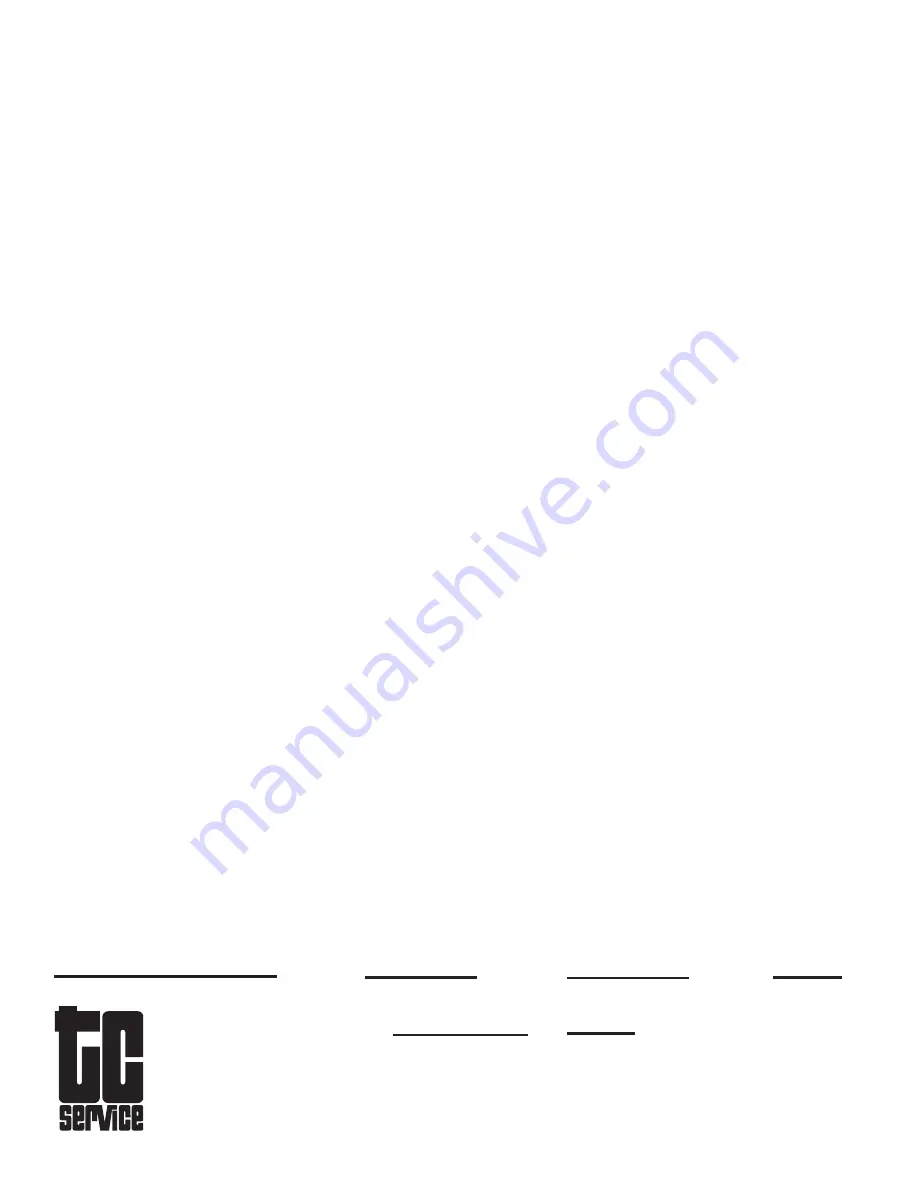
the air system and become lodged onto the blades. This can cause the blades to delaminate where pieces of
blade material will flake off. Any blade exhibiting this characteristic should be replaced. The blades will see the
most wear on the longest edge along their height. This is the surface that makes contact with the cylinder wall
and creates an air seal. The overall width of the blade will reduce as this surface wears. When any one-end
width of the blade wears to the minimum width, (.347 inches) then one should consider replacement.
The Bearings (700-7 and 700-9). There is no means of measurement that can determine the condition of a
bearing. The only test that can be performed it to manually turn either the outer of inner race with respect
to each other. The movement should feel free with no resistance. If resistance is felt either continuous or
repetitive, then the bearing should be replaced
The Front Endplate (700-10). The front endplate is essentially a flat steel disc in the front of the motor
assembly. The rotor makes occasional contact with the front endplate. Over time, this contact will wear away
the surface of the endplate and result in a circular depression in the middle of the part. When this depression
becomes 0.003 inches deep from the original surface, then the efficiency of the motor is reduced to the point
where one should replace the endplate. * Note – The front endplates are designed so either front or back
surface can be used toward the motor. When one side is judged as unusable, the part can be flipped during
reassembly and new wear surface is available.
The Rotor (700-12). We employ a floating rotor design in the many of our motors. This design allows the rotor
to float along the spindle in the motor cavity. Occasionally the rotor will make contact with the endplates. Some
wear can be seen on both the top and bottom surfaces of the overall length. Should the overall length wear to
the minimum length of 1.993 inches then the rotor should be replaced.
The Cylinder (700-11). The only wear seen on the cylinder is going to occur on the inner surface. This surface
is always in contact with the blades. Over time, the blades will remove material from this surface that will
reduce the overall performance of the tool. Consecutive high and low spots will become evident on the internal
surface. They will appear as ridges along the axis of the cylinder. When these ridges vary 0.016 inches from
high to low, the cylinder should be replaced.
The Rear Endplate (700-16). The rear endplate is the located toward the rear of the motor assembly. The most
wear this part is exposed to is from occasional contact with the rotor. Over time, this contact will wear away
the surface of the endplate and result in a circular depression in the middle of the part. When this depression
becomes 0.003 inches deep from the original surface, then the efficiency of the motor is reduced to the point
where one should replace the endplate.
This covers all of the predictable wear that can occur within the tool. Other factors due to environment, level of
treatment/care and air supply quality can cause other forms of wear that are unpredictable.
For More Information
1) General Industry Safety & Health Regulations 29 CFR, Part 1910 and where applicable Construction
Industry Safety & Health Regulations 29 CFR, Part 1926 available from Superintendent of Documents, Gov’t.
Printing Office, Washington, D.C. 20402.
2) Safety Code For Portable Air Tools, ANSI B186.1, B7.1 and Z87.1, available from American National
Standards Institute, Inc. 1430 Broadway, New York, NY 10018
© Copyright 2005
All Rights Reserved
T.C. Service Co.
38285 Pelton Rd.
Willoughby, OH 44094
U.S.A.
Ph: 440-954-7500
Fax: 440-954-7118
Saws
Air Motors
Drills
Grinders
Percussion Tools
Polishers