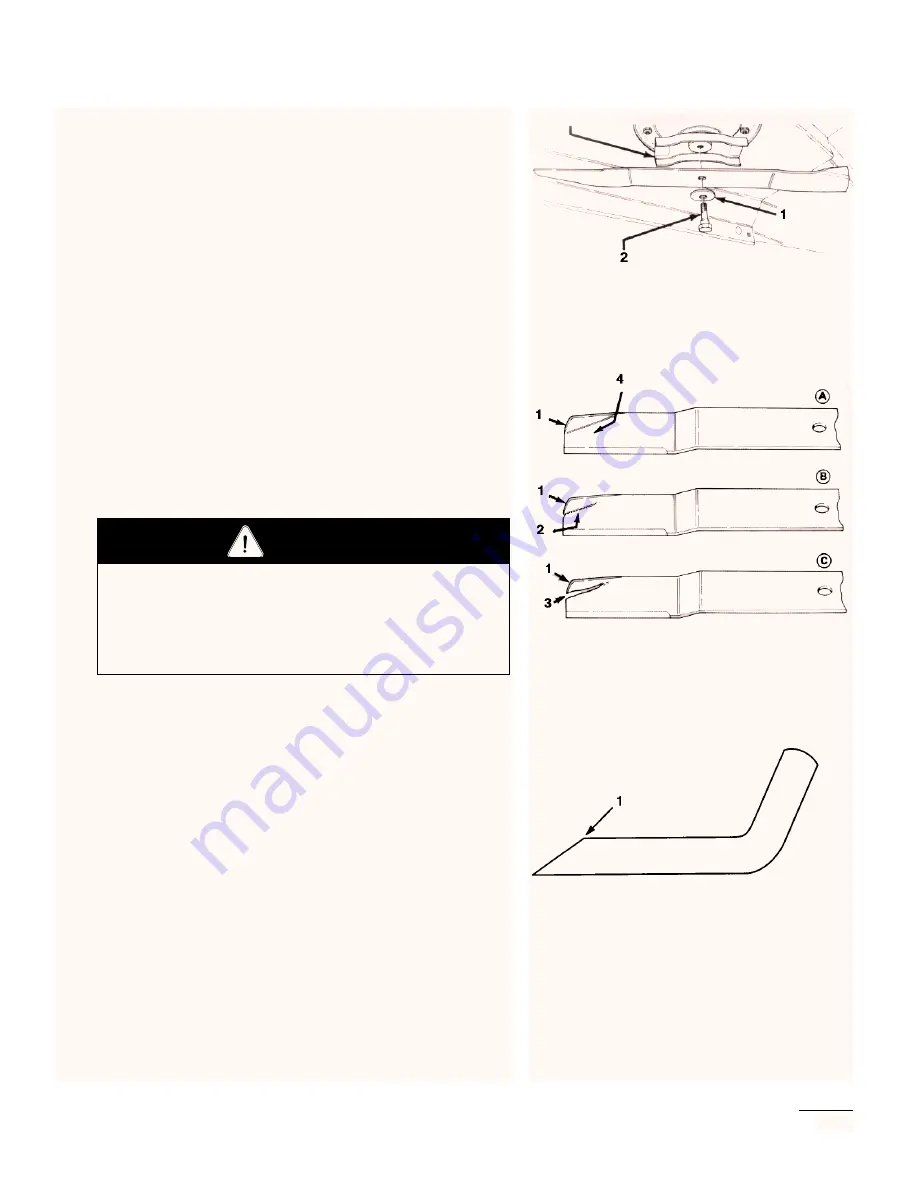
17
Figure 13
1.
Special screw
2.
Belleville washer
Figure 14
1.
Sail
2.
Wear
3.
Slot formed
4.
Flat part of blade
Figure 15
1.
Sharpen at original angle
2.
Grasp the end of the blade using a rag or thickly padded glove.
Remove the special screw, belleville washer and blade from the
spindle assembly (Fig. 13).
Tighten the special screw to 102 to 136 N-m.
INSPECTING AND SHARPENING THE
BLADE
1.
Raise the cutting unit to highest position, shut the engine off
and engage the parking brake. Block the cutting unit to pre-
vent it from falling accidentally.
2.
Examine the cutting ends of the blade carefully, especially
where the flat and curved parts of the blade meet (Fig. 14A).
Since sand and abrasive material can wear away the metal that
connects the flat and curved parts of the blade, check the blade
before using the machine. If any wear is noticed (Fig. 14B),
replace the blade: refer to Removing The Cutter Blade.
3.
Examine the cutting edges of all blades. Sharpen the cutting
edges if they are dull or nicked. Sharpen only the top side of
the cutting edge and maintain the original cutting angle to
assure sharpness (Fig. 15). The blade will remain balanced if
same amount of metal is removed from both cutting edges.
4.
To check the blade for being straight and parallel, lay it on a
level surface and check its ends. Ends of the blade must be
slightly lower than the center, and the cutting edge must be
lower than the heel of the blade. This blade will produce good
quality of cut and require minimal power from the engine. By
contrast, a blade that is higher at the ends than the center, or
the cutting edge higher than the heel of the blade is warped or
bent and must be replaced.
5.
To install the blade, assemble parts in reverse order, and make
sure the blade sail is facing up. Tighten special screw 102 to
136 Nm.
If the blade is allowed to wear, a slot will form between the
sail and the flat part of the blade (Fig. 14 C). Eventually a
piece of the blade may break off and be thrown from under
the housing, possibly resulting in serious injury to yourself
or to bystanders.
WARNING
Summary of Contents for 30710 Groundsmaster 300
Page 20: ......