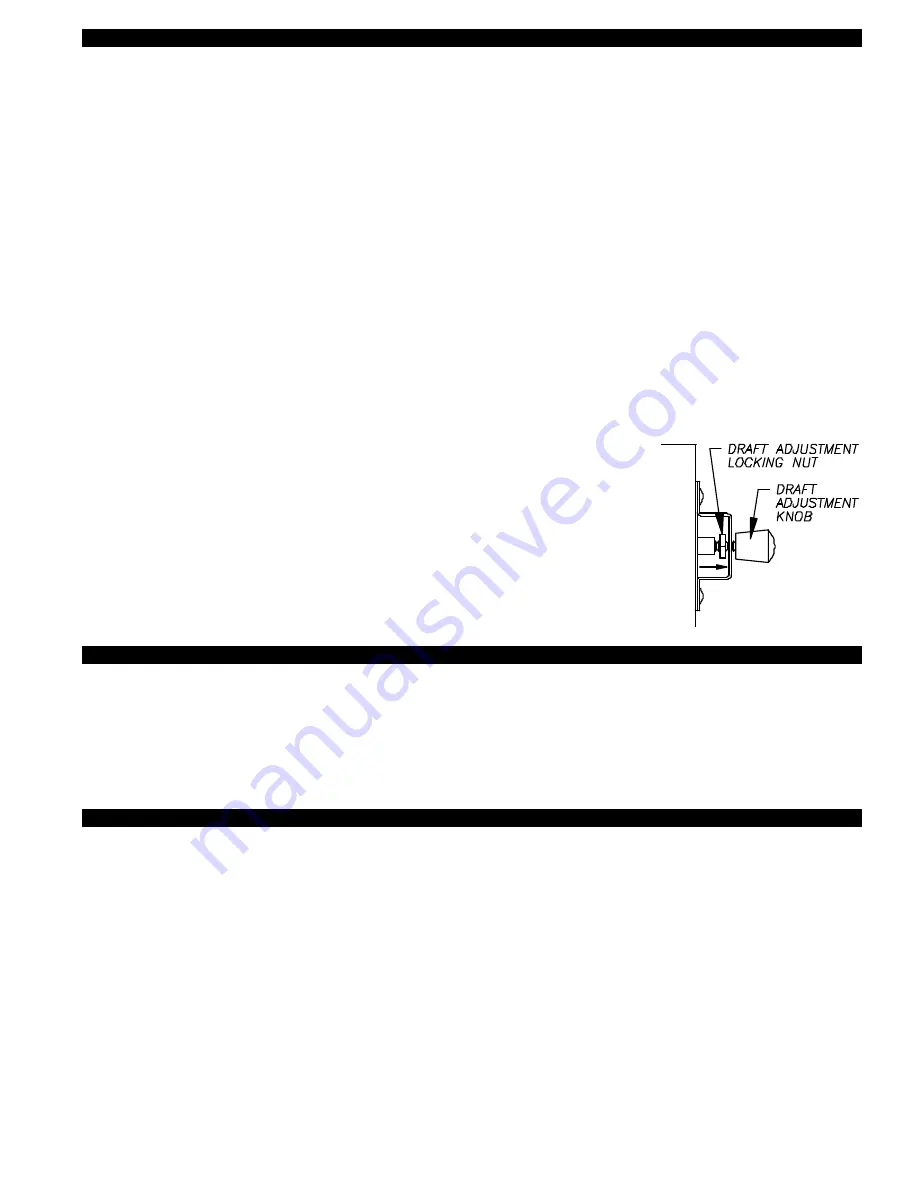
10
DRAFT ADJUSTMENT PROCEDURE
The SS2G Vent System will properly vent a wide range of BTU/hr. input capacities. To compensate for different burner capacities,
vent connector lengths, types and sizes, it features a draft adjustment located on the back of the venter assembly. Turning this
draft adjustment knob clockwise will increase draft and raise the BTU capacity. Turning knob counterclockwise will decrease draft
and lower the BTU capacity. The SS2G is factory set for the highest draft (BTU capacity).
