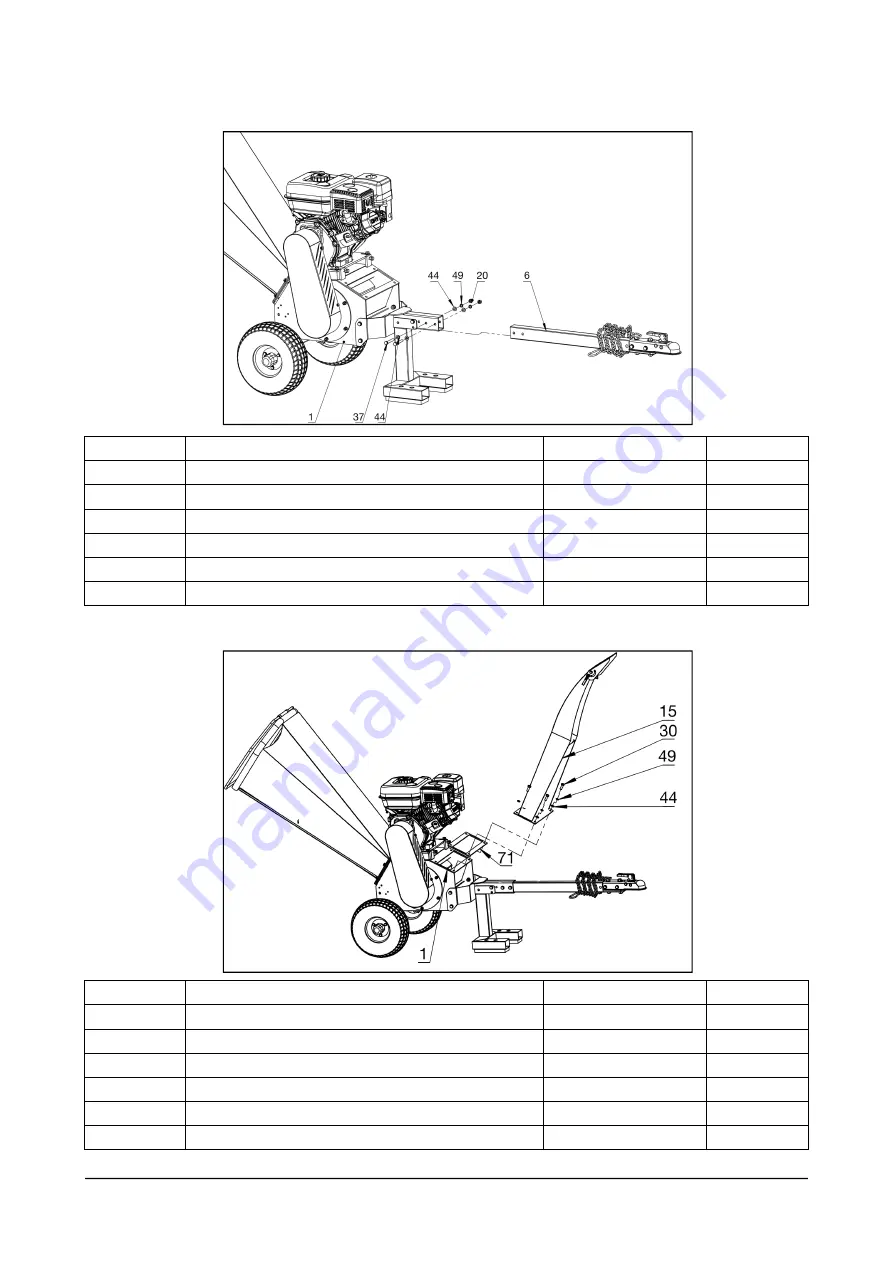
5. Installation tow bar
Parts no.
Description
Specifications
Quantity
1
Machine body assembly
1
6
Tow bar
1
20
Lock nut
M10
2
37
Bolt
M10x65
2
44
Washer
M10
4
49
Spring washer
M10
2
6. Installation discharge chute assembly
Parts no.
Description
Specifications
Quantity
1
Machine body assembly
1
15
Discharge chute assembly
1
30
Bolt
M10x30
4
44
Washer
M10
4
49
Spring washer
M10
2
71
Discharge to frame rubber
1
W W W . T M G I N D U S T R I A L . C O M
P 1 3 / 2 3
T o l l F r e e : 1 - 8 7 7 - 7 6 1 - 2 8 1 9