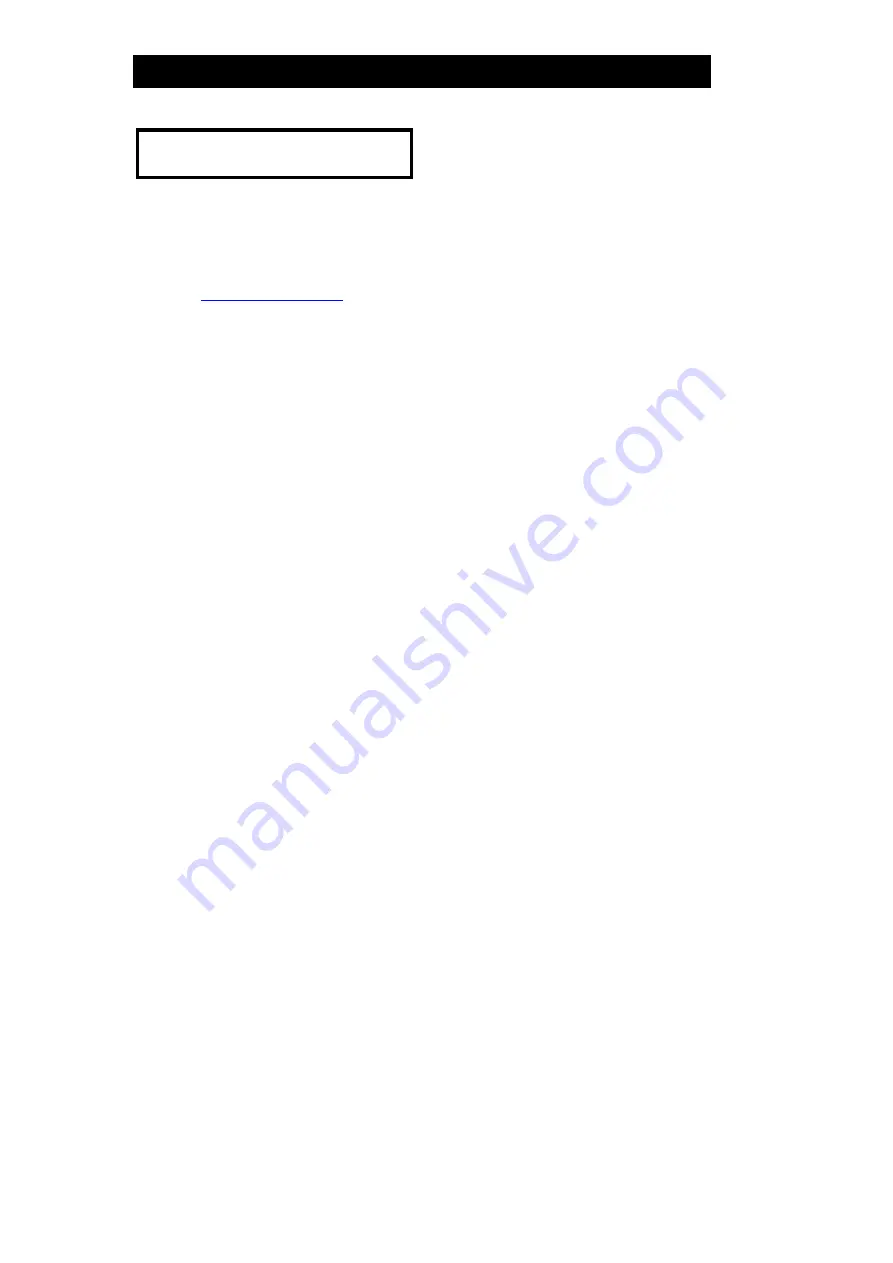
172-65605M-14 (SQ2/SQ4/SQ6) 10 Dec 2019
2
The copyright of this manual belongs to TLV CO., LTD. Unauthorized reproduction
of the contents of this manual in part or in whole is strictly prohibited.
This manual should be kept for future reference. If it becomes defaced or is
misplaced, contact your local TLV representative, or download from the TLV
website (
The contents of this manual are subject to change without notice.
Please note that visuals such as the diagrams and illustrations found within this
manual may differ slightly from the actual unit.
This manual was written for the purpose of use of the unit in the Japanese market.
Please carefully read all other documentation included for this unit and its
components.
Make sure that the person supervising operation of the unit has received a
thorough briefing on the contents of the 'Report on Commissioning Results' which
is issued after finishing the commissioning.
Important Notice