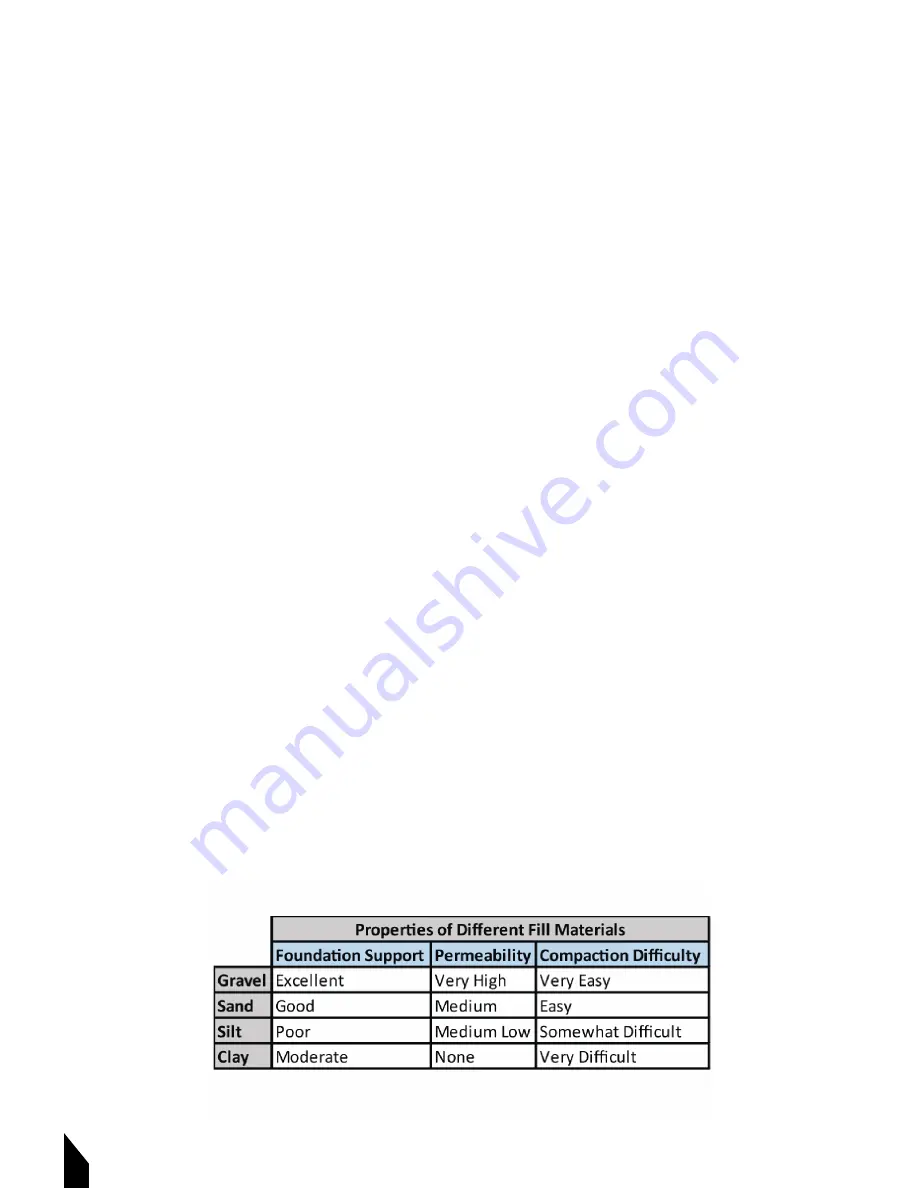
17
18
5. Compaction Tips
5.1 Soil Drop Test:
Soil preparedness refers to the “wetness” of the dirt or soil. Soil needs
to be 50% dry and 50% wet, before starting compaction. A simple “hand test” can deter-
mine this. Pick up a handful of soil with your hand and squeeze the dirt. Observe whether
the soil is powdery or if it breaks apart when dropped. If the soil does break apart, it means
that it is too dry. If the soil keeps together in one piece when dropped, it is ready for com-
paction.
5.2 Soil Testing:
Testing: The function of this step is to measure the density of an aggregate
material to ensure the increase of density when driving out air. At a low moisture content
level, there are more soil particles assembling together. In order to determine if the soil is
compacted properly, there are several methods.
5.2.1 Soil Testing:
Test strips are useful to determine the method of compaction and
understand how many passes of your plate compactor are needed to achieve the optimum
compaction. Every layer of compacted soil meets a specific percentage on the proctor
curve. Through soil testing, it is possible to identify optimum moisture. Soil testing mea-
sures the soil density compared to the degree of compaction specifications, as well as the
e
ff
ect of the moisture.
A common laboratory method called the Proctor Compaction Test can be used to deter-
mine the optimal moisture content for a given soil type. The goal of this method is to
understand the soil’s maximum dry density. A second method of soil testing is known as
the California Test 216 and is used to find the relative compaction of untreated and treated
soils.
Four factors account for optimum compaction including li
ft
thickness, pressure, and soil
moisture content. During the compaction process, the soil's moisture adds density and
lubricates soil particles, until there is a maximum dry unit weight without voids in the soil.
The table below explains the di
ff
erent outcomes and properties of fill materials.
Summary of Contents for TPC80
Page 1: ...TPC80 TPC80H PLATE COMPACTOR Operation Manual ...
Page 23: ......
Page 24: ......
Page 25: ......
Page 28: ......