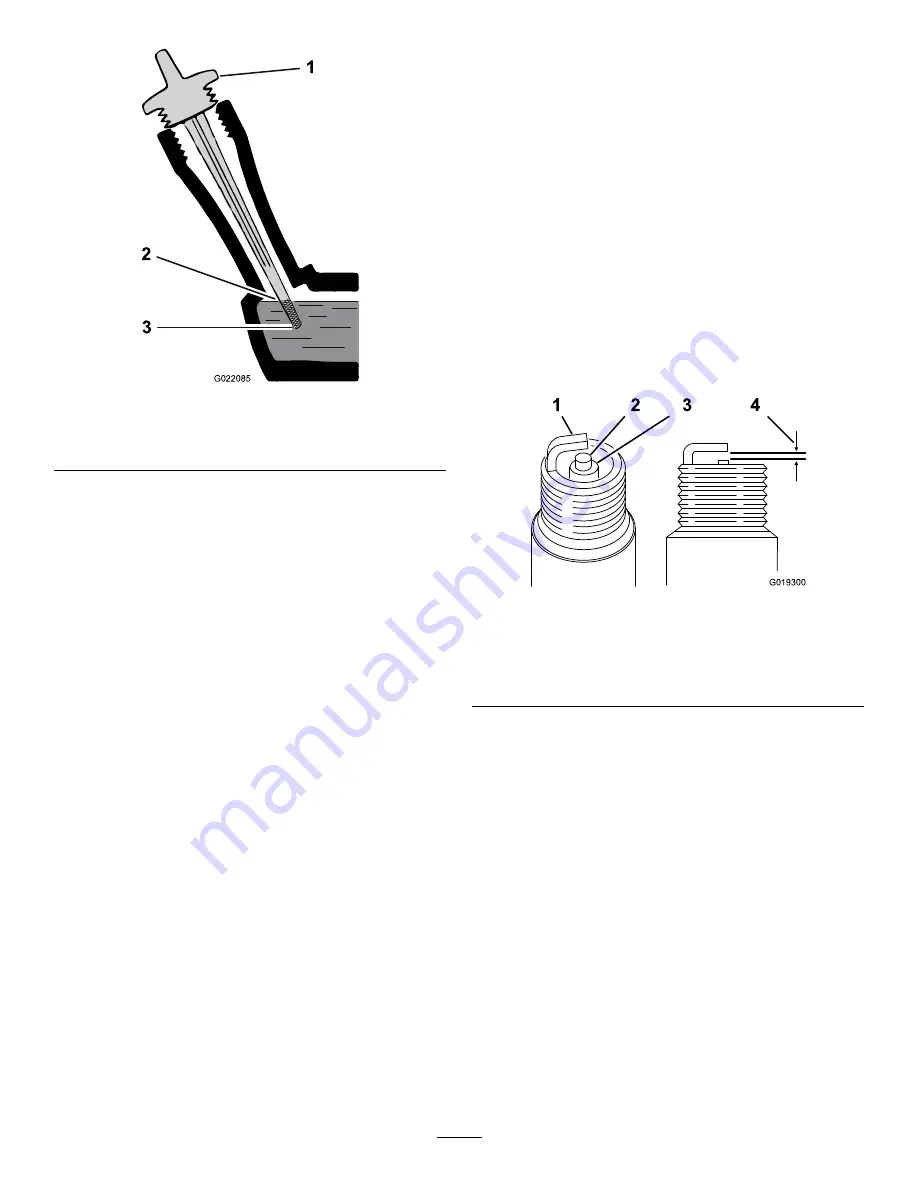
1
2
3
G022085
Figure 29
1.
Dipstick
3.
Lower-limit mark
2.
Upper-limit mark
9.
Install the dipstick securely.
10.
Recycle the used oil according to local codes.
Servicing the Spark Plug
Service Interval:
Every 100 hours—Inspect and adjust the
spark plug; replace it if necessary.
Every 200 hours—Replace the spark plug.
Use an
NGK BPR5ES
spark plug or equivalent.
1.
Stop the engine and wait for all moving parts to stop.
2.
Disconnect the wire from the spark plug.
3.
Clean around the spark plug.
4.
Remove the spark plug from the cylinder head.
Important:
Replace a cracked, fouled, or dirty
spark plug. Do not clean the electrodes, because
grit entering the cylinder can damage the engine.
5.
Set the gap on the plug to 0.7 to 0.8 mm (0.028 to
0.031 inch); refer to Figure 30.
G019300
1
2
4
3
Figure 30
1.
Side electrode
2.
Center electrode
3.
Insulator
4.
0.7 to 0.8 mm (0.028 to 0.031 inch) gap
6.
Carefully install the spark plug by hand (to avoid cross
threading) until it is hand tight.
7.
Tighten the spark plug an additional 1/2 turn if it is
new; otherwise, tighten it an additional 1/8 to 1/4 turn.
Important:
A loose spark plug can become very
hot and can damage the engine; overtightening a
spark plug may damage the threads in the cylinder
head.
8.
Connect the wire to the spark plug.
19