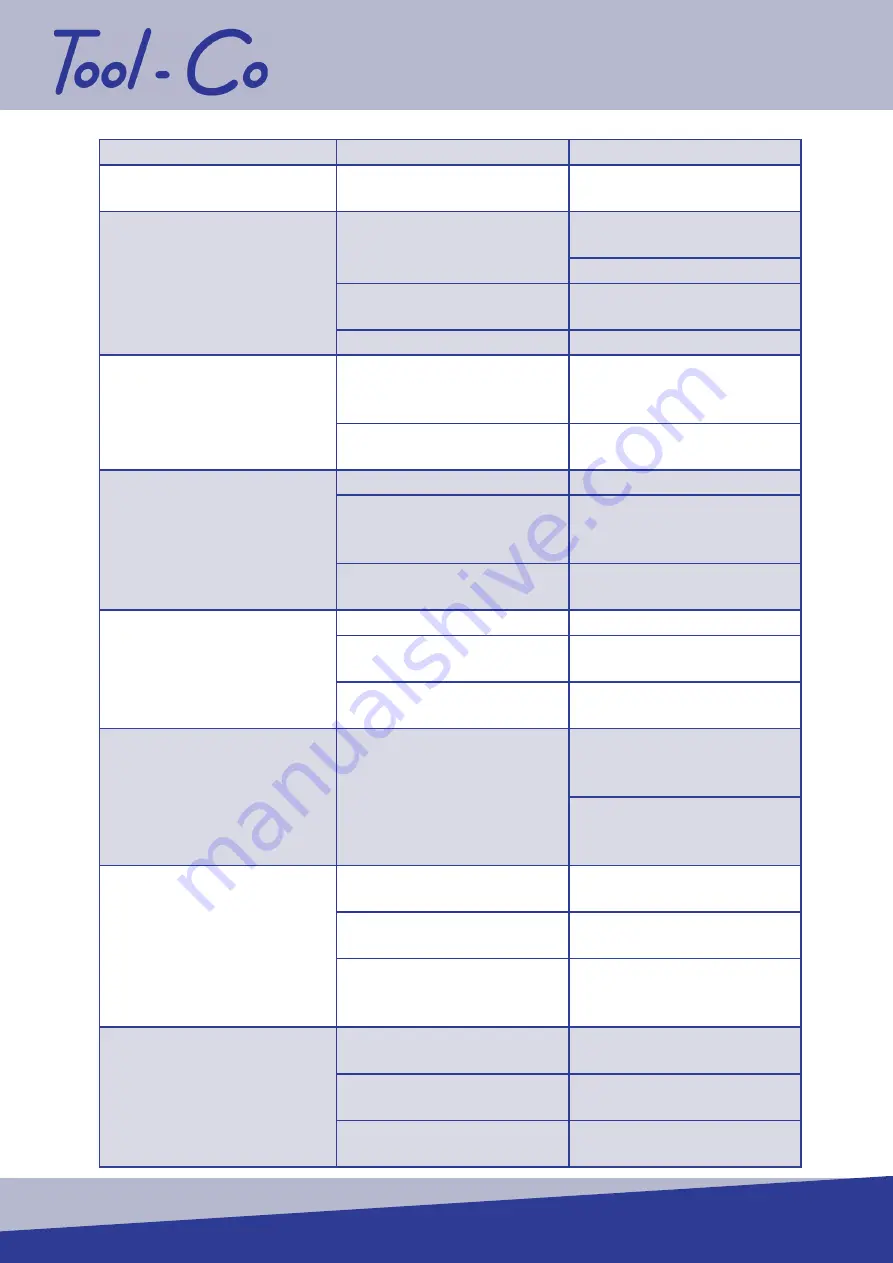
BCA350
Symptom
Possible Cause
Action
Irregular run of the saw
blade
Poor tension in the blade
material
Return the saw blade to the
manufacturer
Saw blade wobbles when
the saw is running
Saw blade is damaged or
bent
Have the saw blade
aligned or fl attened
Clean the receiving fl ange
Flange of the saw blade is
damaged
Replace the saw blade
fl ange
Shaft of the motor is bent
Replace the electric motor
Diamond segment becomes
loose
Overheating of the saw
blade
Have the diamond segment
soldered on the blade
again
Coolant is not suffi cient
Ensure optimum fl ow of
cooling water
Excessive wear
Wrong type of saw blade
Use a harder blade bond
Shaft of motor causes
wobbling
Have bearings of the motor
replaced, or replace the
motor
Overheating
Ensure optimum fl ow of
cooling water
Cracks in or near the
diamond segment
Saw blade bond too hard
Use a softer blade bond
Fixed fl ange is worn out
Have the fi xed fl ange
replaced
Motor shaft bearing is worn Replace the bearing of the
motor shaft
The center hole in the saw
blade has become wider
due to wear
The saw blade has slipped
on the motor shaft when
running
The arbor of the saw blade
must be fi tted with an
adapter ring
Check the receiving fl ange
and have it replaced if
necessary
Appearance of cut is not
optimal
Poor tension in the blade
material
Return the blade to the
manufacturer
Too much load placed on
the saw blade
Use a suitable blade
Diamond segments are
blunt
Sharpen the diamond
blade on an abrasive
material
Grinding marks on the saw
blade
Material is not being fed
parallel to the saw blade
Ensure that the direction of
feed is parallel to the blade
Poor tension in the blade
material
Adjust the roller table or
have it adjusted
Too much load on the
blade
Exert less pressure when
cutting, proceed slower
Pg.7
Summary of Contents for BCA350
Page 1: ...OPERATING MANUAL BCA350 MASONRY SAW...
Page 2: ......
Page 12: ...BCA350 Pg 9 Pg 10 EXPLODED DIAGRAM A...
Page 16: ...BCA350 EXPLODED DIAGRAM B Pg 13...
Page 20: ...BCA350 Pg 17...