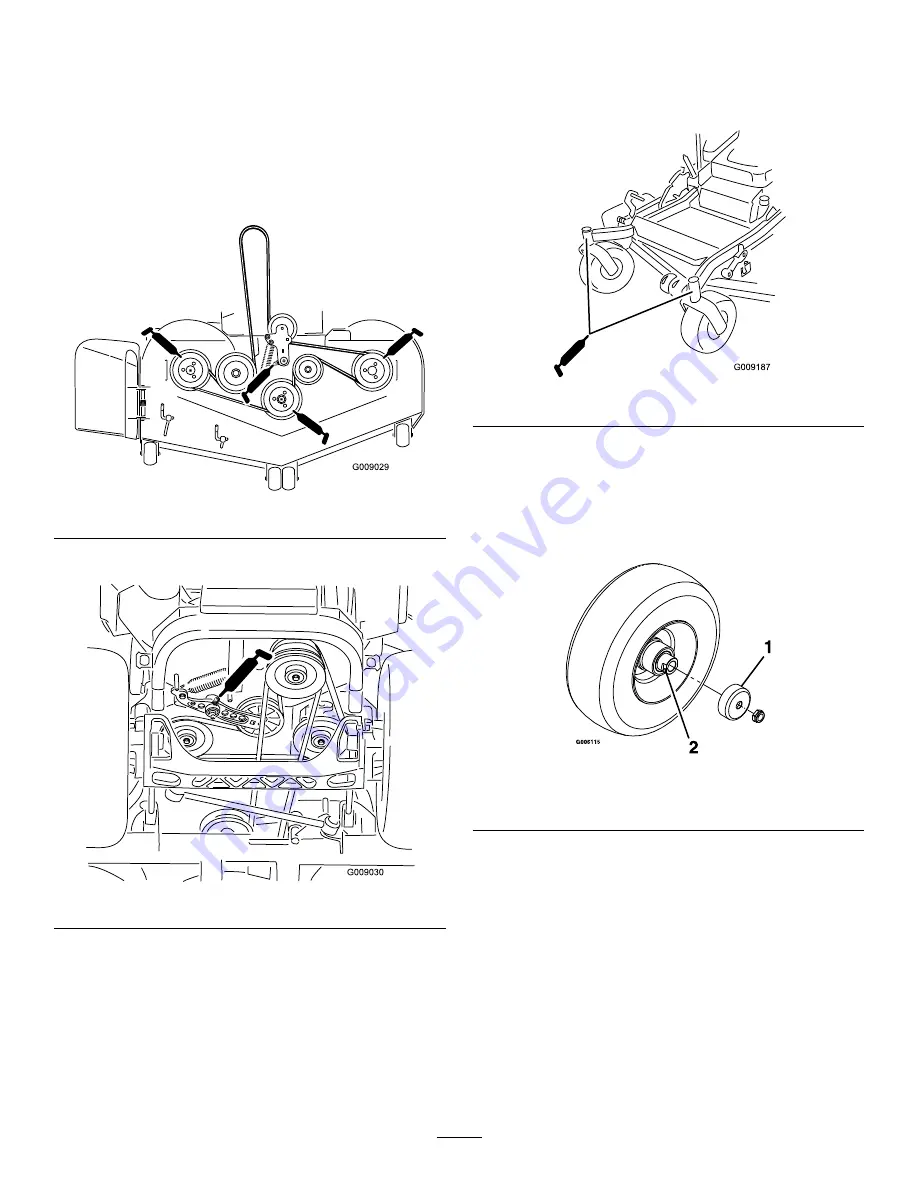
2. Stop the engine, remove the key, and wait for all
moving parts to stop before leaving the operating
position.
3. Grease the mower deck idler pulley pivot until grease
come out the bottom (Figure 40).
4. Grease the fittings on the side of the 3 spindle
bearings until grease come out the bottom
(Figure 40).
Figure 40
5. Grease the drive belt idler arm (Figure 40).
Figure 41
6. Remove the dust cap and adjust the caster pivots.
Keep the dust cap off until greasing is done. Refer to
Adjusting the Caster Pivot Bearing in Maintenance.
7. Remove the hex plug. Thread a grease zerk into the
hole.
8. Pump grease into the zerk until it oozes out around
the top bearing.
9. Remove the grease zerk in the hole. Install the hex
plug and dust cap (Figure 42).
Figure 42
Lubricate Caster Wheel Hubs
Service Interval:
Yearly
1. Stop the engine, wait for all moving parts to stop,
and remove the key. Engage the parking brake.
Figure 43
1.
Seal guard
2.
Spacer nut with wrench
flats
2. Remove the caster wheel from the caster forks.
3. Remove the seal guards from the wheel hub.
4. Remove one of the spacer nuts from the axle
assembly in the caster wheel. Note that thread
locking adhesive has been applied to lock the spacer
nuts to the axle. Remove the axle (with the other
spacer nut still assembled to it) from the wheel
assembly.
5. Pry out seals, and inspect bearings for wear or
damage and replace if necessary.
6. Pack the bearings with a general-purpose grease.
7. Insert one bearing, one new seal into the wheel.
31
Summary of Contents for Z Master 74923
Page 6: ...Slope Chart 6...
Page 8: ...107 2102 107 2112 109 7232 109 7304 109 7929 109 9477 8...
Page 65: ...Schematics Wire Diagram Rev A 65...
Page 66: ...Notes 66...
Page 67: ...Notes 67...