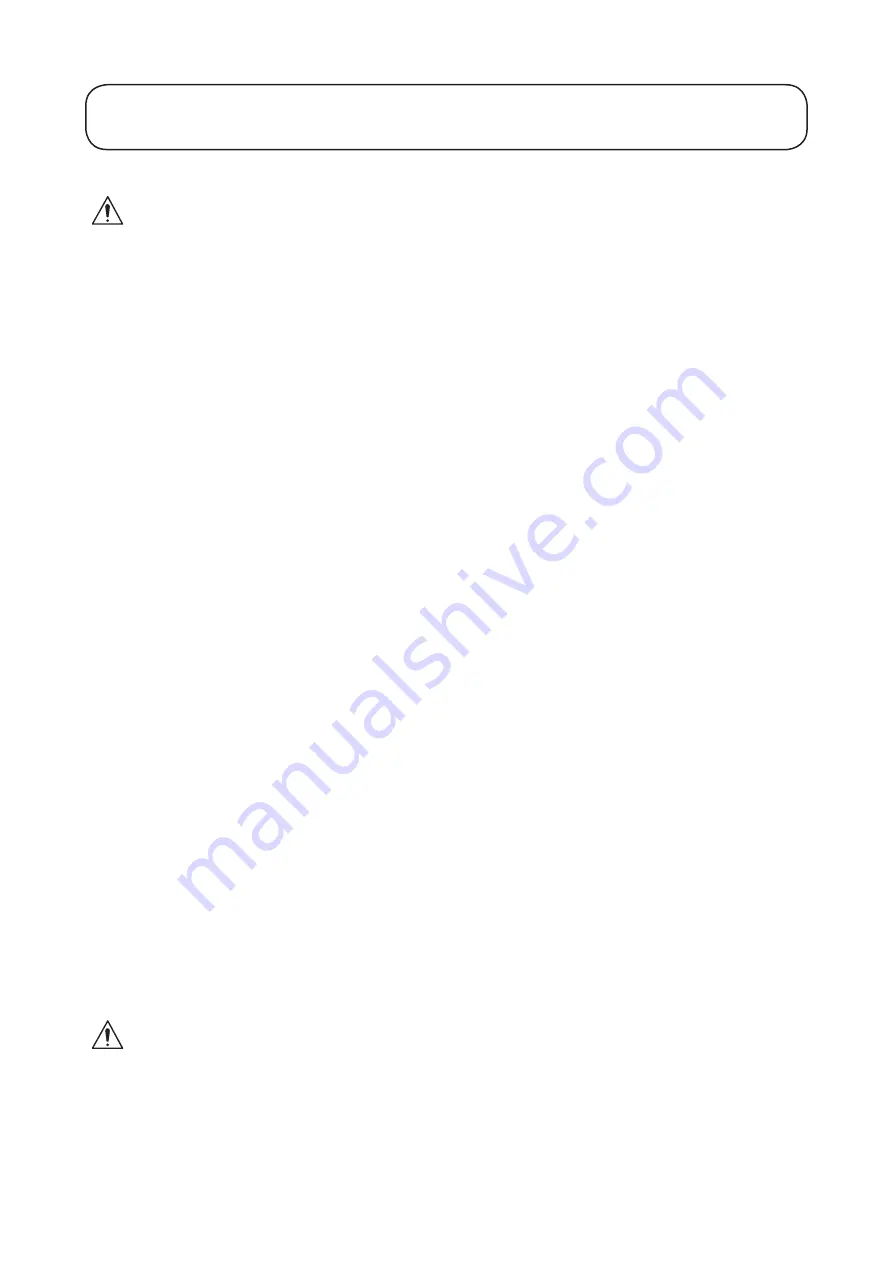
1.27
1.27
Safety Notice
WARNING: PREVENT ACCIDENTS - Before operating the mower it is essential that;
- The operator reads and understands this manual.
- The operator platform latching mechanism is fully engaged and in good working order, refer to
OPERATOR PLATFORM LATCHING MECHANISM.
- The daily maintenance checks have been properly carried out and the mower is in good working
order.
- The operator should wear safety clothing and eye protection. Failure to do so could result in risk to
health and safety.
- The area where the equipment is to be used is inspected and all objects which may be thrown by the
machine are removed.
Operate safely on slopes;
It is essential to follow safe working practices when working on slopes. In order to avoid potentially
hazardous situations, it is essential that the operator understands and observes the relevant safety
precautions listed in this manual, refer to SAFETY PRECAUTIONS.
This machine is fitted with a R.O.P.S as standard to increase operator safety in the event of the
machine rolling over.
The R.O.P.S frame may be folded down to allow access into area of restricted height.
While the R.O.P.S is folded down it does not provide any protection in the event of a roll over and
should not be considered as a Roll Over Protective structure.
Operator Presence Control
Cutterblade Drive Lockout:
Drive to the cutterblades is only possible when the operator is seated. If the
operator raises off the seat for a period of more than one second, a switch is activated and drive to the cut
-
terblades is automatically disengaged. To re-engage drive to the cutterblades, the operator must return to the
seat, then operate the cutterdeck drive switch to the ‘OFF’ position before moving it back to the ‘ON’ posi
-
tion. If the operator rises off the seat for a brief moment during normal work, drive to the cutterblades is not
affected.
Note: The engine can only be started with the cutterdeck drive switch in the ‘OFF’ position.
Engine Start Lockout:
The engine can only be started when the forward/reverse travel pedal is in the
‘NEUTRAL’ position, the cutterdeck drive switch is in the ‘OFF’ position and the parking brake is engaged.
When these circumstances are satisfied, switches are activated permitting the engine to be started.
Engine Run Interlock:
Once the engine is started the operator must be seated before the parking brake is
released for the engine to continue to run.
Note: The engine will cut out if the operator leaves the seat without engaging the parking brake.
WARNING: PREVENT ACCIDENTS - Do not operate the turf mower if the operator presence
controls are defective in any way. ALWAYS replace faulty parts and check that they function
correctly before operating the mower.
OPERATING THE MOWER
Summary of Contents for R3240T
Page 2: ......
Page 4: ......
Page 69: ...1 69 1 69 TRANSMISSION BRAKE HYDRAULIC CIRCUIT DIAGRAM 23 ...
Page 74: ...1 74 1 74 NOTES ...
Page 75: ...1 75 1 75 NOTES ...
Page 76: ...1 76 1 76 NOTES ...
Page 77: ...1 77 1 77 NOTES ...
Page 80: ......