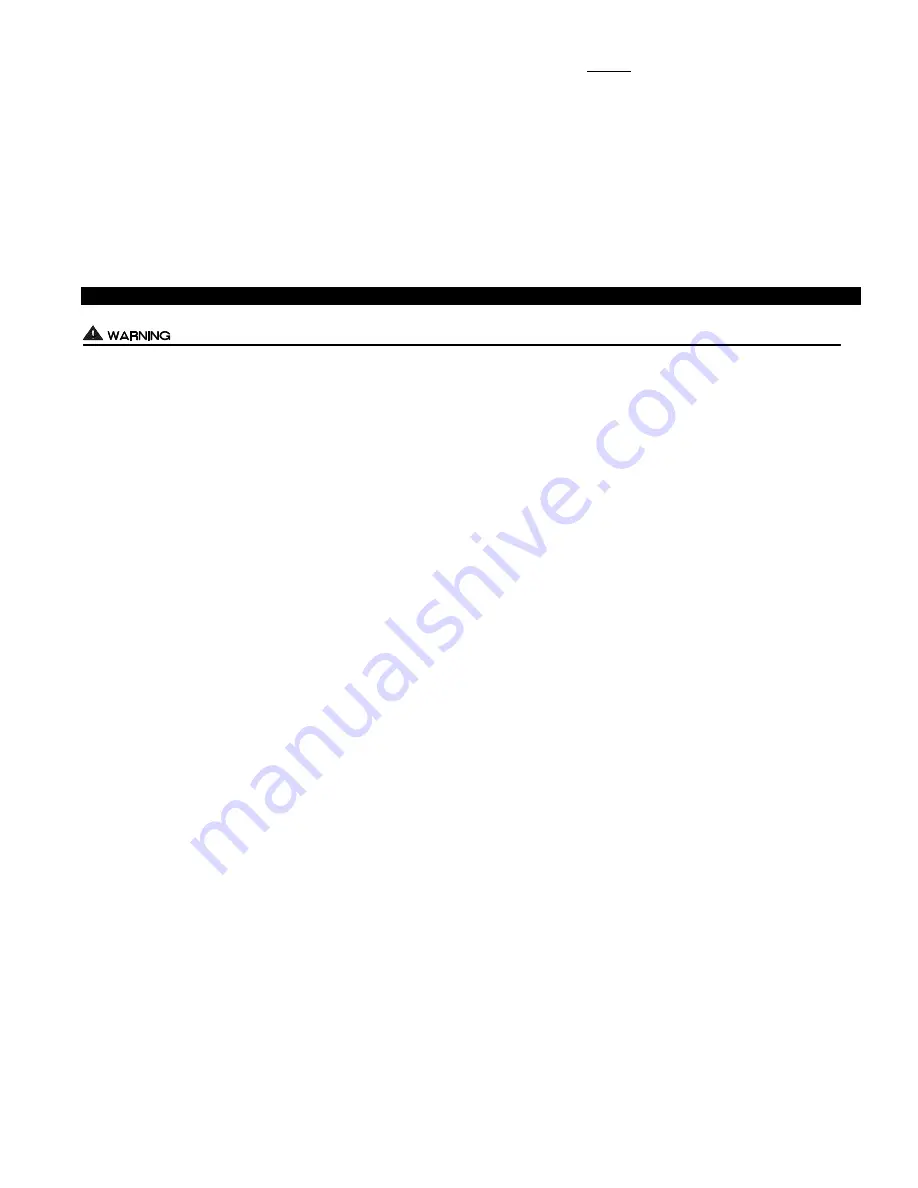
Combustion Air:
Modern construction methods and materials have reduced natural air infiltration rates to extremely low levels.
Even older homes can lack adequate air for combustion, when insulation upgrades and other weatherization methods have been
installed. It is recommended that fuel burning appliances have dedicated sources of outside air for combustion. This may be sim-
ply accomplished by running a properly sized duct from outdoors and terminating it near the burner air intake. Accessory air
intakes are available that connect to the burner motor, using it to pull in the outdoor air. The Tjernlund IN-FORCER
TM
Combustion
Air Intake tempers the raw outdoor air as it is delivered to the burner. Without a source of outdoor air for combustion, a tight
home's negative pressures will draw odors back through the venting system during the appliance off cycle.
