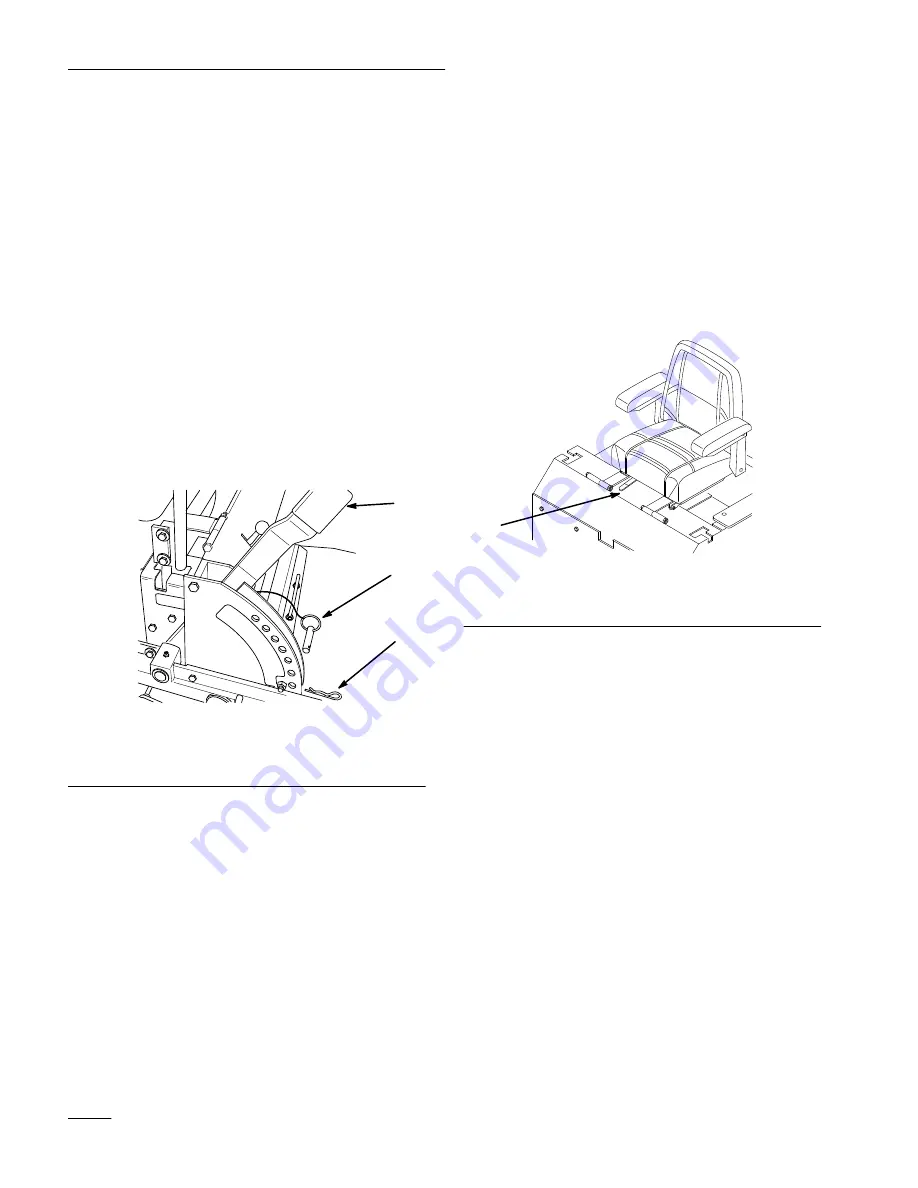
Operation
22
Adjusting Height-of-Cut
The height-of-cut is adjusted from 1-1/2” to 5”
(38 to 127 mm) in 1/2” (13 mm) increments by
relocating clevis pin in different hole locations.
1.
Raise the height-of-cut lever to the transport
position (also the 5” (127 mm) cutting height
position) (Fig. 11).
2.
To adjust, remove hairpin cotter and clevis pin
from height-of-cut bracket (Fig. 11).
3.
Select hole in height-of-cut bracket
corresponding to the height-of-cut desired. Lift
handle to transport position, insert clevis pin
(Fig. 11).
4.
Secure clevis pin with hairpin cotter (Fig. 11).
1
m-3654
3
2
Figure 11
1.
Height of cut lever
2.
Clevis Pin
3.
Hairpin Cotter
Positioning the Seat
The seat can move forward and backward. Position
the seat where you have the best control of the
machine and are most comfortable.
1.
To adjust, move the lever sideways to unlock
seat (Fig. 12).
2.
Slide the seat to the desired position and release
lever to lock in position.
1
1200
m–3655
Figure 12
1.
Adjustment knob