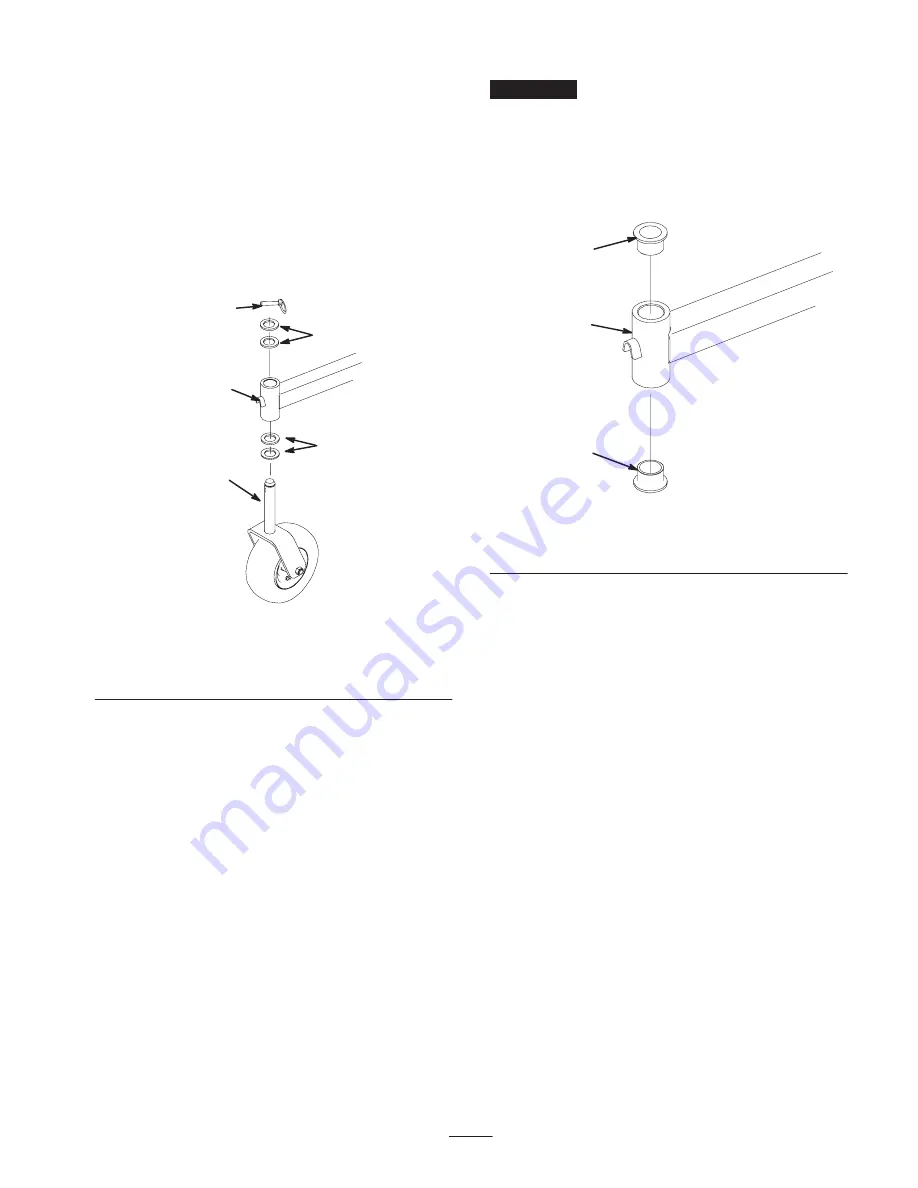
39
1. Raise the cutting unit so the castor wheels are off the
floor, then block up the front of the mower with jack
stands.
2. Remove the locking pin and spacer(s) from the top of
the castor wheel fork (Fig. 64).
3. Pull the castor wheel fork out of the mounting tube,
leaving the spacer(s) on the bottom of the fork.
Remember the location of the spacers on each fork to
ensure correct installation, and to maintain a level
deck.
4
2
1
3
2
m-5198
Figure 64
1.
Locking Pin
2.
spacers (locate as
required)
3.
Carrier Frame Mounting
Tube
4.
Castor Wheel Fork
4. Insert a pin punch into the mounting tube and carefully
drive out the bushings (Fig. 65). Clean the inside of
the mounting tube.
5. Grease the inside and outside of the new bushings. Use
a hammer and flat plate to carefully drive the bushings
into the mounting tube.
6. Inspect the castor wheel fork for wear and replace if
necessary (Fig. 64).
7. Slide the castor wheel fork through the bushings in the
mounting tube. Replace the spacer(s) onto the fork and
secure with the retaining ring (Fig 64).
Important
The inside diameter of the bushings may
collapse slightly when installed. If the castor wheel fork
does not slide into the new bushings, ream both bushings
to an inside diameter of 1.126 in. (28.6mm).
8. Grease the fitting on the carrier frame mounting tube
using No. 2 general purpose lithium base or
molybdenum base grease.
2
2
1
m–5197
Figure 65
1.
Carrier Frame Mounting
Tube
2.
Bushing
Castor Wheel and Bearings
Service
The castor wheels rotate on a roller bearing supported by a
spanner bushing. If the bearing is kept well lubricated,
wear will be minimal. Failure to keep the bearing well
lubricated will cause rapid wear. A wobbly castor wheel
usually indicates a worn bearing.
1. Remove the locknut and wheel bolt holding the castor
wheel to the castor fork (Fig. 66).
2. Remove one bushing, then pull the spanner bushing
and roller bearing out of the wheel hub (Fig. 66).
3. Remove the other bushing from the wheel hub and
clean any grease and dirt from the wheel hub (Fig. 66).
4. Inspect the roller bearing, bushings, spanner bushing
and inside of the wheel hub for wear. Replace any
defective or worn parts (Fig. 66).
Summary of Contents for 30257
Page 7: ...7 Slope Chart...
Page 8: ...8...
Page 11: ...11 104 8171 105 0884 104 8180...
Page 45: ......
Page 46: ......
Page 47: ......