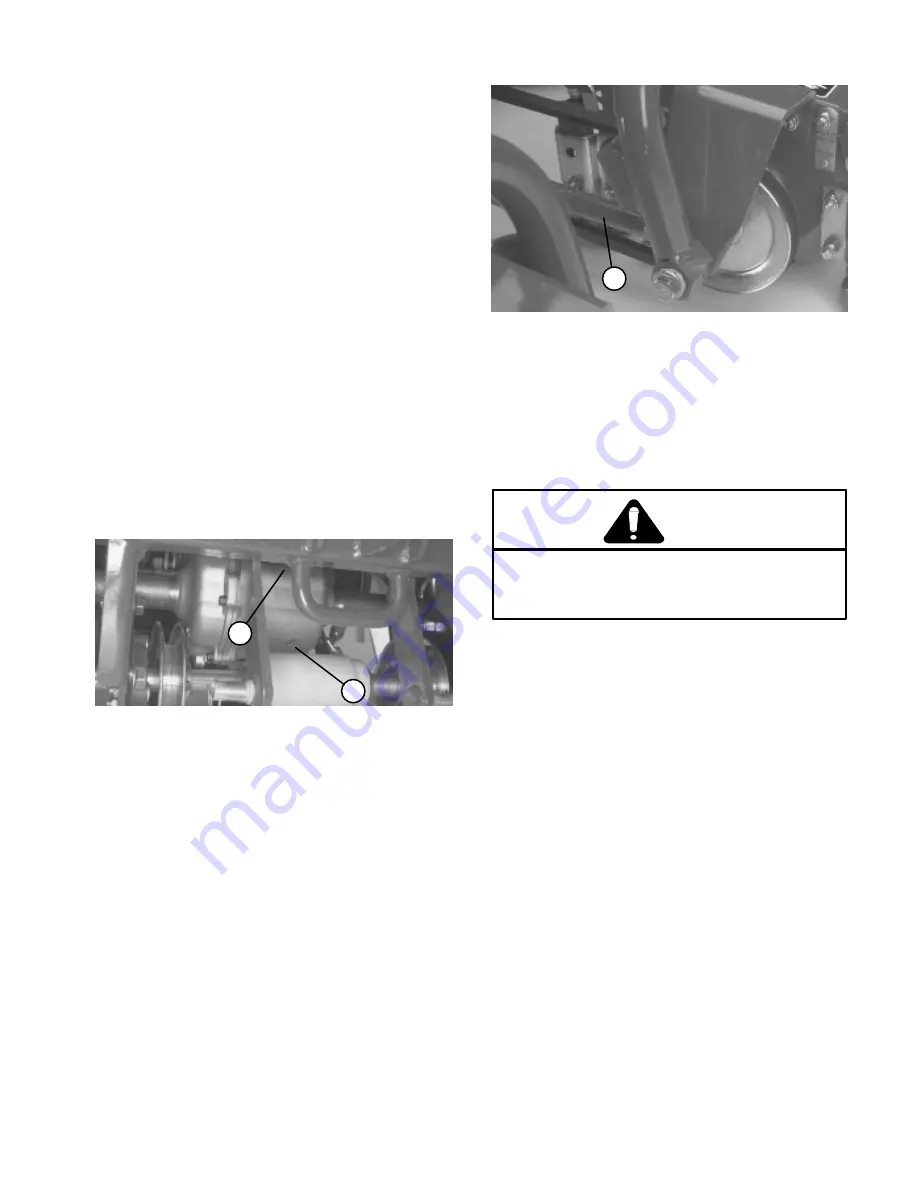
35
MAINTENANCE
1.
Remove hydraulic oil filter from mounting head.
Use bottom type filter wrench. Dispose of filter
properly.
2.
Apply a film of oil on the gasket. Install filter by hand
until gasket contacts mounting head; then tighten filter
an additional 3/4 turn.
3.
Start engine and check for oil leaks. Allow engine
to run for about 2 minutes so any air in system is
purged. Then shut engine off.
4.
Check level of oil in reservoir; refer to Check
Hydraulic System Fluid.
CHANGING FRONT AXLE OIL
(Fig. 78)
After every 400 hours of operation, change oil in the
front axle.
1.
Drive machine around for five minutes before
changing oil to warm axle oil. Warm oil flows more
freely and carries more contaminants than cold oil.
2.
Clean area around drain plug and place a drain
pan below drain plug on axle.
Figure 78
1. Drain plug
2. Fill plug
1
2
3.
Remove drain plug and allow oil to flow into drain
pan . After oil is drained, reinstall drain plug.
4.
Remove fill plug and fill to plug level with ISO
150/220 (SAE EPĆ90) oil (approximately 44 oz.).
ADJUSTING CUTTING UNIT BELTS
(Fig. 79)
Make sure belts are properly tensioned to assure
proper operation of the machine and prevent
unnecessary wear. Check all belts midway in span of
belt. Check belts frequently.
1.
The cutting unit drive belts should have a
maximum deflection of 1/2 inch with a 10 pound load
applied.
2.
Loosen jam nut on front end of belt tension rod.
Rotate rod to lengthen or shorten rod to desired length.
Tighten jam nut.
Figure 79
1. Belt tension rod
1
BATTERY CARE
1.
Battery electrolyte level must be properly
maintained and the top of the battery kept clean. If the
Grounds Pro 2000-D is stored in a location where
temperatures are extremely high, the battery will run
down more rapidly than if the machine is stored in a
location where temperatures are cool.
CAUTION
Since the gasses from the battery are
explosive, keep open flame and electrical
spark away from the area; do not smoke.
2.
Check the electrolyte level every 25 operating
hours or, if machine is in storage, every 30 days.
3
. Maintain cell level with distilled or demineralized
water. Do not fill cells above the bottom of the split ring
inside each cell.
4.
Keep top of battery clean by washing periodically
with a brush dipped in ammonia or bicarbonate of soda
solution. Flush the top surface with water after
cleaning. Do not remove the fill caps while cleaning.
5
. Battery cables must be tight on terminals to
provide good electrical contact.
6.
If corrosion occurs at terminals, disconnect
cables, negative (-) cable first and scrape clamps and
terminals separately. Reconnect cables, positive (+)
cable first and coat terminals with petroleum jelly.
WIRE HARNESS SERVICE
Prevent corrosion of wiring terminals by applying Grafo
112X (SkinĆover) grease, Toro Part No. 505Ć47, to the
inside of all harness connectors whenever the harness
is replaced.
Whenever working with the electrical system, always
disconnect battery cables, negative (-) cable first, to
prevent possible wiring damage from shortĆouts.
Before welding on the machine, disconnect ground
cable from the battery to prevent damage to the
electrical system.
Summary of Contents for 02003-90001
Page 6: ... ...
Page 11: ... 2 0 1 ...
Page 21: ... ...
Page 23: ... 1 1 2 0 0 0 0 0 0 0 1 0 0 0 0 ...
Page 27: ... ...
Page 28: ... 2 0 2 2 0 1 2 2 2 2 2 0 2 2 0 1 0 0 1 2 0 0 2 2 ...
Page 29: ... ...
Page 37: ... ...
Page 38: ... ...
Page 40: ... _ _ ...
Page 41: ... ...
Page 42: ... ...
Page 43: ... ...