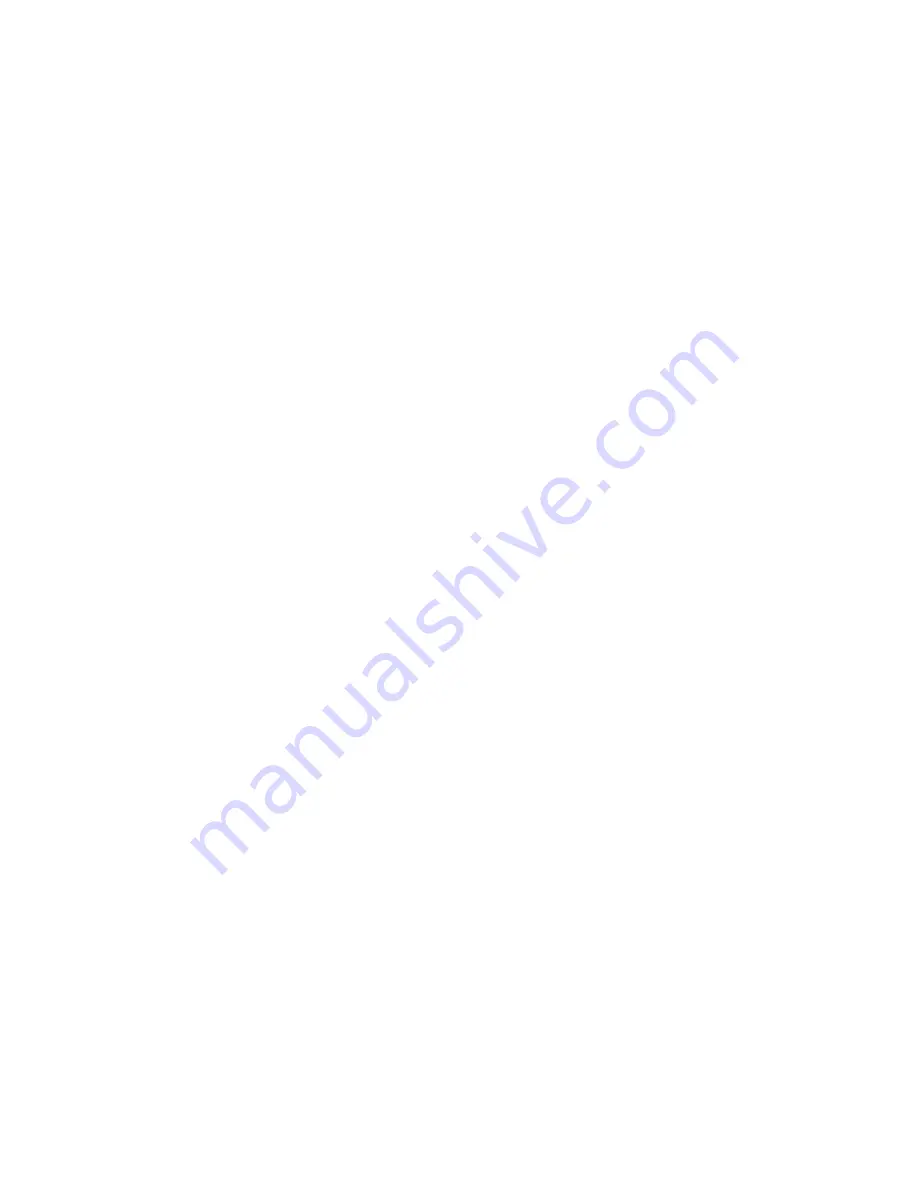
5
where the total thickness at the splice is about the same as unspliced film. (Fuji Single-8 and K-
Mart Focal film was on polyester base and must be tape spliced.) When making tape splices,
ensure that the sprocket holes are not covered up and the tape is on straight, on both sides of the
film.
NOTE: The multiple bends in the film path of the TVT-S8S puts greater demands on the
integrity of cement splices. If they are weak owing to using old cement, or not being fully
scraped, these are more likely to pop apart than in most silent equipment with a simpler path.
We suggest using 400 foot (122 meter) reels, and cans or 7" size white 1/4" audio tape
boxes. Usually if 8 small 50' rolls of super-8 film is wound on each reel, this will enable two of
the reels to fit on each 1 hour tape or disc with minimum waste and no need for time-consuming
tape editing or overlaps. Mark the leader on the head (beginning) of the reel with the customer’s
name or job number, and the reel number, to avoid mixups. Leader with a matte finish can be
written on with pencil, while shiny leader can be marked with a Sharpie or India ink. Ensure
that that the cleaning step does not remove the reel identification. Storage cans should be
ventilated for slight air circulation, to prevent film deterioration from “vinegar syndrome.”
Advise the customer to keep his film in a cool, dry, dark place to prevent fungus growth. You
want the film to be in good condition so you can transfer it again when the next super
generation of video equipment formats makes the present transfer obsolete. :-)
NOTE: Super-8 mechanisms are fussy about splices, compared to regular-8 ones. If
your cement splices of super-8 cause lost loops, change the direction of splicing by winding the
film right to left on the bench while splicing, instead of left to right, so you are scraping the
outgoing film instead of the incoming one. Having the splice accordingly lap the other way (so
the sharp leading edge of the thick splice rubs against the mechanism’s pressure plate instead of
hitting the bottom of the minimally undercut aperture plate opening) will give more reliable
running.
After each reel is spliced and repaired, it is rewound through the film cleaner device on
to the proper reel, which restores the reel to being heads (beginning) out instead of tails (foot or
end) out, and sent to the transfer room. Note: When using a liquid cleaner, view the rewinding
film by reflected light to make sure it is dry again before it is wound up, or else the film may
dry with “shoreline” marks on it. You can wind quite fast if not using an excessive amount of
solvent.
IMPORTANT NOTE: Film that is not lubricated will cause noisy unsteady running
and can lead to film damage. Even some newly processed films are returned unlubricated,
owing to laxity or environmental concerns by the processing lab. The cleaning fluid should
have a small amount of wax dissolved in it to provide lubrication for smooth transport through
the TVT-S8S or through the customer’s projector. A suggested amount is a lump of candle wax
or beeswax the size of a pea ground up and dissolved in a pint (half liter) of solvent. Cleaning
solvents that are widely used include methyl chloroform (toxic fumes), perchloroethylene (dry
cleaning fluid) (toxic fumes), Freon TF (ozone depleting), or 99% isopropanol (isopropyl
alcohol) (flammable). There are also commercially mixed film cleaners with lubricant. Cleaning
must take place in a ventilated area. Some users report that using Pledge Beeswax furniture
polish sprayed on a rag, with the film wound through it while still damp, does an excellent job
of lubrication.
Exposure Correction
The correction uses your choice of Peak or Center-Weighted Averaging sensing, for