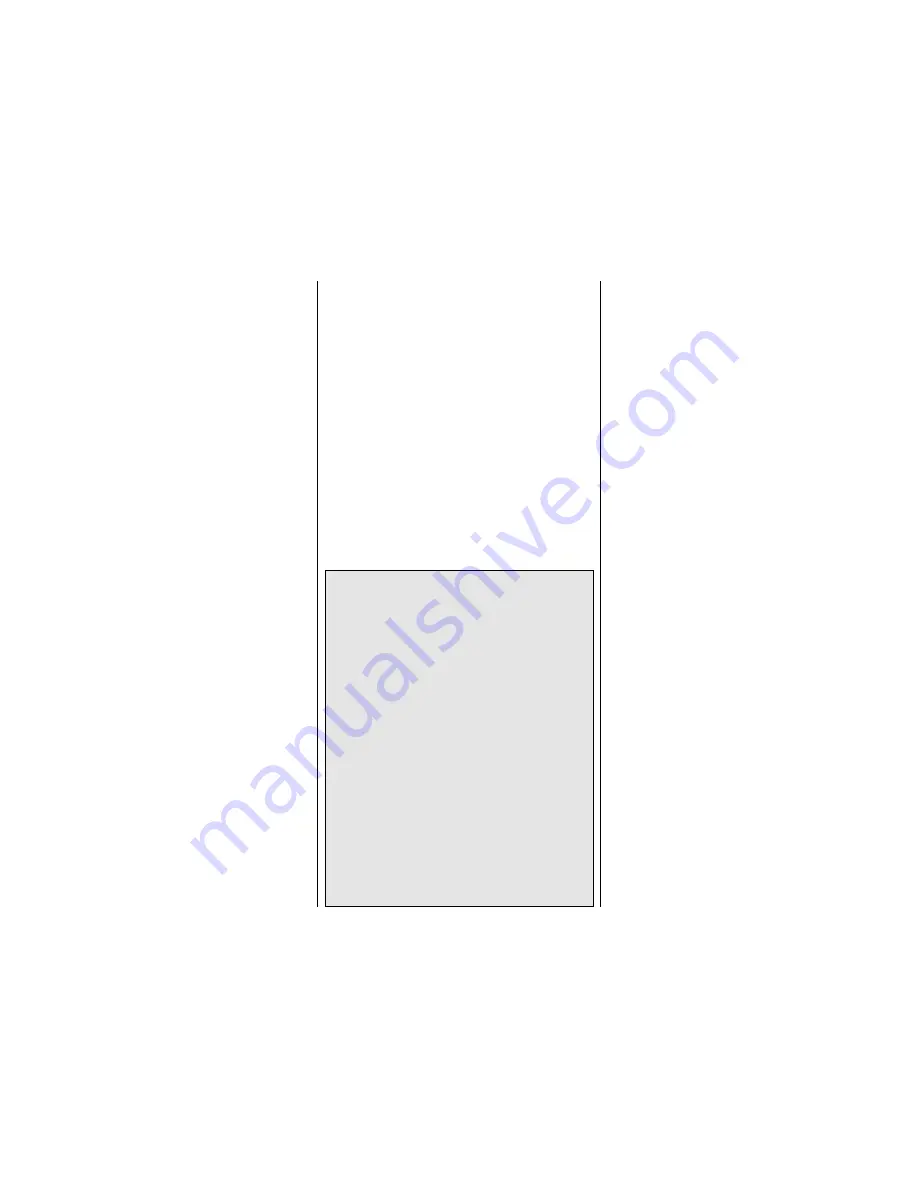
35
aircraft presents a greater danger than an overpowered
aircraft. However, the selection of engine size relative
to airframe strength and power loading mandates good
discretionary judgment by the designer and builder.
Current AMA maximums for engine displacement are
6.0 cu. in. for two-stroke and 9.6 cu. in. for four-stroke
engine. These maximums apply only to AMA Sanctions
concerning competition events (such as 511, 512, 515
and 520) and, as such, the maximums apply. All IMAA
(non competition) events should be sanctioned as Class
“C” events, in which these engine size maximums do
not apply.
Generally, it is recommended that no attempt should be
made to fl y a radio controlled model aircraft with a gasoline
engine in which the model aircraft weight would exceed
twelve (12) pounds (underpowered) per cubic inch of
engine displacement, or be less than fi ve (5) pounds
(overpowered) per cubic inch of engine displacement.
Example: Using a 3 cu. in. engine, a model would likely
be underpowered at an aircraft weight greater than 36
pounds. With the same engine, an aircraft weighing less
than 15 pounds would likely be overpowered.
Servo arms and wheels should be rated heavy duty.
Glass-fi lled servo arms and control horns are highly
recommended.
Control surfaces linkages are listed in order of
preference:
1. Cable system (pull-pull). A tiller bar is highly
recommended along with necessary bracing.
