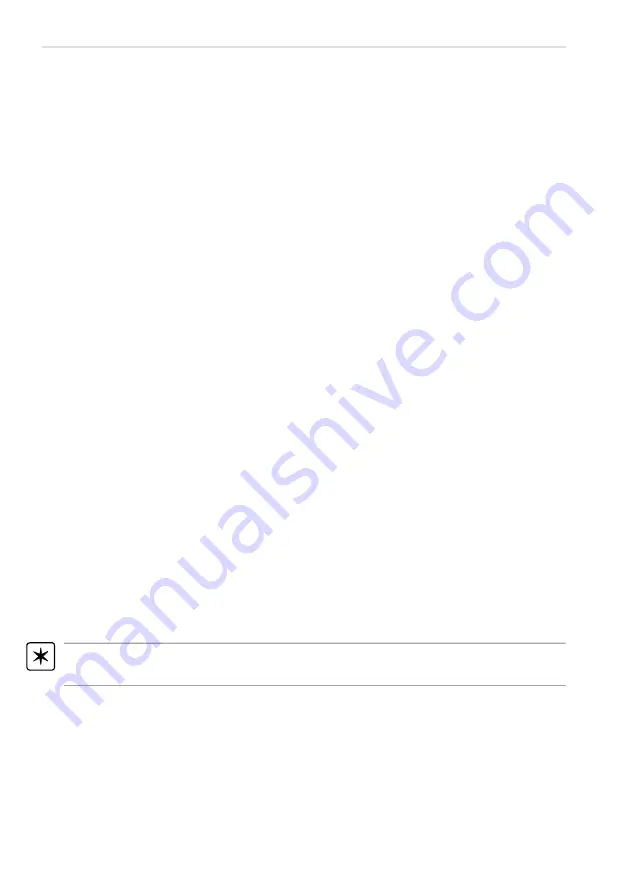
15
Chapter 3 Operation
Encoder Position Setpoint Window (counts)
- When an encoded move is corrected,
the system attempts to 'reach' a required position setpoint (i.e. encoder count). This
parameter specifies a window of acceptability (in encoder counts) that the system
must achieve.
For example, when set to a value of 1, the system must get to within 1 encoder count
either side of the required position. This setting is useful for noisy systems (i.e.
mechanical noise causing jitter on the encoder count) where achieving a precise
encoder count may prove difficult.
For an encoder calibration factor of 10000/mm, a value of 1 for this setting means the
system will position to -0.1micron of the required position.
Single Microstepping Window
- Specifies a window within which the system attempts
to reach the required position setpoint by single microstep stepping - a very accurate
stepping mode. For example, if this parameter is set to a value of 10, and if the
encoded move initially ends up within 10 counts (1 micron for a calibration factor of
10000) either side of the required position, the system will single microstep to reach
the required position.
If at the end of the initial encoded move, the system detects the encoder position is
outside of this window, then the system steps at whatever multiple of microsteps is
specified by the 'Correction Move Distance' parameter described below, until the
encoder position falls within the Single Microstepping Window and single
microstepping can take place.
Stop Short Distance
- When the 'Position (Stop Short & Correct)’ position correction
mode is enabled (described in the Encoder Operation section), this parameter
specifies the distance (in microsteps) to stop short of an encoded move.
Assuming 25600 microsteps per revolution of the stepper motor and a 1mm pitch lead
screw, a value of 250 equates to approximately 10 microns stop short distance.
Correction Move Distance
- Specifies the size of correction step (in microsteps) to use
when the system issues correction moves outside of the distance set in the ‘Single
Microstepping Window’ parameter described above.
Assuming 25600 microsteps per revolution of the stepper motor and a 1mm pitch lead
screw, a value of 5 equates to approximately 0.2 micron step size.
Note
. These settings are set to suitable defaults automatically when an encoded stage
type has been associated with the motor channel (using the APT Config utility).