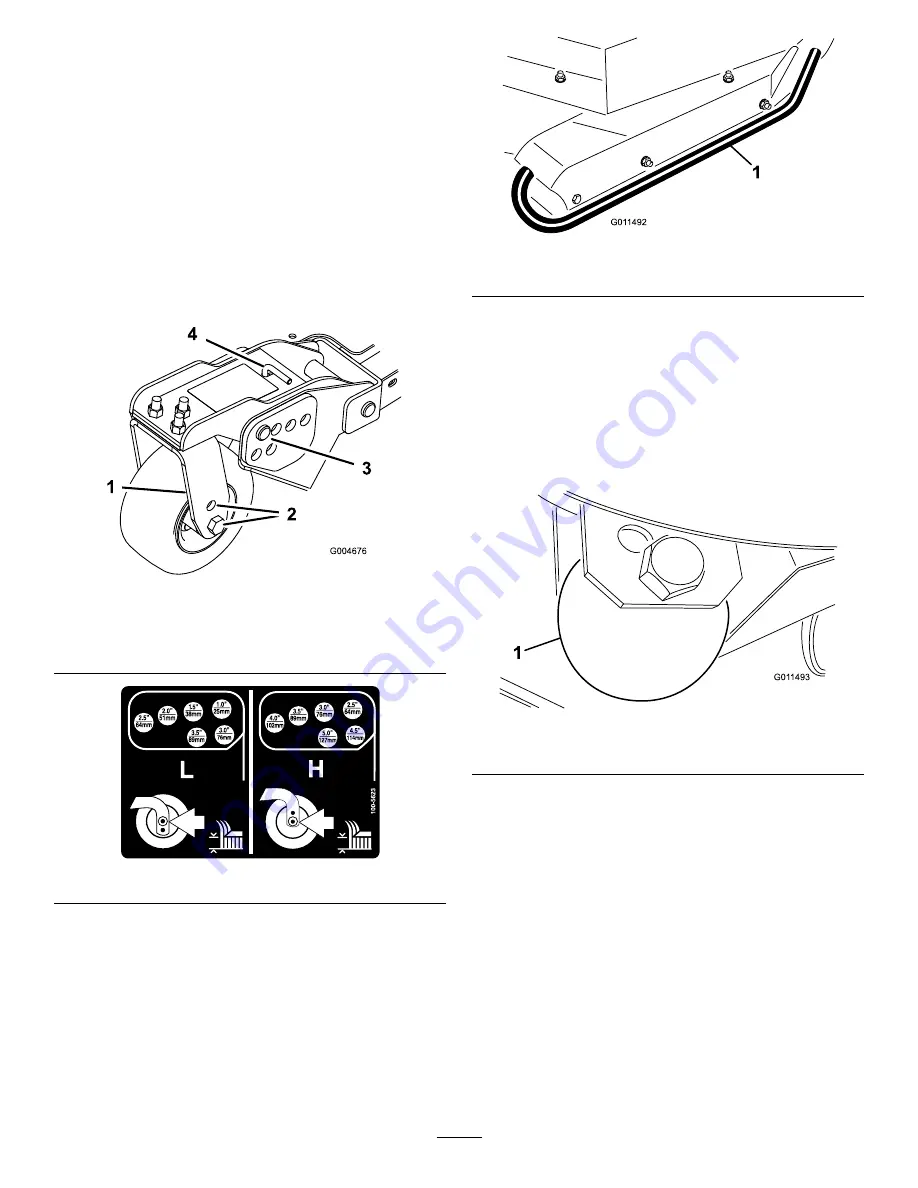
3.
Push the castor spindle through the castor arm. Install
the shims (as originally installed) and the remaining
spacers onto the spindle shaft. Install the tensioning
cap to secure the assembly.
4.
Remove the hairpin cotter and clevis pins from the
castor pivot arms (
5.
Rotate tension rod to raise or lower pivot arm until
holes are aligned with selected height-of-cut bracket
holes in the cutting unit frame (
and
6.
Insert the clevis pins and install the hairpin cotters.
7.
Rotate tension rod counterclockwise (finger tight) to
put tension on adjustment.
Figure 21
1.
Castor pivot arm
3.
Clevis pin and hair pin
cotter
2.
Axle mounting holes
4.
Tension rod
Figure 22
Adjusting the Skids
The skids should be mounted in the lower position when
operating at heights of cut greater than 64 mm (2-1/2 inches)
and in the higher position when operating at heights of cut
lower than 64 mm (2-1/2 inches).
Adjust the skids by removing the flange bolt and nuts,
positioning them as desired, and installing the fasteners
(Figure 24).
Figure 23
1.
Skid
Adjusting the Cutting Unit Rollers
The cutting unit rollers should be mounted in the lower
position when operating in height of cuts greater than 64 mm
(2-1/2 inches) and in the higher position when operating in
height of cuts lower than 64 mm (2-1/2 inches).
1.
Remove the bolt and nut securing the gage wheel to
the cutting unit brackets (
Figure 24
1.
Gage wheel
2.
Align the roller and spacer with the top holes in the
brackets and secure them with the bolt and nut.
Adjusting the Blade
To ensure proper operation of the cutting unit, there must be
10-16 mm (0.38-0.62 inch) clearance between the tips of the
wing and center cutting unit blades (
).
1.
Raise cutting unit so blades are visible and block center
deck section so it cannot fall accidentally. Wing decks
must be horizontal to center cutting unit.
2.
Rotate a center and adjoining wing blade so there blade
tips are aligned. Measure distance between blade tips,
distance should be approximately 10-16 mm (0.38-0.62
inch) (
29