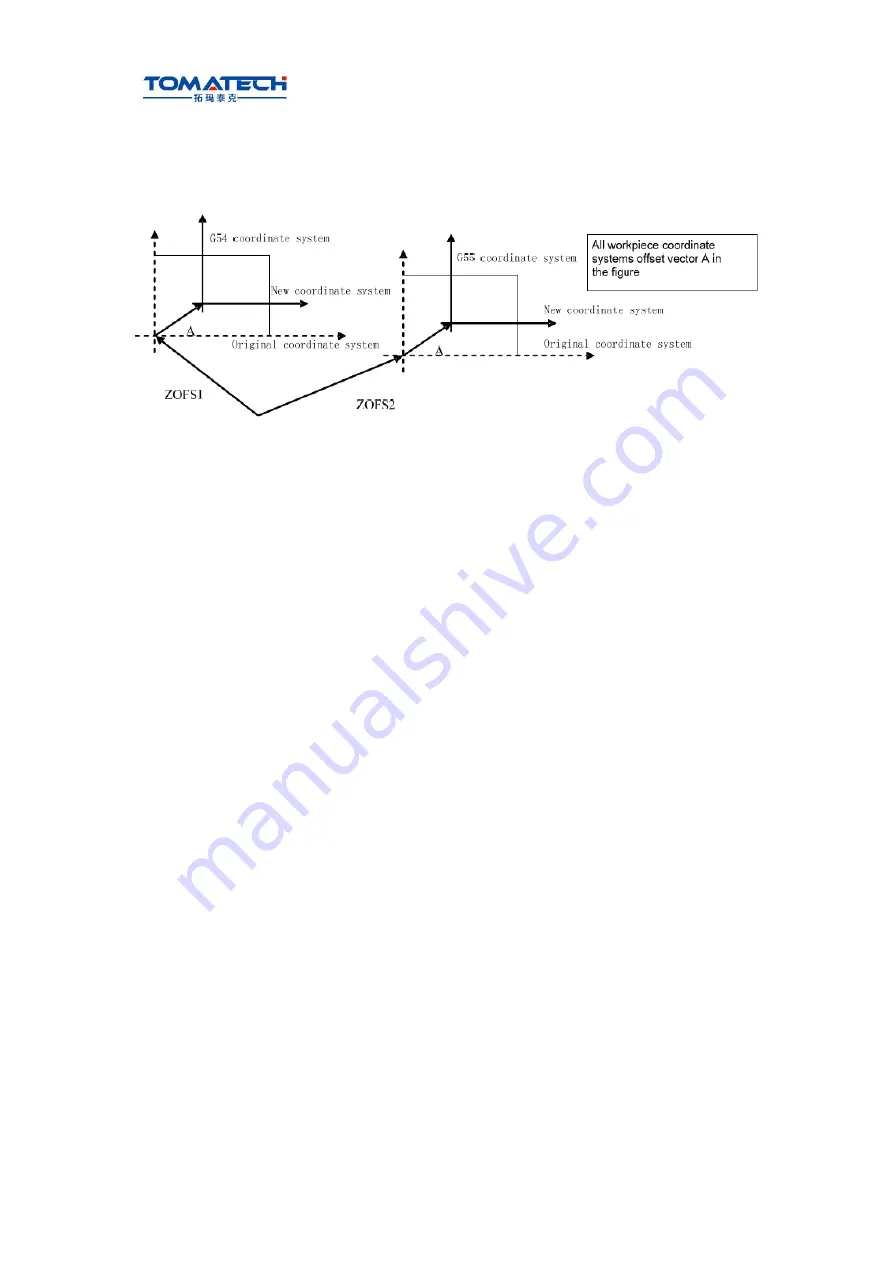
TOMATECH AUTOMATION
systems, which are shown below:
Ⅰ
Prog
ramming
3.19 Fixed Cycle Command
To simplify programming, the system defines G command of single machining cycle with
one
block to complete the rapid traverse to position, linear/thread cutting and rapid traverse to
return to
the starting point:
G90: axial cutting cycle;
G92: thread cutting cycle;
G94: radial cutting cycle;
G92 will be introduced in section Thread Function.
3.19.1 Axial cutting cycle G90
Command format:
G90 X(U) __ Z(W) __ F__; (cylinder cutting)
G90 X(U) __ Z(W) __ R__ F__; (taper cutting)
Command function:
From starting point, the cutting cycle of cylindrical surface or taper
surface is completed by radial feeding(X) and axial (Z or X and Z) cutting.
Command specifications:
G90 is modal;
Starting point of cutting: starting position of linear interpolation(cutting feed)
End point of cutting: end position of linear interpolation(cutting feed)
X: X absolute coordinates of cutting end point
U: different value of X absolute coordinate between end point and starting point of cutting
Z: different value of Z absolute coordinate between end point and starting point of cutting
W: different value of Z absolute coordinate between end point and starting point of cutting
R: different value (radius value) of X absolute coordinates between end point and start
point of
cutting. When the signs of R is not the same that of U, R│≤│U/2│; when R
=
0 or
the input is default, the cylinder cutting is executed as Fig.3-17, otherwise, the cone
cutting is executed as Fig. 3-18; unit: mm.
Ranges of X, U, Z, W
,
R are referred to Table 1-2 of Section 1.4.1, unit: mm/inch.
Cycle process:
Summary of Contents for TAC-100XT
Page 32: ...TOMATECH AUTOMATION...
Page 58: ...TOMATECH AUTOMATION After insert c Insert behind Before insert...
Page 92: ...TOMATECH AUTOMATION Fig 3 19 Example Fig 3 20 rod 125 110...
Page 95: ...TOMATECH AUTOMATION Fig 3 23 Programming Example Fig 3 24 rod 125 112...
Page 137: ...TOMATECH AUTOMATION Fig 3 48 a Cut in method as follows Fig 3 48 b Programming Fig 3 48 b...
Page 145: ...TOMATECH AUTOMATION 1 Operation commands 1 Assignment of macro variables I J G65 H01 P I Q J...
Page 154: ...TOMATECH AUTOMATION Fig 4 7 Imaginary tool nose number in rear tool post coordinate system...
Page 155: ...TOMATECH AUTOMATION Fig 4 8 Imaginary tool nose number in front tool post coordinate system...
Page 158: ...TOMATECH AUTOMATION Fig 4 11 Compensation direction of rear coordinate system...
Page 165: ...TOMATECH AUTOMATION d Special cutting 1 Without intersection...
Page 176: ...TOMATECH AUTOMATION...