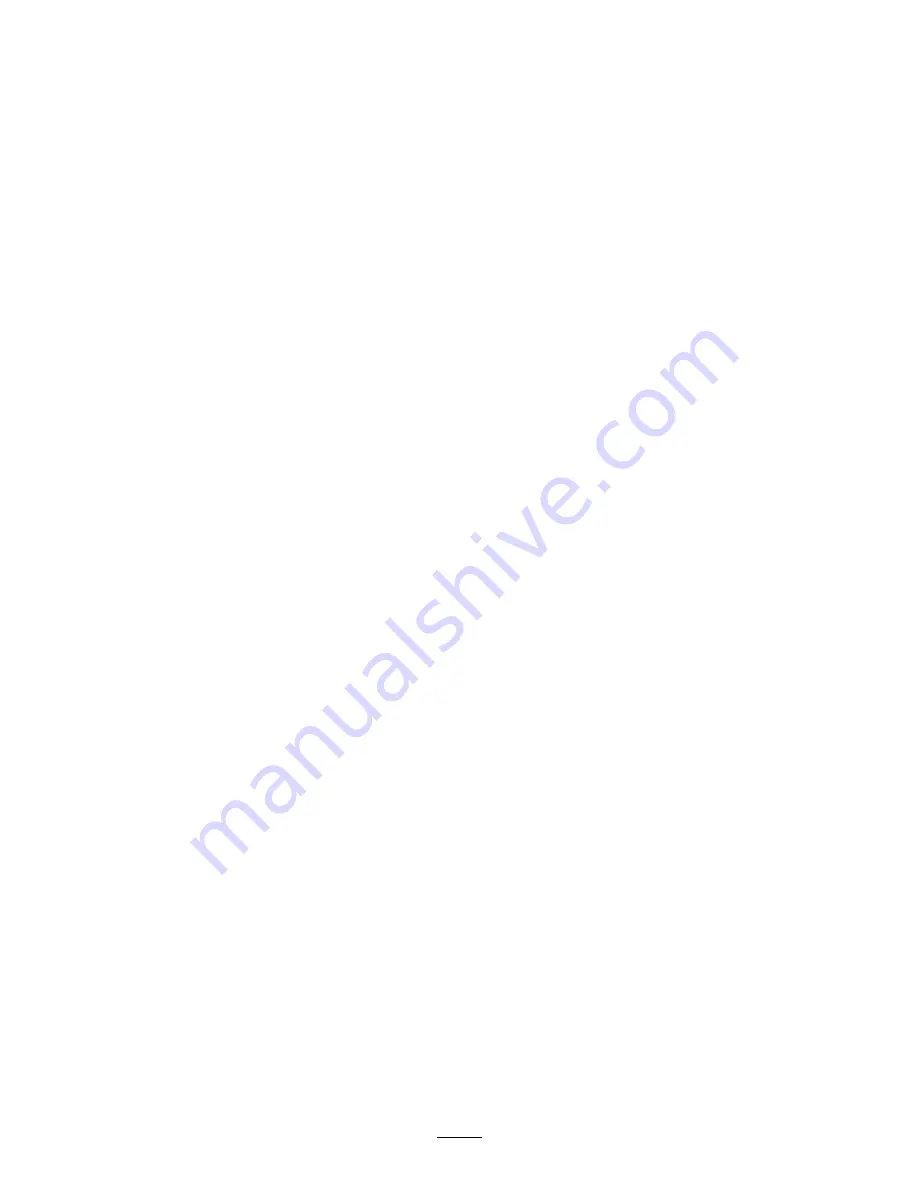
Replacing the Headlight
When removing or replacing the headlight assembly,
disconnect the wiring harness to the bulb assembly if the bulb
is to be removed with the lamp.
1.
Remove the speed clips and washers securing the
headlight in place.
Note:
Retain all of the parts.
2.
Remove the headlight assembly by moving it forward
through the opening in the front bumper (Figure 31).
3.
Install the new headlight through the opening in the
bumper (Figure 31).
4.
Ensure that the adjustment posts are lined up with the
holes in the mounting bracket in the bumper.
5.
Secure the headlight assembly with the washers and
speed clips removed previously.
6.
Attach the headlight to the wire harness removed
previously.
7.
Adjust the headlights to direct the beams to the desired
position.
Adjusting the Headlights
Use the following procedure to adjust the headlight beam
position whenever a headlight assembly is replaced or
removed.
1.
Turn the key to the On position and turn on the
headlights.
2.
At the headlight assembly, use the fasteners to pivot the
headlight assembly and affect the cast-beam position.
Drive System
Maintenance
Inspecting the Tires
Service Interval:
Every 100 hours
Every 100 hours
Check the tire condition at least every 100 hours of operation.
Operating accidents, such as hitting curbs, can damage a
tire or rim and also disrupt wheel alignment, so inspect tire
condition after an accident.
Check the wheels to ensure that they are mounted securely.
Torque the lug nuts to 61 to 88 N-m (45 to 65 ft-lb).
Adjusting the Front Wheel
Toe-in and Camber
Service Interval:
Every 100 hours/Yearly (whichever comes
first)—Check the front wheel toe-in and
camber.
Important:
You will need to obtain tool number
TORO 6010 from your Toro Distributor to perform this
procedure.
The toe-in should be 0 to 6 mm (0 to 1/4 inch) and the
camber should be 0+1/2 degree, i.e., the bottom of the wheel
rims angled in 2.3 mm (0.09 inch) more than the top, with the
following parameters:
•
Check the tire pressure to ensure that the front tires are
inflated to 82 kPa (12 psi).
•
Either, add weight to the driver's seat equal to the average
operator who will run the machine, or have an operator
sit on the seat. The weight or operator must remain on
the seat for the duration of the procedure.
•
On a level surface, roll the machine straight back 2 to 3
m (6 to 10 ft) and then straight forward to the original
starting position. This will allow the suspension to settle
into the operating position.
•
Measure the toe-in with the wheels facing straight ahead.
1.
To check the camber, place a 90 degree square on the
ground with the vertical edge touching the face of the
tire (Figure 32).
30