Chronic Oil Odor Conditions:
Certain features of the specific appliance and installation, e.g. high heat-retention combustion
chamber; low-mass, dry-base; piping system design; oil impurities; air in lines, can all contribute to an increased production of oil
odor and cannot always be anticipated. For extreme cases of oil odor nuisance Tjernlund recommends the practice of post-purg-
ing the burner during the vent system post-purge. A burner post-purge cycle can eliminate any shortcomings of compatibility
between the specific installation and the SideShot. Burner post-purge kits, such as, Tjernlund's P/N 950-2043, are available from
most oil equipment distributors. Burner post-purge kits should be used on installations where the combustion air is being ade-
quately supplied, yet oil odors continue.
TROUBLESHOOTING ELECTRICAL PROBLEMS
The following guide is intended to be used if a problem occurs during the use of the SS1 side wall vent system. It may be neces-
sary to measure voltage during troubleshooting.
Extreme caution must be exercised to prevent injury.
If you are unable to determine the defective part with the use of this
guide, call your Tjernlund distributor or Tjernlund Products direct at 1-800-255-4208 for further assistance.
IMPORTANT:
To reset faults, verify fault by checking the LEDs and then remove call for heat.
LED STATUS & FAULT INDICATORS
LED INDICATOR LIGHTS
LED #1 (Amber) Appliance call for heat.
LED #2 (Green) Safety circuit through P1 & P2 (SS1 Limit & Fan Prover) is verified “Open” upon start-up. Burner circuit is
energized with contact closure from terminal 3 to 4. Also verifies SS1 prover & limit are closed during run cycle.
LED #3 (Green) Power switched to SS1 Motor from L to MTR & M.
LED #4 (Red)
Status indicator.
LED #5 (Red)
115 VAC power supplied to board. Also used as status indicator.
LED INDICATOR LIGHT STATUS & FAULTS
LED #4 & #5 Flashing Alternately
= Prover start up fault. SS1 Prover contacts “Closed” across P1 & P2 upon appliance call
before SS1 is turned on. Prover status check
must
be activated, see page 5.
LED #4 & #5 Flashing in Unison
= Fan Prover circuit is “Open” longer than 60 seconds on start-up or 10 seconds during run
cycle. Prover or Limit contacts are not staying “Closed” across P1 & P2 safety circuit.
LED #4 Flashing & #5 on Continuous = System in Pre-Purge. (Pre-Purge options 0, 15, 30, 60 seconds)
LED #5 Flashing & #4 on Continuous = System in Post-Purge. (Post-Purge options 0, 30 seconds or 1, 2, 4, 8, 16 minutes)
SYMPTOM 1: SS1 OPERATES CONTINUOUSLY
Verify that Venter is not in post-purge mode which could last up to 16 minutes. A factory post-purge has been set for 2 minutes.
LED #4 (Red) will be on continuously and LED #5 will be flashing during post-purge. A Venter pre-purge could also be set for up
to 1 minute. LED #4 (Red) will be flashing and LED #5 will be on continuously during a Venter pre-purge. See “Pre / Post-Purge
Settings” on page 5.
Verify that LED #1 (Amber) is not lit.
Yes, LED #1 (Amber) is lit: Check interlock wiring. UC1 control is receiving constant call for heat signal.
LED #1 (Amber) is not lit: Replace UC1 circuit board part number 950-8801.
SYMPTOM 2: SS1 MOTOR DOES NOT OPERATE
Verify that UC1 control has power, LED #5 (Red) should be lit.
No: Check circuit breaker, disconnect switches and wiring.
Yes, LED #5 (Red) is lit: Verify that the interlocked burner is calling for heat, LED #1 (Amber) should be lit.
No, LED #1 (Amber) is not lit: Verify interlock wiring and that thermostat/aquastat is adjusted to call for heat. Verify that the RED
voltage selection jumper is installed so that it matches the voltage of the interlocked burner.
20