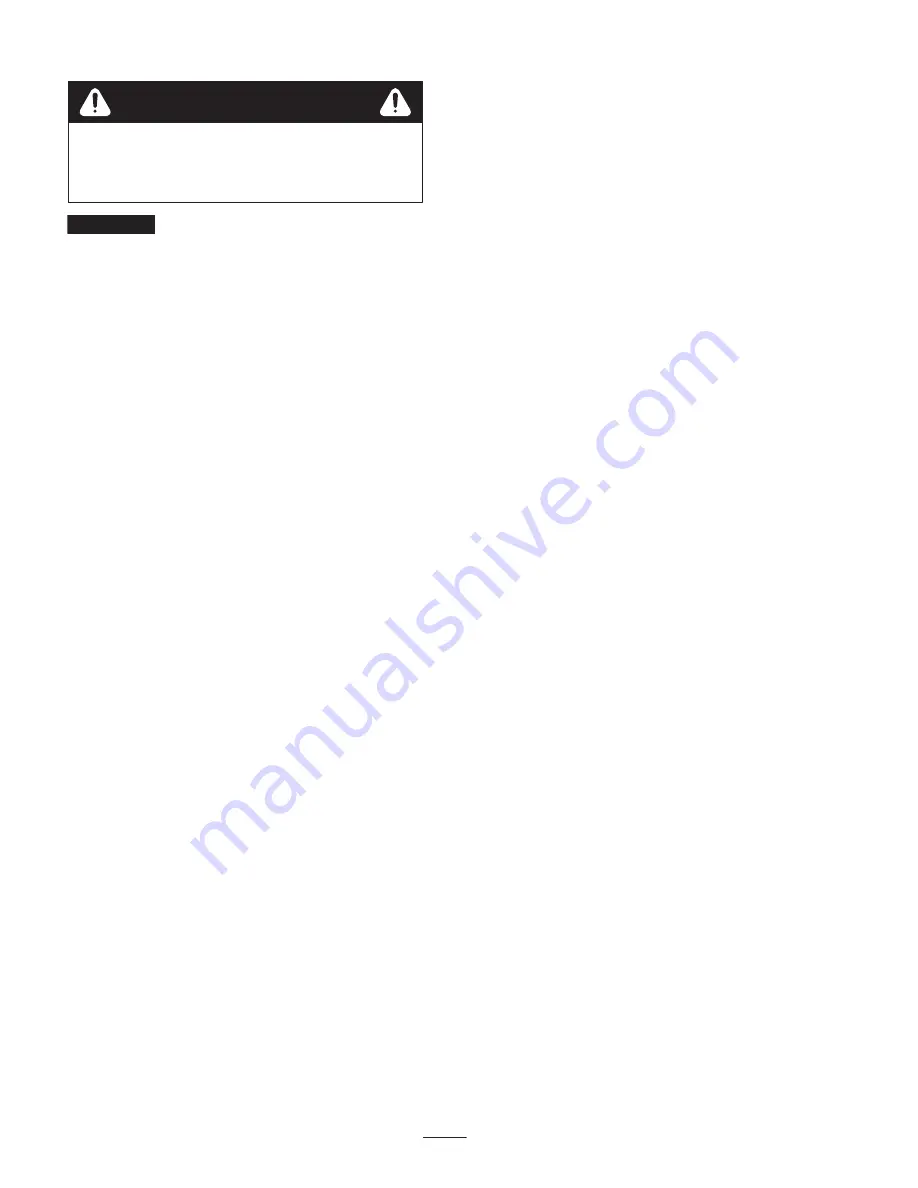
2
All Rights Reserved
Printed in the USA
W
2002 by The Toro Company
8111 Lyndale Avenue South
Bloomington, MN 55420-1196
The engine exhaust from this product contains
chemicals known to the State of California to cause
cancer, birth defects, or other reproductive harm.
Warning
Important
The engine in this product is not equipped
with a spark arrester muffler. It is a violation of California
Public Resource Code Section 4442 to use or operate this
engine on any forest-covered, brush-covered, or
grass-covered land as defined in CPRC 4126. Other states
or federal areas may have similar laws.
This spark ignition system complies with Canadian
ICES-002.
Ce système d’allumage par étincelle de véhicule est
conforme à la norme NMB-002 du Canada.
Contents
Page
Introduction
3
. . . . . . . . . . . . . . . . . . . . . . . . . . . . . . . . .
Safety
3
. . . . . . . . . . . . . . . . . . . . . . . . . . . . . . . . . . . . . .
Safe Operating Practices
3
. . . . . . . . . . . . . . . . . . . .
Toro Mower Safety
5
. . . . . . . . . . . . . . . . . . . . . . . .
Sound Pressure
6
. . . . . . . . . . . . . . . . . . . . . . . . . . . .
Sound Power
6
. . . . . . . . . . . . . . . . . . . . . . . . . . . . .
Vibration
6
. . . . . . . . . . . . . . . . . . . . . . . . . . . . . . . . .
Safety and Instruction Decals
7
. . . . . . . . . . . . . . . . .
Specifications
10
. . . . . . . . . . . . . . . . . . . . . . . . . . . . . . . .
General Specifications
10
. . . . . . . . . . . . . . . . . . . . . .
