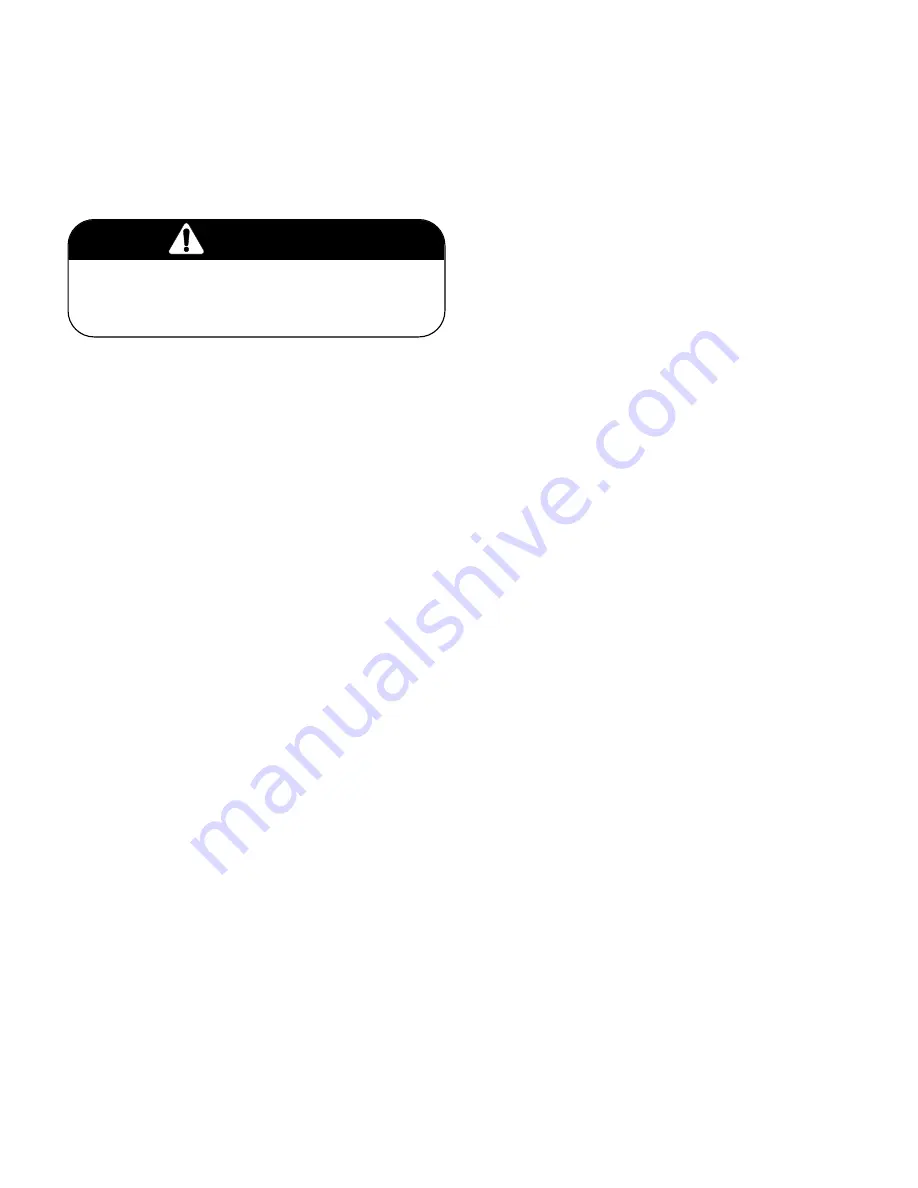
Safety - Basic Safety Rules & Precautions
1.3.4
Before Beginning To Work
Fasten safety belt.
Always allow for adequate warm-up of the engine
and hydraulic oil, particularly when ambient
temperature is below 32
o
F (0
o
C). Refer to cold
weather starting instructions in Section 4.1.
Check operation of emergency escape
hatch every 50 hours. See Section 5.3 for
procedures.
Check all controls for proper operation. If a control
is malfunctioning, stop immediately and have the
problem corrected before resuming work.
Be aware of all obstacles and hazards around you;
stumps, slopes, ditches, overhead wires, etc.
Before moving the machine, check position of frame
articulation joint. Normal forward travel is with the
frame articulation joint behind the cab. When the
frame articulation joint is in front of the cab the
reverse steer feature, see Section 3.3, should be
activated otherwise the steering controls must be
worked opposite.
During Machine Operation
Adhere strictly to all regulations at the work site
pertaining to the operation of this machine.
Know the capacities and limitations of the machine
and DO NOT exceed them. Lift capacity decreases
as the load moves away from the machine.
If a failure occurs that causes the loss of implement
control, steering, brakes or engine, stop machine
motion as quickly as possible, lower the grapple to
the ground and shut down machine. Leave
machine parked until repairs can be made or the
machine can be towed.
Keep eye contact on the grapple and its
immediate surroundings at all times when handling
the load.
Maintain a safe operating distance between the
machine and other equipment and personnel.
NEVER swing the boom or grapple above the
heads of bystanders.
When moving the machine, watch that enough
clearance is available on both sides and above
the boom. Extra clearance may be required
particularly where ground is uneven.
Maintain a safe operation distance from hazards
such as steep drop-offs, deep ditches and areas
where the ground may be unstable and allow the
machine to slide or tip.
Drive machine with care and at speeds compatible
with job conditions. Use extra care on rough
ground, slopes and when turning the machine.
Approach an area where overhanging electrical
power lines are present with EXTREME CAUTION.
Serious injury or death by electrocution could result
if the machine or its grapple is not kept a safe
distance away from these lines. Keep machine and
booms at least 10 ft. (3m), plus an additional 1/2”
(10mm) for each 1,000 volts over 50,000 volts, from
any power line. If state/province, local or job site
regulations require even greater safety
distances than stated above, adhere strictly to those
regulations for your protection.
Keep grapple close to ground level, approximately
15” (40 cm), while traveling.
Keep loads close to the machine when traveling or
swinging and avoid conditions and operating
practices that may lead to tipping or overturning the
machine.
On steep slopes, travel as straight up and down as
possible and always carry any load on the uphill
side of the machine.
Always lower the booms so that the grapple rests on
the ground whenever operation is stopped;
regardless if the engine is running or not.
Use a recommended vehicle when transporting the
machine between jobsites.
When transport of machine is required, make sure
that it is adequately secured to the vehicle. Even
though the machine’s parking brakes are fully
engaged, block the wheels to prevent movement
during transport.
Form M251
WARNING