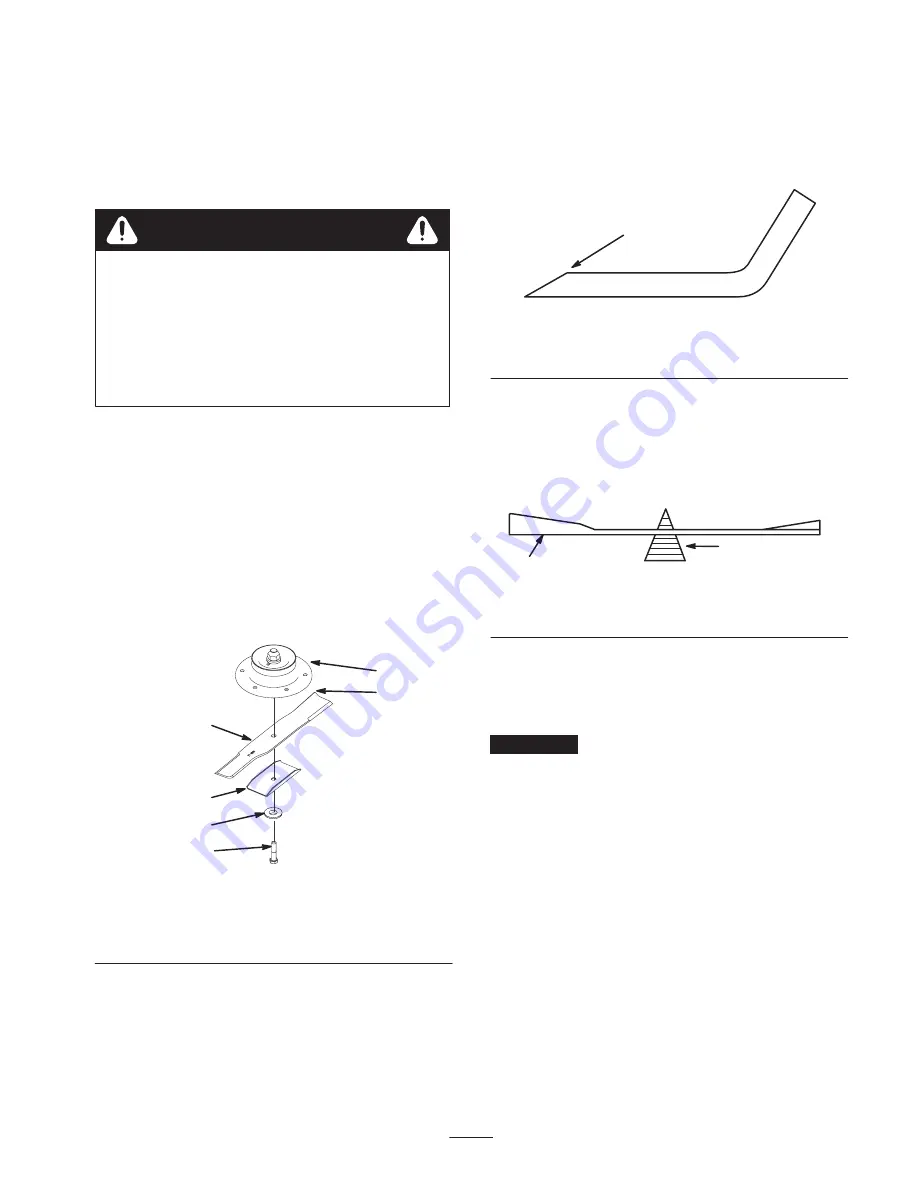
37
3. Measure from a level surface to the cutting edge of the
blades at the same position as in step 1. The difference
between the dimensions obtained in steps 1 and 2 must
not exceed 1/8 inch (3 mm). If this dimension exceeds
1/8 inch (3 mm), the blade is bent and must be replaced.
Refer to Removing the Blades, and Installing the Blades
on page 37.
A blade that is bent or damaged could break apart
and could seriously injure or kill you or
bystanders.
•
Always replace bent or damaged blade with a
new blade.
•
Never file or create sharp notches in the edges
or surfaces of blade.
Warning
Removing the Blades
Blades must be replaced if a solid object is hit, if the blade
is out of balance or is bent. To ensure optimum
performance and continued safety conformance of the
machine, use genuine TORO replacement blades.
Replacement blades made by other manufacturers may
result in non-conformance with safety standards.
1. Hold the blade end using a rag or thickly-padded glove.
Remove the blade bolt, blade stiffener, washer, and
blade from the spindle shaft (Fig. 51).
1
3
2
4
5
m–6368
6
Figure 51
1.
Sail Area of Blade
2.
Blade
3.
Blade spindle
4.
Blade Bolt
5.
Blade stiffener
6.
Flat washer
Sharpening the Blades
1. Use a file to sharpen the cutting edge at both ends of the
blade (Fig. 52). Maintain the original angle. The blade
retains its balance if the same amount of material is
removed from both cutting edges.
1
m–1854
Figure 52
1.
Sharpen at original
angle
2. Check the balance of the blade by putting it on a blade
balancer (Fig. 53). If the blade stays in a horizontal
position, the blade is balanced and can be used. If the
blade is not balanced, file some metal off the end of the
sail area only
(Fig. 51).
Repeat this procedure until the
blade is balanced.
1
2
m–1855
Figure 53
1.
Blade
2.
Balancer
Installing the Blades
1. Install the blade onto the spindle shaft
(Fig. 51).
Important
The sail part of the blade must be pointing
upward, toward the inside of the mower to ensure proper
cutting
(Fig. 51).
2. Install the blade stiffener, flat washer and blade bolt
(Fig. 51).
Torque the blade bolt to 85–110 ft-lb
(115–140 N
m).
Correcting the Mower Quality
of Cut
If one deck blade cuts lower than the other, correct as
follows.
Note:
Tire air pressure is critical in these procedures.
Make sure all tires have correct pressure.
1. Disengage the PTO and set the parking brake.