or
trucks. One full width ramp that is wide enough to
extend beyond the rear tires is recommended instead
of individual ramps for each side of the unit. The
lower rear section of the tractor frame extends back
between the rear wheels and serves as a stop for
tipping backward. Having a full width ramp provides
a surface for the frame members to contact if the unit
starts to tip backward. If it is not possible to use one
full width ramp, use enough individual ramps to
simulate a full width continuous ramp.
Ramp should be long enough so that the angles
between the ramp and the ground and the ramp and
the trailer or truck do not exceed 15 degrees. A
steeper angle may cause mower deck components to
get caught as the unit moves from ramp to trailer or
truck. Steeper angles may also cause the unit to tip
backward. If loading on or near a slope, position the
trailer or truck so it is on the down side of the slope
and the ramp extends up the slope. This will
minimize the ramp angle. The trailer or truck should
be as level as possible.
IMPORTANT: DO NOT attempt to turn the
unit while on the ramp; you may lose control
and drive off the side.
Avoid sudden acceleration when driving up a ramp
and sudden deceleration when backing down a ramp.
Both maneuvers can cause the unit to tip backward.