2. Arrow Shaft, fi berglass or aluminum, 1/4" or 5/16" [6
or 8mm] O.D. bracing every six (6) to ten (10) inches is
highly recommended.
3. Tube-in-tube (nyrod). Bracing every few inches is
highly recommended. Inner tube should be totally
enclosed in outer tube.
4. Hardwood dowel, 3/8" O.D. bracing every six (6) to ten
(10) inches is highly recommended.
Hinges should be rated heavy duty and manufactured
for Giant Scale use primarily. Homemade and original
design hinges are acceptable if determined to be
adequate for the intended use.
Clevis (steel, excluding heavy duty ball links) and
attachment hardware should be heavy duty 4-40
threaded rod type. 2-56 threaded size rod is acceptable
for some applications (e.g. throttle). Clevis is to have
lock nuts and sleeve or spring keepers.
Propeller tips should be painted or colored in a visible
and contrasting manner so as to increase the visibility of
the propeller tip arc.
FLYING
The Giant P-47D ARF is a great-fl ying model that fl ies
smoothly and predictably. The Giant P-47D ARF does
not, however, possess the self-recovery characteristics
of a primary R/C trainer and should be fl own only by
experienced R/C pilots.
FUEL MIXTURE ADJUSTMENTS
A fully cowled engine may run at a higher temperature
than an un-cowled engine. For this reason, the fuel
mixture should be richened so the engine runs at about
200 rpm below peak speed. By running the engine
slightly rich, you will help prevent dead-stick landings
caused by overheating.
CAUTION (THIS APPLIES TO ALL R/C AIRPLANES):
If, while fl ying, you notice an alarming or unusual
sound such as a low-pitched “buzz,” this may indicate
control surface fl utter. Flutter occurs when a control
surface (such as an aileron or elevator) or a fl ying
surface (such as a wing or stab) rapidly vibrates up
and down (thus causing the noise). In extreme cases,
if not detected immediately, fl utter can actually cause
the control surface to detach or the fl ying surface to fail,
thus causing loss of control followed by an impending
crash. The best thing to do when fl utter is detected is to
slow the model immediately by reducing power, then
land as soon as safely possible. Identify which surface
fl uttered (so the problem may be resolved) by checking
all the servo grommets for deterioration or signs of
vibration. Make certain all pushrod linkages are secure
and free of play. If it fl uttered once, under similar
circumstances it will probably fl utter again unless the
problem is fi xed. Some things which can cause fl utter
are; Excessive hinge gap; Not mounting control horns
solidly; Poor fi t of clevis pin in horn; Side-play of wire
pushrods caused by large bends; Excessive free play
in servo gears; Insecure servo mounting; and one of
the most prevalent causes of fl utter; Flying an over-
powered model at excessive speeds.
TAKEOFF
If you are using the optional air retracts, remember to
pump them up before each fl ight. Before you get ready
to takeoff, see how the model handles on the ground by
doing a few practice runs at low speeds on the runway.
Hold “up” elevator to keep the tail wheel on the ground.
If necessary, adjust the tail wheel so the model will roll
straight down the runway. If you need to calm your nerves
before the maiden fl ight, shut the engine down and bring
the model back into the pits. Top off the fuel, then check
all fasteners and control linkages for peace of mind.
Remember to takeoff into the wind. When you’re ready,
point the model straight down the runway, hold a bit of
up elevator to keep the tail on the ground to maintain tail
wheel steering, then gradually advance the throttle. As
the model gains speed decrease up elevator allowing the
tail to come off the ground. One of the most important
things to remember with a tail dragger is to always be
ready to apply right rudder to counteract engine torque.
Gain as much speed as your runway and fl ying site will
practically allow before gently applying up elevator, lifting
the model into the air. At this moment it is likely that
you will need to apply more right rudder to counteract
engine torque. Be smooth on the elevator stick, allowing
the model to establish a gentle climb to a safe altitude
before turning into the traffi c pattern.
FLIGHT
For reassurance and to keep an eye on other traffi c, it
is a good idea to have an assistant on the fl ight line
with you. Tell him to remind you to throttle back once the
plane gets to a comfortable altitude. While full throttle
is usually desirable for takeoff, most models fl y more
smoothly at reduced speeds.
Take it easy with the Giant P-47D ARF for the fi rst few
fl ights, gradually getting acquainted with it as you gain
confi dence. Adjust the trims to maintain straight and
level fl ight. After fl ying around for a while, and while still
at a safe altitude with plenty of fuel, practice slow fl ight
and execute practice landing approaches by reducing
the throttle and lowering the fl aps to see how the model
handles at slower speeds. Add power to see how she
climbs as well. Continue to fl y around, executing various
maneuvers and making mental notes (or having your
assistant write them down) of what trim or C.G. changes
may be required to fi ne tune the model so it fl ies the way