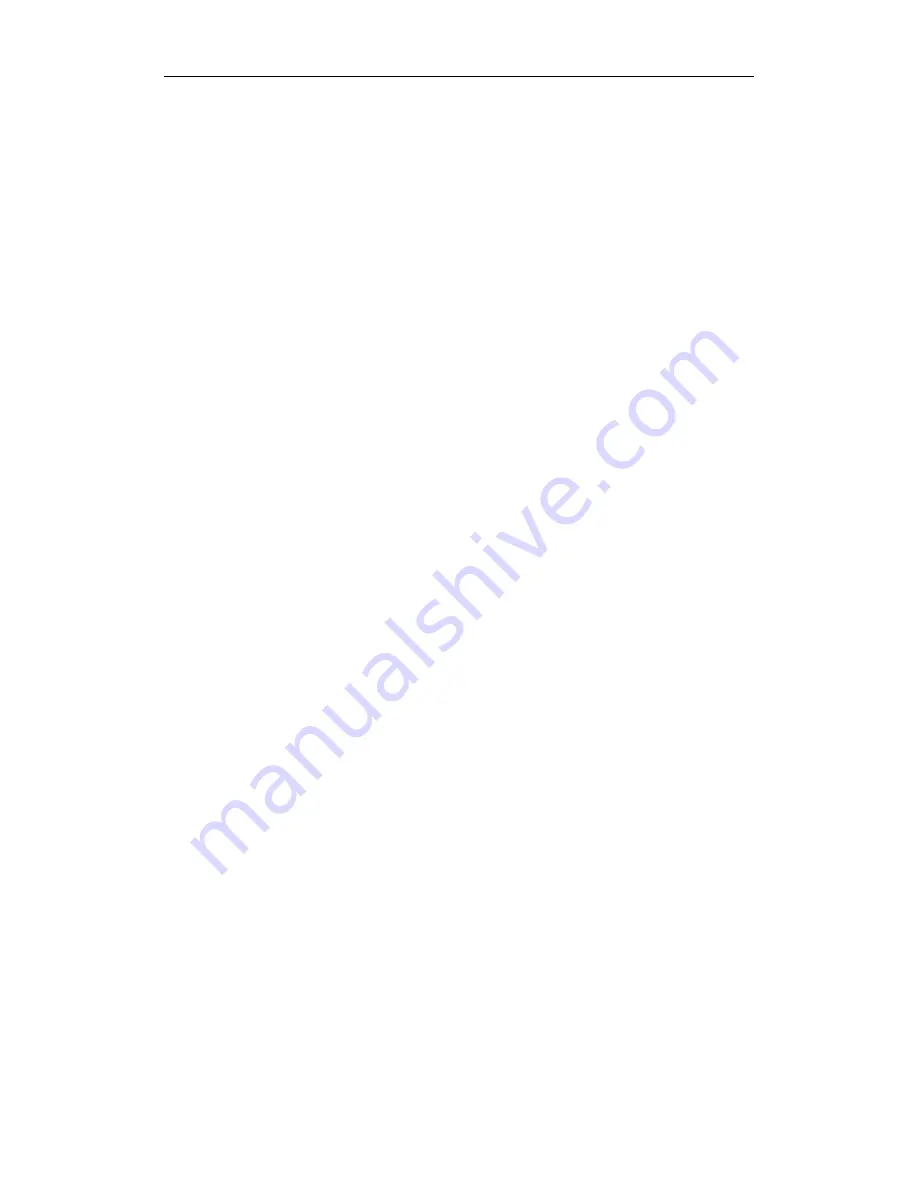
CONTENT
- II -
CONTENT
§
1 Safety .......................................................................................... 1
§1.1 Signal Explanation ....................................................................................................... 1
§1.2 Arc Welding Damage ................................................................................................... 1
§1.3 The knowledge of Electric and Magnetic Fields ....................................................... 5
§2 Overview ....................................................................................... 7
§2.1 Brief Introduction ........................................................................................................ 7
§2.2 Working Principle ........................................................................................................ 8
§2.3 Volt-Ampere Characteristic ........................................................................................ 8
§3 Installation and Adjustment ..................................................... 10
§3.1 Parameters ................................................................................................................. 10
§3.2 Duty cycle and Over-heat .......................................................................................... 10
§3.3 Equipment Connection ............................................................................................... 11
§3.4 Maintenance of MIG Gun mechanism ..................................................................... 12
§3.5 Maintenance of the wire feed mechanism ................................................................ 14
§4 Operation .................................................................................... 16
§4.1 Layout for the front and rear panel ......................................................................... 16
§4.2 Welding operation ...................................................................................................... 18
§4.2.1
Voltage Setting
................................................................................................................... 18
§4.2.2
Wire speed setting
.......................................................................................................... 18
§4.3 Welding parameters................................................................................................... 18
§4.4 Operation environment ............................................................................................. 19
§4.5 Operation Notices ...................................................................................................... 19
§5 Maintenance & Troubleshooting ............................................. 20
§5.1 Maintenance ............................................................................................................... 20
§5.2 Troubleshooting ......................................................................................................... 21
§5.3 Electrical schematic drawing .................................................................................... 23