Accessories
10
. . . . . . . . . . . . . . . . . . . . . . . . . . . . . . .
Assembly
11
. . . . . . . . . . . . . . . . . . . . . . . . . . . . . . . . . . .
Activating and Charging the Battery
12
. . . . . . . . . . .
Installing the Rear Wheel Assembly
13
. . . . . . . . . . .
Mounting the Seat
13
. . . . . . . . . . . . . . . . . . . . . . . . .
Installing the Battery
13
. . . . . . . . . . . . . . . . . . . . . . .
Installing the Steering Wheel
14
. . . . . . . . . . . . . . . . .
Installing the Cutting Units
14
. . . . . . . . . . . . . . . . . .
Rear Ballast
15
. . . . . . . . . . . . . . . . . . . . . . . . . . . . . .
Before Operating
16
. . . . . . . . . . . . . . . . . . . . . . . . . . . . .
Checking the Engine Oil
16
. . . . . . . . . . . . . . . . . . . .
Filling the Gas Tank
16
. . . . . . . . . . . . . . . . . . . . . . . .
Servicing the Hydraulic System
17
. . . . . . . . . . . . . . .
Tire Pressure
18
. . . . . . . . . . . . . . . . . . . . . . . . . . . . . .
Checking the Torque of the Wheel Nuts
18
. . . . . . . .
Page
Operation
19
. . . . . . . . . . . . . . . . . . . . . . . . . . . . . . . . . . .
Think Safety First
19
. . . . . . . . . . . . . . . . . . . . . . . . . .
Controls
19
. . . . . . . . . . . . . . . . . . . . . . . . . . . . . . . . .
Break-in Period
21
. . . . . . . . . . . . . . . . . . . . . . . . . . .
Starting the Engine
21
. . . . . . . . . . . . . . . . . . . . . . . . .
Checking the Interlock System
22
. . . . . . . . . . . . . . .
Preparing the Machine for Mowing
23
. . . . . . . . . . . .
Training Period
23
. . . . . . . . . . . . . . . . . . . . . . . . . . . .
Before Mowing
23
. . . . . . . . . . . . . . . . . . . . . . . . . . .
Mowing Procedures
24
. . . . . . . . . . . . . . . . . . . . . . . .
Transport Operation
24
. . . . . . . . . . . . . . . . . . . . . . . .
Inspection and Cleanup After Mowing
25
. . . . . . . . .
Towing The Traction Unit
25
. . . . . . . . . . . . . . . . . . .
Maintenance
25
. . . . . . . . . . . . . . . . . . . . . . . . . . . . . . . . .
Recommended Maintenance Schedule
25
. . . . . . . . .
Daily Maintenance Checklist
26
. . . . . . . . . . . . . . . . .
Lubrication
27
. . . . . . . . . . . . . . . . . . . . . . . . . . . . . . .
Changing the Engine Oil and Filter
29
. . . . . . . . . . . .
Servicing the Air Cleaner
29
. . . . . . . . . . . . . . . . . . . .
Adjusting the Throttle Control
30
. . . . . . . . . . . . . . . .
Adjusting the Choke Control
30
. . . . . . . . . . . . . . . . .
Adjusting the Carburetor and Speed Control
30
. . . . .
Replacing the Spark Plugs
31
. . . . . . . . . . . . . . . . . . .
Replacing the Fuel Filter
31
. . . . . . . . . . . . . . . . . . . .
Changing the Hydraulic Oil and Filter
32
. . . . . . . . . .
Checking the Hydraulic Lines and Hoses
32
. . . . . . .
Adjusting the Brakes
32
. . . . . . . . . . . . . . . . . . . . . . .
Adjusting the Rear Camshaft
33
. . . . . . . . . . . . . . . . .
Adjusting the Lift and Mow Pedal Height
34
. . . . . . .
Leveling the Lift and Mow Pedals
34
. . . . . . . . . . . . .
Adjusting the Traction Pedal
35
. . . . . . . . . . . . . . . . .
Adjusting Cutting Unit Lift and Drop
35
. . . . . . . . . .
Adjusting the Lift Cylinders
35
. . . . . . . . . . . . . . . . .
Replacing the Seat Switch
36
. . . . . . . . . . . . . . . . . . .
Replacing the Traction Switch
36
. . . . . . . . . . . . . . . .
Replacing the Mow/Lift Switch
36
. . . . . . . . . . . . . . .
Adjusting the Traction Return Linkage
37
. . . . . . . . .
Battery Care
37
. . . . . . . . . . . . . . . . . . . . . . . . . . . . . .
Storage
38
. . . . . . . . . . . . . . . . . . . . . . . . . . . . . . . . . .
Electrical Schematic
39
. . . . . . . . . . . . . . . . . . . . . . . .
Hydraulic Schematic
40
. . . . . . . . . . . . . . . . . . . . . . .
Troubleshooting
41
. . . . . . . . . . . . . . . . . . . . . . . . . . . . . .
The Toro General Commercial Products Warranty
48
. . .
Summary of Contents for GREENSMASTER 3100
Page 28: ...28 Figure 28 Figure 29 Figure 30 Figure 31 Figure 32 Figure 33 ...
Page 46: ...46 ...
Page 47: ...47 ...