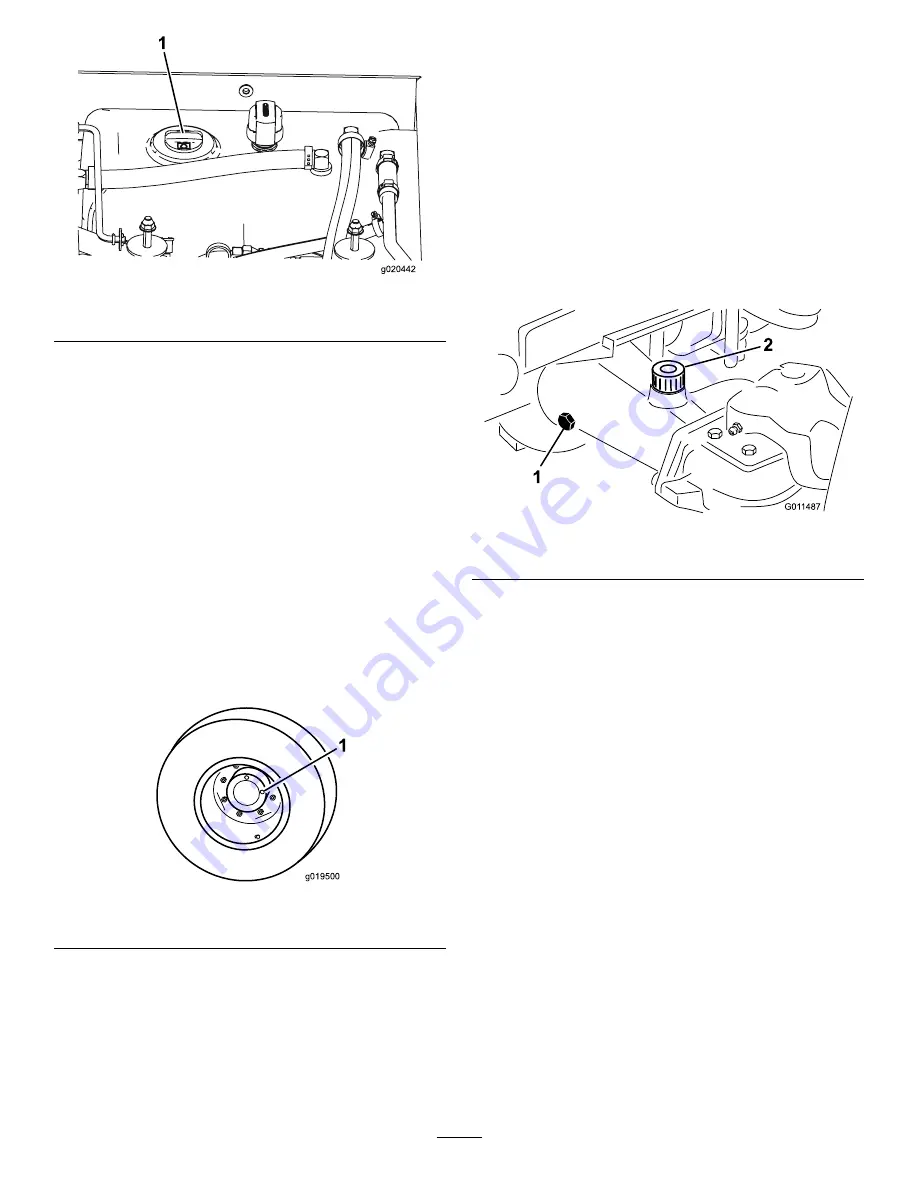
Figure 13
1.
Hydraulic tank cap
4.
Remove the dipstick from the filler neck and wipe it
with a clean rag. Insert the dipstick into the filler neck;
then remove it and check the fluid level. The fluid level
should be between the 2 marks on the dipstick.
5.
If the level is low, add the appropriate fluid to raise the
level to the upper mark.
6.
Install the dipstick and cap onto the filler neck.
Checking the Planetary Gear Drive Oil
Service Interval:
Every 400 hours
Check the oil level after every 400 hours of operation or if
external leakage is noted. Use high quality SAE 85W-140 gear
lube as a replacement.
1.
With machine on level surface, position the wheel so
one check plug (
) is at the 12 o'clock position
and the other is at 3 o'clock position.
g019500
Figure 14
1.
Check/drain plug (2)
2.
Remove the plug at the 3 o’clock position (
Oil level should be at the bottom of the check plug
hole.
3.
If the oil level is low, remove the plug at the 12 o’clock
position and add oil until it begins to flow out of the
hole at the 3 o’clock position.
4.
Install both plugs.
Checking the Rear Axle Lubricant
Service Interval:
Every 400 hours
The rear axle is filled with SAE 85W-140 gear lube. Check the
oil level before the engine is first started and every 400 hours
thereafter. The capacity is 2.4 L (80 oz). Visually inspect for
leaks daily.
1.
Position the machine on a level surface.
2.
Remove a check plug from one end of the axle (
) and make sure that the lubricant is up to the bottom
of the hole. If the level is low, remove the fill plug
(
) and add enough lubricant to bring the level
up to the bottom of the check plug holes.
Figure 15
1.
Check plug
2.
Fill plug
Checking the Rear Axle Gear Box
Lubricant
Service Interval:
Every 400 hours
The gear box is filled with SAE 85W-140 gear lube. Check the
oil level before the engine is first started and every 400 hours
thereafter. The capacity is 0.5 L (16 oz). Visually inspect for
leaks daily.
1.
Position the machine on a level surface.
2.
Remove the check/fill plug from the left side of the
gear box (
) and make sure that lubricant is
up to the bottom of the hole. If the level is low, add
enough lubricant to bring the level up to the bottom
of the hole.
27