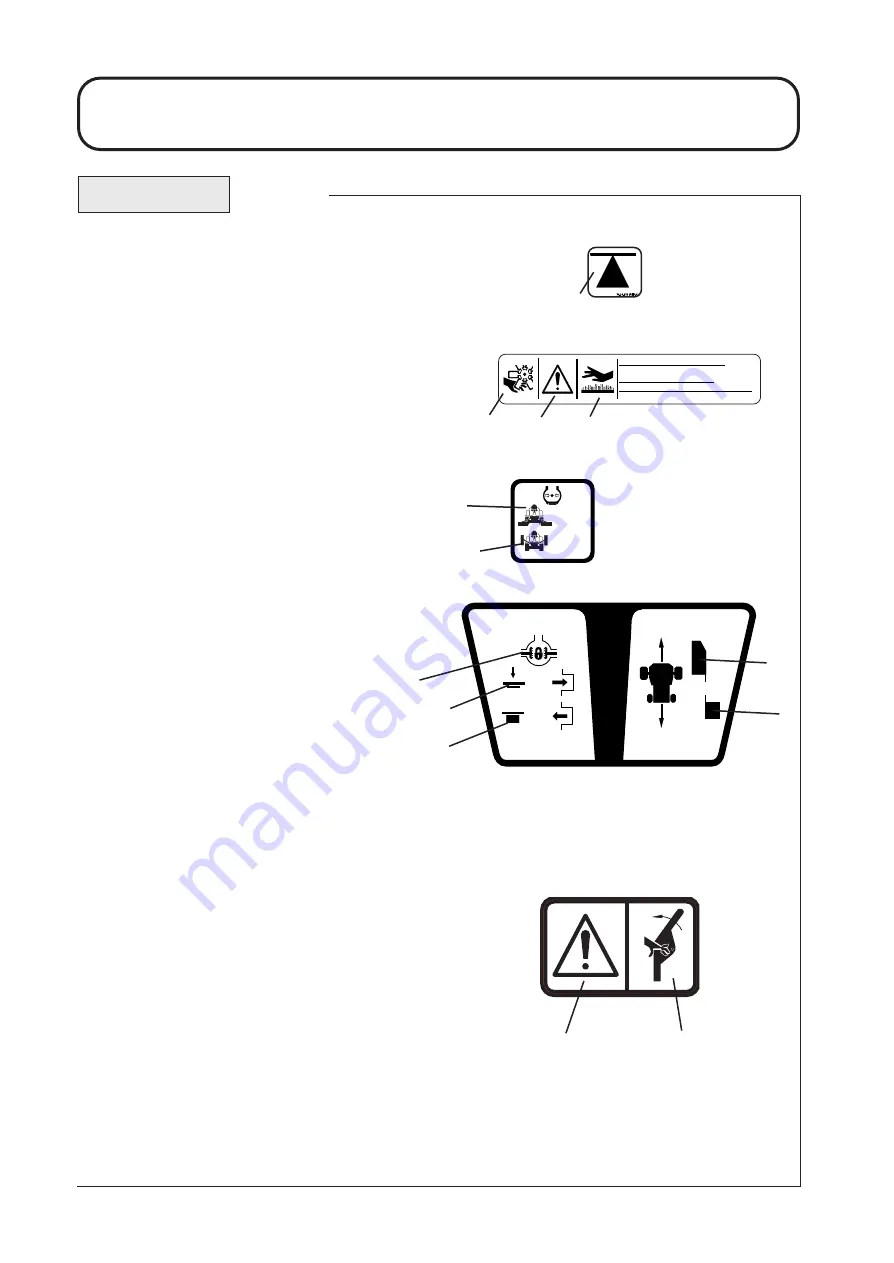
111-1033TH051006
SAFETY PRECAUTIONS
DECALS Continued.
HEIZKORPERDECKELENTFERNENERSTWENNDERMOTORKUHLIST.
ONLYREMOVE RADIATORCAPWHENENGINEISCOOL.
VERWIJDERDE RADIATORDOPPASNADATDE MOTORISAFGEKOELD.
ILFAUTTOUJOURSATTENDRELE REFROIDISSEMENTDUMOTEUR
AVANTDERETIRERLE BOUCHONDURADIATEUR.
70-13-073 REV (.0.)
Decal - Jacking / Support Point
Part No: 70-13-072
Location: Front Axle - 2 Points
Rear Towing Eye
a) Jacking and Support Point
Decal - Engine Fan / Radiator
Part No: 70-13-073
Location: Engine Fan Cowl
a) Danger of Severing Fingers
b) Caution
c) Warning - Hot Surfaces
Decal - Tyre Pressure
Part No. 950832 (2)
Location: LH/RH Chassis - 4 Places
a) Mowing
b) Road Travel
Decal - Diff Lock / Control Pedal
Part No: 924812
Location: Centre Platform.
a) Differential Lock
b) Depress to engage Diff-lock
c) Release to Dis-engage Diff-lock
d) Forward Speed & Directional Control
e) Reverse Speed & Directional Control
Decal - Warning Crush Hazard
Part No. 111-0773(A)
A = Safety Alert - Be aware to the possibility of injury
B = Crushing of fingers. Force applied from side.
950832 Rev.2
0.7 BAR
10 PSI
1.4 BAR
20 PSI
1.13
1.13
a
a
b
c
a
b
924812 REV.(0)
a
b
c
d
e
111-0773 Rev A
a
b
Summary of Contents for Reelmaster 3220-D
Page 2: ......
Page 33: ...111 1033TH051006 OPERATING THE MOWER 1 33 1 33 1 2 3 4 3 4 fig 1 ...
Page 79: ...111 1033TH051006 1 79 1 79 HYDRAULIC CIRCUIT DIAGRAM RM3220 D 1D922C16 ...
Page 81: ...111 1033TH051006 HYDRAULIC CIRCUIT DIAGRAM RM3240 D 1 81 1 81 ...