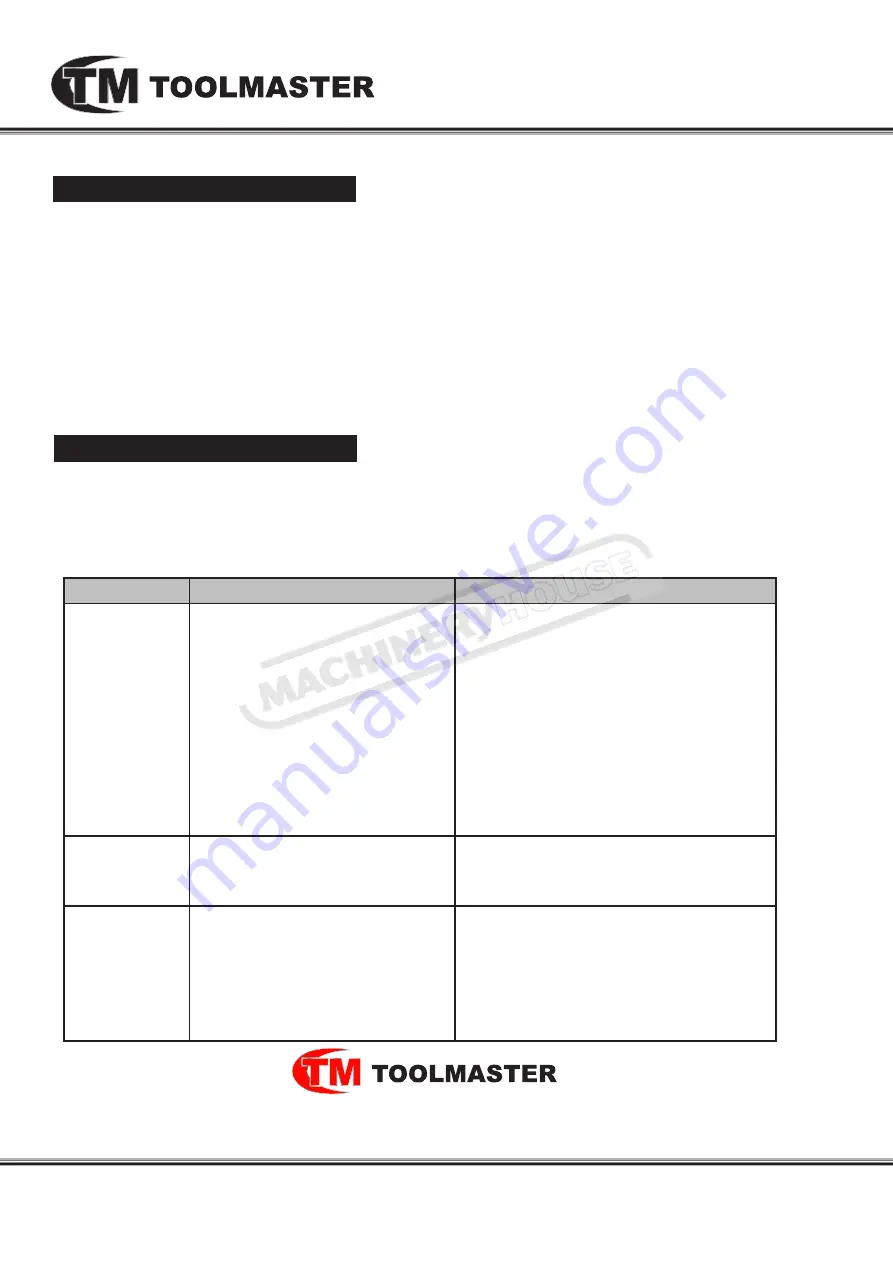
6
www.machineryhouse.com.au
www.machineryhouse.co.nz
1.
Daily - Air Supply Maintenance:
Every day, maintain the air supply according to the component manufacturers’ instructions.
Maintain the lubricator’s oil level. Use Pneumatic Tool Oil (Order Code A037)
Drain the moisture filter regularly.
Performing routine air supply maintenance will allow the tool to operate more safely and will also
reduce wear on the tool.
2.
Quarterly (every 3 months)
– Tool Disassembly, Cleaning, and Inspection:
Have the internal mechanism cleaned, inspected, and lubricated by a qualified technician.
3. For a full service contact your local Toolmaster service agent.
4. When not in use, disconnect from air supply, clean nibbler and store in a safe and dry place.
Maintenance
Symptoms
Possible Cause
Possible Solution
Decreased output.
1. Not enough air pressure and/or air flow.
2. Obstructed throttle.
3. Incorrect lubrication or not enough
lubrication.
4. Blocked air inlet screen (if equipped).
5. Air leaking from loose housing.
6. Mechanism contaminated.
7. Vane wear or damage.
1. Check for loose connections and make sure
that air supply is providing enough air flow
(CFM) at required pressure (PSI) to the tool’s air
inlet. Do not exceed maximum air pressure.
2. Clean around throttle to ensure free movement.
3. Lubricate using air tool oil and grease according
to directions.
4. Clean air inlet screen of buildup.
5. Make sure housing is properly assembled and
tight.
6. Have qualified technician clean and lubricate
mechanism. Install in-line filter in air supply as
stated in Setup: Air Supply.
7. Replace all vanes.
Housing heats
during use
1. Incorrect lubrication or not enough
lubrication.
2. Worn parts.
1. Lubricate using air tool oil and grease according
to directions.
2. Have qualified technician inspect internal
mechanism and replace parts as needed.
Severe air leakage
(Slight air leakage
is normal,
especially on older
tools.
1. Cross-threaded housing components.
2. Loose housing.
3. Damaged valve or housing.
4. Dirty, worn or damaged valve.
1. Check for incorrect alignment and uneven gaps.
If cross-threaded, disassemble and replace
damaged parts before use
2. Tighten housing assembly. If housing cannot
tighten properly, internal parts may be
misaligned
3. Replace damaged components.
4. Clean or replace valve assembly.
Review the troubleshooting and procedures in this section if a problem develops with your Air Tool.
If you are still unable to resolve the problem, then contact your local Toolmaster service centre. If
additional help with a procedure is required, then contact you distributor.
Note:
Make sure you have the model of the machine, serial number,and manufacture date
before calling.
Troubleshooting
INDUSTRIAL AIR TOOLS