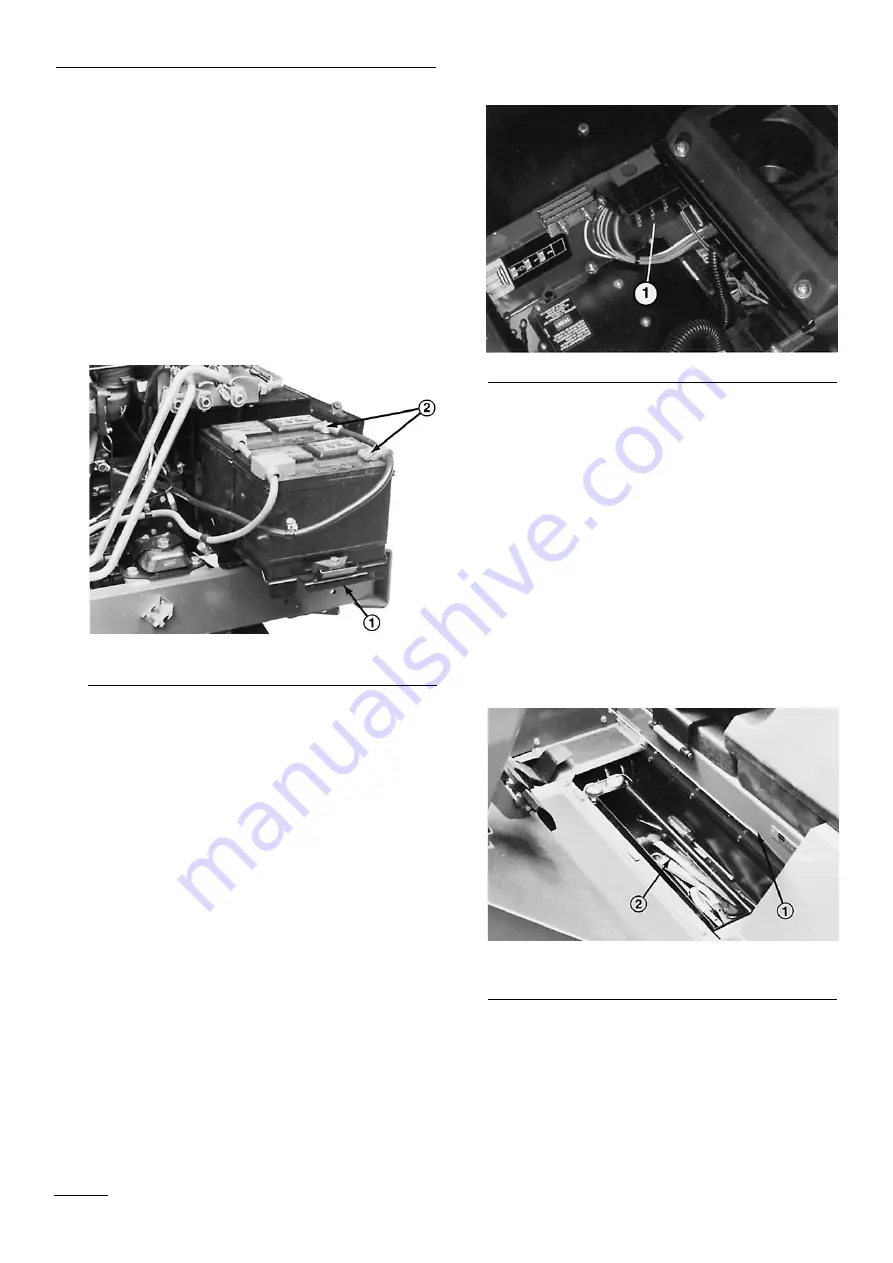
2.
Remove the capscrews securing the battery tray to
the machine and slide the tray out (Fig. 51).
3.
Check both batteries for charge with a hydrometer.
If the batteries check acceptably, slide the tray back
in place, secure with capscrews and install the side
panel. If the batteries require charging, proceed to
step 4.
4.
Remove the negative (–) battery cable connectors
from the batteries (Fig. 51). Connect a 3- to 4-amp
battery charger to the posts. Charge the batteries at a
rate of 3 to 4 amperes for 4 to 8 hours.
Figure 51
1.
Battery tray
2.
Negative (–) cable connectors
5.
When batteries are fully charged, disconnect charger
from electrical outlet and battery posts.
6.
Connect the negative (–) cable ends, slide the tray
back in place, and secure it with capscrews. Install
the side panel, close the hood and secure both with
latches.
FUSES & CIRCUIT BREAKER
One 5 amp, two 15-amp fuses and a fusible link are
incorporated for the protection of the entire wiring circuit.
The link can be replaced if the total loss of electrical
function results. They are located under the control panel to
the right of the seat (Fig. 52). If total loss of electrical
function occurs, find and correct the malfunction before
replacing the fusible link.
Figure 52
1.
Fuse block
IMPORTANT: Do not install the fuses in the fuse block
on the left side of the instrument control panel. Fuses
should be installed in this fuse block only if the machine
is equipped with a road light kit.
BRAKE SYSTEM SERVICE
Check the brake fluid level every 50 hours operation.
Replace fluid every 1000 hours operation, or yearly.
Replenish the system with DOT 3 hydraulic brake fluid. To
check the fluid level:
1.
Raise the floor panel in the front of the seat
(Fig. 53). Remove the tool tray.
Figure 53
1.
Floor plate
2.
Tool tray
2.
Snap the cover bail off the cover and remove the
cover from the master cylinder (Fig. 54).
Maintenance
38
Summary of Contents for GROUNDSMASTER 580-D 30581
Page 28: ...Maintenance 28 Figure 31 Figure 31...
Page 48: ......