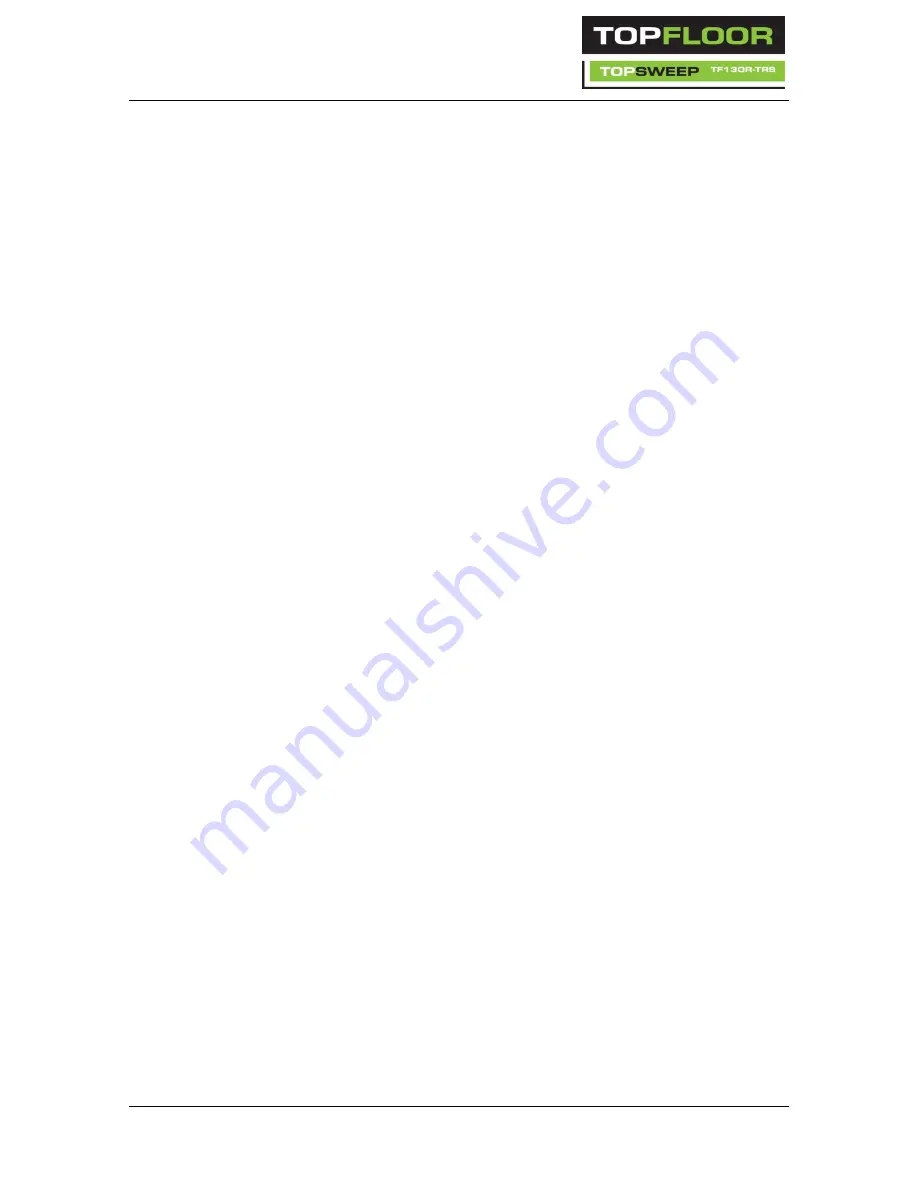
TF130R-TRS
19
5.8
Maintenance Table
5.8.1
Maintenance daily
Check the battery acid level and if required, replenish distilled water.
Charge the battery.
Check the machine for visible damage and malfunctions.
Empty the dust container.
Check the broom tunnel and roller tunnel for adhered parts, or dirt parti-
cles that have got stuck, which would narrow the broom tunnel and
constrict the free movement of the roller brushes.
Check the state of the dust filter, clean if required.
5.8.2
In addition, every 50 operating hours
Clean the battery poles and grease them.
Check the main brooms for wear and foreign bodies replace them if
required
Check the sweeping mirror and adjust it if required
Check the side broom setting for wear, if required, set it or replace it.
5.8.3
In addition, every 100 operating hours
Check the cable connections for firmness
Check the cable insulation, replace cables if required.
Check all the chains for wear or impermissible tension, replace if re-
quired.
Check all the bearings for wear.
Check all the seals for damage or correct seating.
Check the cable connections for firmness, replace faulty cables
Check the dust filter, replace if required.
Check the collected dust for foreign bodies and clean it.
In addition
Check the brake pads of the drum brake
Summary of Contents for TF130R-TRS
Page 1: ...Operator manual TF130R TRS vacuum sweeper...
Page 2: ......
Page 26: ...24 TF130R TRS...
Page 27: ...TF130R TRS 25...