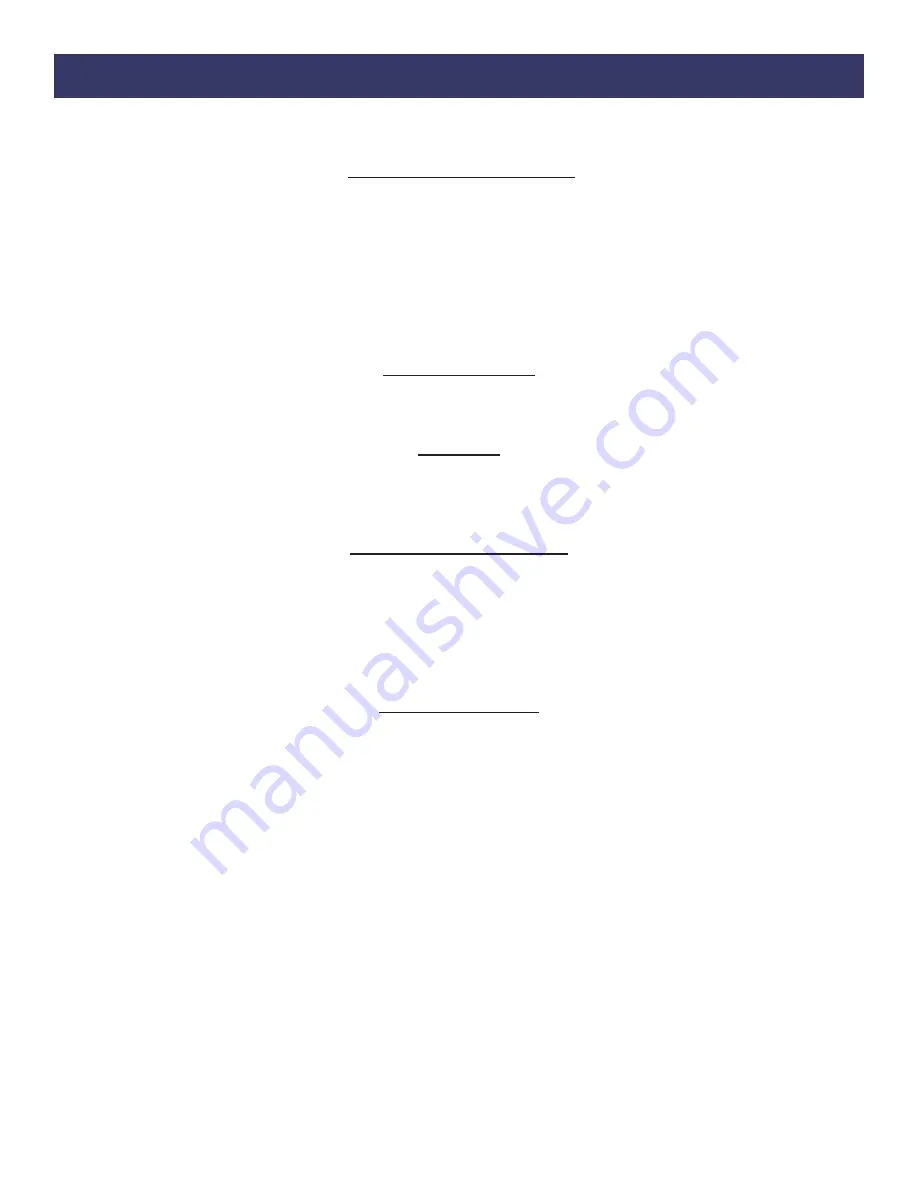
Installation and Maintenance Tips
Following the guidelines will help you to ensure the pneumatic tools your company uses are operating and are
maintained in the very best of condition.
Initial Inspection of a New Tool
When a new tool is delivered to your facility, it is important to inspect the tool for any signs of damage that may
have occurred during shipping. Here is a list of things to inspect:
● With the tool disconnected from the air supply, depress the throttle lever or trigger. The device should move
freely and not become caught.
● Inspect the guard of the tool, if so equipped. The guard should be free of any chips, nicks or dents.
● Inspect the output of the tool. The threads should show no signs of bends or chips. Grasp the spindle by
hand and spin. The spindle should turn freely with no resistance.
Plumbing Installation
The tool must have fittings and connectors installed into the air inlet in order to connect with your companies
air system. Your choice of fittings can greatly affect the performance of the tool.
Fitting Size
The size of the air inlet of the tool is the minimum size of fitting that will allow for proper airflow into the tool.
Should a smaller fitting size be used such as reducers or adapters, this will constrict the airflow into the tool
and reduce the overall performance.
Coupling Size and Installation
The coupling size should be equal to or larger than the inlet size of the tool. If a smaller size coupling is used
then the air supply volume may be reduced which may lead to reduced performance from the tool.
The coupling should be installed near to the tool. It is important that the tool receive internal lubrication on a
regular basis. Having the connection closer to the tool will promote regular lubrication, as the connection is
easily accessible. Hose whips are often used between the tool and the coupling.
Use thread sealant on all pipe threads and ensure a tight fit.
Operating Speed Test
After your initial inspection and installation of the plumbing connections, it is important to test for the operating
speed of the tool. This test should be performed before you install any abrasive or tooling. Each tool is
stamped with a maximum operating speed. This speed determines the highest rotational speed in R.P.M.’s
that the tool will turn when it is functioning properly. This speed was set from the factory and is closely related
to the operating speed of the abrasive used with the tool. This relationship will be discussed in the “mounting
abrasives and blades” section.
Find the maximum operating speed stamped onto the tool. Connect the tool to an air supply that provides
90 psi and secure the tool in a vise. A lower or higher air pressure will result in a false speed test and may
create a hazardous situation. Depress the throttle lever or trigger and run the tool. Use a properly calibrated
tachometer to determine the actual operating speed of the tool. The actual operating speed on the tachometer
should be 90-95% of the maximum free speed stamped on the tool. If this is not the case then contact the
distributor or tool manufacturer immediately. The tool must not be put into service if the actual speed is over
95% of the stamped maximum speed.
Example: Tool rated at 6000 R.P.M.
90% of 6000 (.90 x 6000) = 5400
95% of 6000 (.95 x 6000) = 5700
The tool should run between 5400 R.P.M. and 5700 R.P.M. when tested with a tachometer. Tachometers must
be checked and calibrated on a regular basis according to the manufacturers recommendations