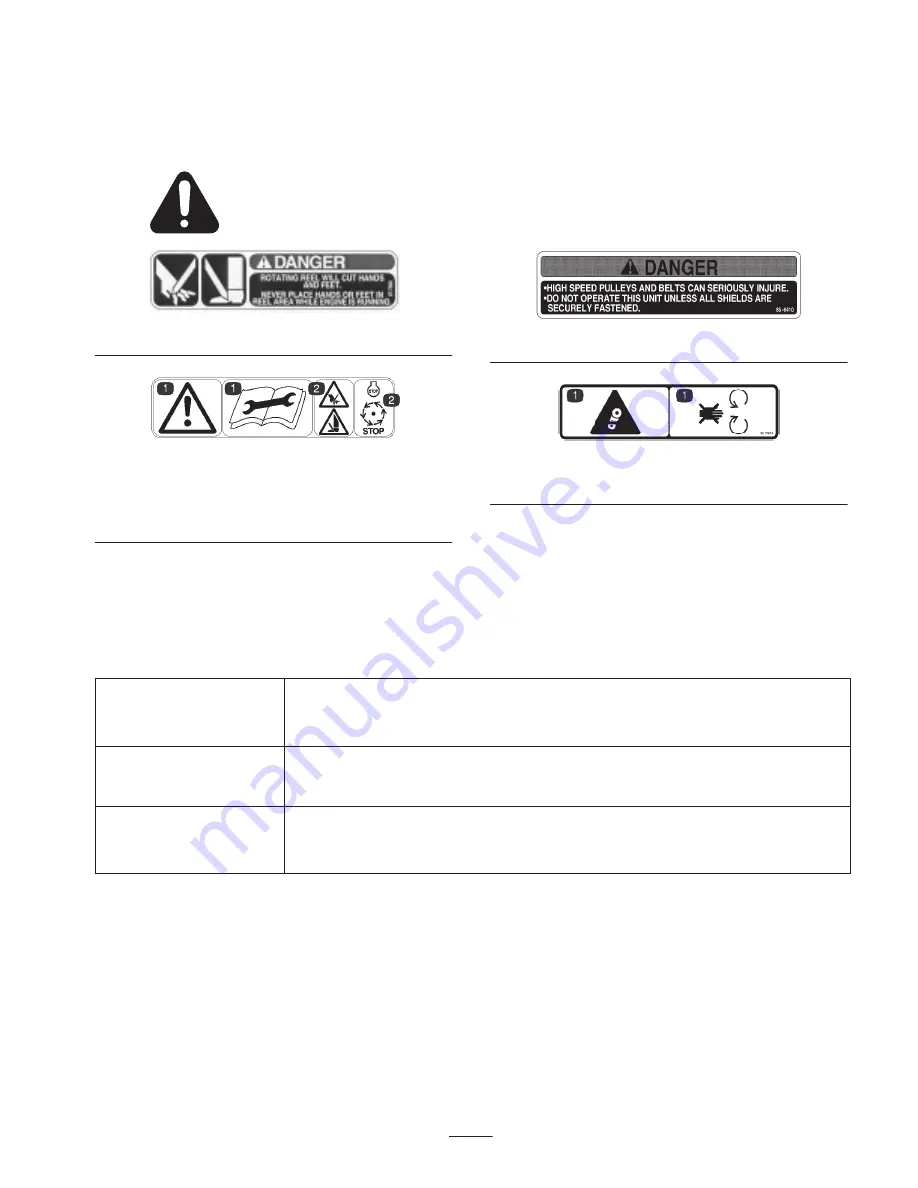
3
Safety
Safety and Instruction Decals
Safety decals and instructions are easily visible to the operator and are located near any
area of potential danger. Replace any decal that is damaged or lost.
Part No. 67-7960
Part No. 93-6688 (for CE)
1.
Danger—read the
operator’s manual before
performing maintenance.
2.
Cutting hazard to hands,
fingers, and feet—stop the
engine before going near
rotating reels.
Part No. 85-6410
Part No. 93-7814 (for CE)
1.
Entanglement hazard—stay away from moving parts.
Specifications
General Specifications
Height-of-cut
5 Blade—1 to 3 in. (25 to 76 mm)
7 Blade—1/2 to 1-3/4 in. (9.5 to 45 mm)
11 Blade—3/8 to 3/4 in. (9.5 to 19 mm)
Height-of-cut adjustment
Quick adjustment and positive locking is provided by locking type cone nuts.
Gauge marks of 1/4 in. (6.3 mm) are provided as a reference for easy changes of
height-of-cut.
Clip (variable to match
cutting conditions)
5 Blade Cutting Unit: .176 in. per mph (.352 in. at 2 MPH-1.32 in. at 7.5 mph)
7 Blade Cutting Unit : .126 in. per mph (.252 in. at 2 MPH-.945 in. at 7.5 mph)
11 Blade Cutting Unit: .080 in. per mph (.16 in. at 2 MPH-.600 in. at 7.5mph)