IMPORTANT:
Before proceeding, close all windows, doors and fireplace dampers. Turn on all appliances in the structure that exhaust indoor air
such as clothes dryer, exhaust fans, range hoods, bathroom and whole house exhaust fans. Failure to perform the draft adjust-
ment procedure may cause a poor vent system installation possibly resulting in fire, carbon monoxide poisoning, explosion, per-
sonal injury or property damage.
1. Place the heating system into operation. NOTE: there will be a slight pause between venter operation and burner operation. If
installation uses a barometric draft control adjust it to the minimum or least draft setting. Allow heater to operate for 5 minutes.
2.
PREFERRED METHOD:
MUST HAVE DRAFT GAUGE AVAILABLE
Sample draft one foot after draft hood, diverter or barometric draft control using a draft gauge. If the draft reading is in excess of
-0.05” W.C. turn the draft adjustment knob on the SS2G counterclockwise so that a draft reading of -0.02” to -0.05” W.C. is
obtained. Never adjust draft to a setting of less than -0.02” W.C. If the vent system is terminated on a wall subject to prevailing
winds a -0.05” W.C. draft setting is recommended.
3. If a draft gauge is not available test for spillage at the draft hood, diverter or barometric draft control using the flame from a
match, lighter or candle and determine the following:
A. The flame or smoke is being drawn into the draft hood, diverter or barometric draft control.
B. The main burner is burning properly, i.e. no floating, lifting or flash back.
C. If the heater has a two stage or modulating gas valve verify that burner operates properly at
both low and high fire.
If the draft appears excessive turn the draft adjustment knob counterclockwise and repeat
steps A through C.
4. Lock the draft adjustment knob in place by tightening the locking nut behind the bracket,
(See Diagram K).
5. Turn off appliances and exhaust fans activated for draft adjustment procedure.
DIAGRAM K
COMBUSTION AIR
Adequate combustion air is vital for proper combustion and for safe venting. Likewise, for proper SS2G performance, adequate
combustion air must be available to the appliance. Many installers assume adequate combustion air is present, especially in older
homes. In some cases this is a false assumption, because many older homes have been made "tight" due to weatherization. Size
the combustion air opening(s) into the appliance room as outlined NFPA 54/NFPA 211. When installing a SS2G, it is not neces-
sary to supply any more combustion air than normally required when conventional venting. Common symptoms of inadequate
combustion air include: Fan Proving Switch short cycling, odor present at the end of burner cycle, outside air enters the structure
through the SS2G Vent System on SS2G/Appliance off cycle.
FINAL SYSTEM OPERATION CHECK-OUT
1. Adjust thermostat or appliance controls to call for heat.
2. Verify that the SS2G operates first, prior to burner ignition.
Allow heating equipment and SS2G to operate continuously while performing steps 3-5.
3. Close all doors and windows of the building. If heating equipment is installed in utility room or closet, close the entrance door to
this room. Close fireplace dampers.
4. Turn on all appliances in the structure that exhaust indoor air during their operation, e.g. turn on clothes dryer and exhaust fans
such as range hoods, bathroom exhaust and whole house fans.
5. Allow SS2G and equipment to operate for at least 15 minutes. Tripping of the burner circuit by the Fan Prover Switch during the
15 minute operation indicates an unsafe operating condition. Turn fuel supply off to appliance and DO NOT OPERATE
UNTIL UNSAFE VENTING CONDITION IS INVESTIGATED BY QUALIFIED SERVICE PERSONNEL.
6. Turn thermostat or equipment controls to the "off" position. Verify that the post-purge timer operates the SS2G for approximately
45 seconds while burner is not firing before the SS2G turns off.
7. Return all windows, doors and exhaust fans to their original conditions of use.
Summary of Contents for SS2G SIDESHOT (DISCONTINUED) 8504075 REV 1 1198
Page 10: ...9 ...