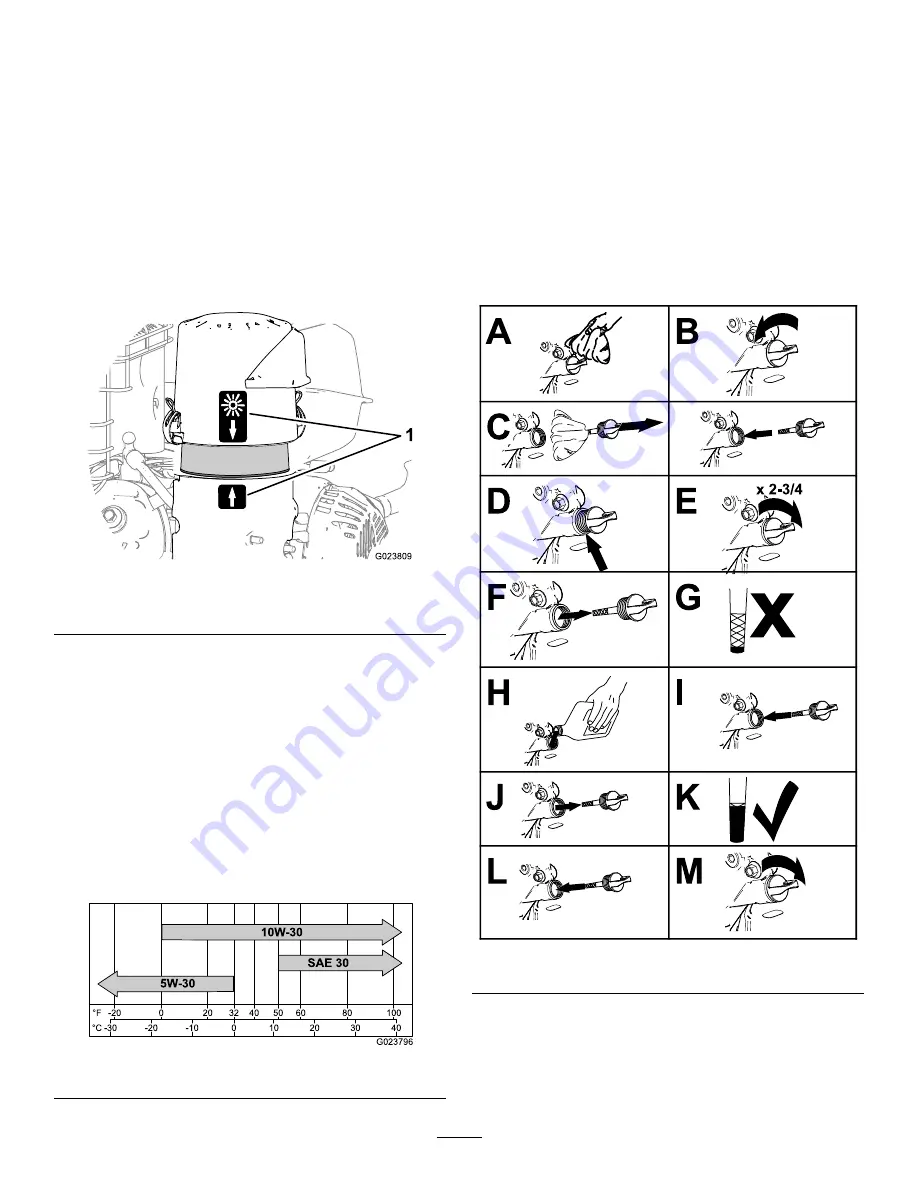
5.
Wipe dirt away from the base and the cover with
a moist rag.
Note:
Be careful to prevent dirt and debris from
entering the air duct leading to the carburetor.
6.
Install the foam pre-cleaner onto the paper air
filter (
).
Note:
Use a new paper air filter if you discarded
the old one.
7.
Install the air filter assembly to the air-filter base
(
).
8.
Align the arrow decal on the air-cleaner cover
and the arrow decal on the base (
).
g023809
Figure 33
1.
Alignment-arrow decal (normal ambient air position shown)
9.
Secure the air-filter cover to the base with the
latches.
Servicing the Engine Oil
Engine-Oil Specifications
Oil Type:
Detergent oil (API service SJ or later)
Engine Oil Capacity:
1.7 L (1.8 US qt) without the
filter; 1.5 L (1.6 US qt) with the filter.
Oil viscosity:
Refer to the table below.
g023796
Figure 34
Checking the Engine-Oil Level
Service Interval:
Before each use or daily
Important:
Do not operate the engine with the oil
level below the Low (or Add) mark on the dipstick,
or over the Full mark.
1.
Move the machine to a level surface.
2.
Shut off the engine, engage the parking brake,
remove the key, and wait for all moving parts to
stop before leaving the operating position.
3.
Allow the engine to cool.
4.
Check the engine-oil level as shown in
g249636
Figure 35
5.
If the oil level is low, wipe off the area around
the oil fill cap, remove cap and add the specified
oil until the oil level is at the Full mark on the
dipstick.
Note:
Do not
overfill the engine with oil.
32