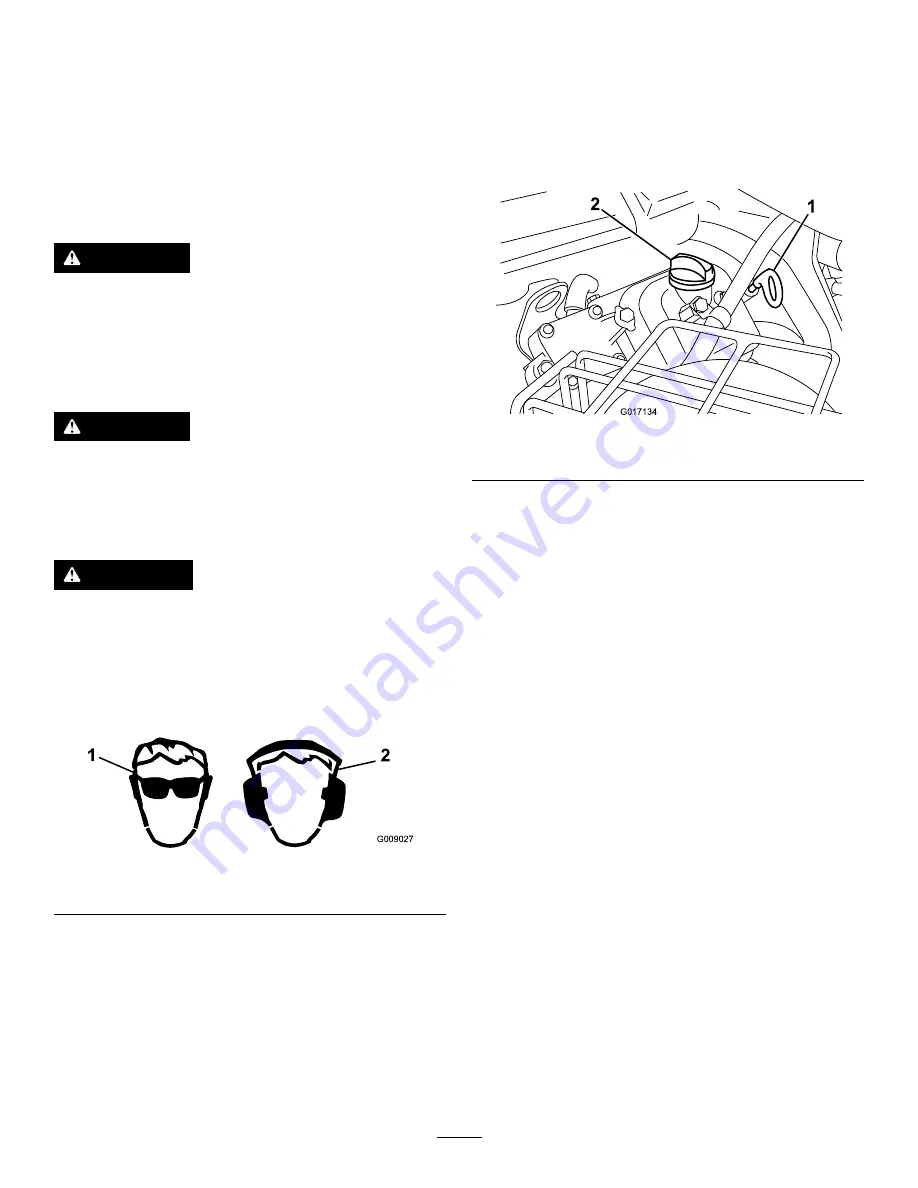
Operation
Note:
Determine the left and right sides of the machine
from the normal operating position.
Think Safety First
Carefully read all safety instructions and symbols in the
safety section. Knowing this information could help you or
bystanders avoid injury.
DANGER
Operating the machine on wet grass or steep slopes
can cause sliding and loss of control.
•
Reduce speed and use extreme caution on
slopes.
•
Do not operate the machine near water.
DANGER
Wheels dropping over edges can cause rollovers,
which may result in serious injury, death, or
drowning.
Do not operate the machine near drop-offs.
CAUTION
This machine produces sound levels that can cause
hearing loss through extended periods of exposure.
Wear hearing protection when operating this
machine.
Use of protective equipment for eyes, ears, hands, feet, and
head.
G009027
1
2
Figure 20
1.
Wear eye protection.
2.
Wear hearing protection.
Checking the Engine Oil
Service Interval:
Before each use or daily
The engine is shipped with 1.4 L (1.5 US qt) (w/filter) of oil
in the crankcase; however, you must check the oil level before
and after starting the engine the first time.
The engine uses any high-quality detergent oil having the
American Petroleum Institute (API) service classification of
SG, SH, or SJ or higher. The recommended viscosity (weight)
is SAE 30.
1.
Position the machine on a level surface and stop the
engine. Wait a few minutes before checking the oil.
2.
Pull the dipstick out and wipe it with a clean rag. Push
the dipstick into the tube and make sure it is seated
fully (
G017134
1
2
Figure 21
1.
Filler cap
2.
Dipstick
3.
Pull the dipstick out of the tube and check the oil level.
4.
If the oil level is low, remove the filler cap from the
valve cover and pour oil into the opening in the valve
cover until the oil level is within the hatch marks on the
dipstick. Add the oil slowly and check the level often
during this process.
Do not overfill.
5.
Install the filler cap and dipstick firmly in place.
Filling the Fuel Tank
•
Fuel tank capacity:
26.6 L (7 US gallons)
•
Recommended Fuel:
–
For best results, use only clean, fresh (less than 30
days old), unleaded gasoline with an octane rating of
87 or higher ((R+M)/2 rating method).
–
Ethanol
: Gasoline with up to 10% ethanol (gasohol)
or 15% MTBE (methyl tertiary butyl ether) by
volume is acceptable. Ethanol and MTBE are not the
same. Gasoline with 15% ethanol (E15) by volume
is not approved for use.
Never use gasoline that
contains more than 10% ethanol by volume
,
such as E15 (contains 15% ethanol), E20 (contains
20% ethanol), or E85 (contains up to 85% ethanol).
Using unapproved gasoline may cause performance
problems and/or engine damage, which may not be
covered under the warranty.
–
Do not
use gasoline containing methanol.
–
Do not
store fuel either in the fuel tank or fuel
containers over the winter unless you use a fuel
stabilizer.
–
Do not
add oil to gasoline.
21
Summary of Contents for Greensmaster 3150 04358
Page 45: ...Notes 45 ...
Page 46: ...Notes 46 ...