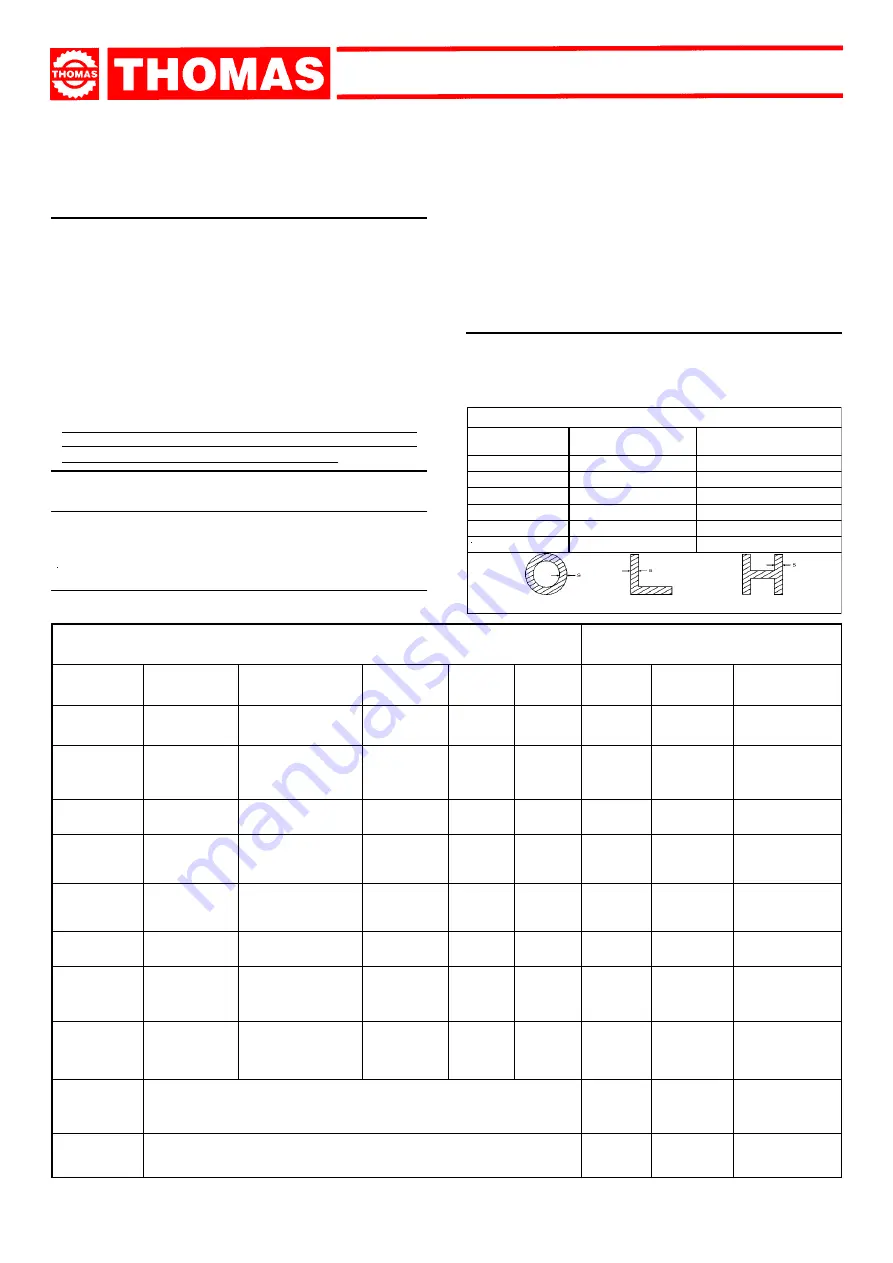
16
SAR 460 SA G
TYPES OF STEEL
CHARACTERISTICS
USE
I
UNI
D
DIN
F
AF NOR
GB
SB
USA
AISI-SAE
Hardness
BRINELL
HB
Hardness
ROCKWELL
HRB
R=N/mm²
Construction
steels
Fe360
Fe430
Fe510
St37
St44
St52
E24
E28
E36
----
43
50
----
----
----
116
148
180
67
80
88
360÷480
430÷560
510÷660
Carbon
steels
C20
C40
C50
C60
CK20
CK40
CK50
CK60
XC20
XC42H1
----
XC55
060 A 20
060 A 40
----
060 A 62
1020
1040
1050
1060
198
198
202
202
93
93
94
94
540÷690
700÷840
760÷900
830÷980
Spring
steels
50CrV4
60SiCr8
50CrV4
60SiCr7
50CV4
----
735 A 50
----
6150
9262
207
224
95
98
1140÷1330
1220÷1400
Alloyed steels for
hardening and
tempering and for
nitriding
35CrMo4
39NiCrMo4
41CrAlMo7
34CrMo4
36CrNiMo4
41CrAlMo7
35CD4
39NCD4
40CADG12
708 A 37
----
905 M 39
4135
9840
----
220
228
232
98
99
100
780÷930
880÷1080
930÷1130
Alloyed
casehardening
steels
18NiCrMo7
20NiCrMo2
----
21NiCrMo2
20NCD7
20NCD2
En 325
805 H 20
4320
4315
232
224
100
98
760÷1030
690÷980
Alloyed for
bearings
100Cr6
100Cr6
100C6
534 A 99
52100
207
95
690÷980
Tool steel
52NiCrMoKU
C100KU
X210Cr13KU
58SiMo8KU
56NiCrMoV7C100K
C100W1
X210Cr12
----
----
----
Z200C12
Y60SC7
----
BS 1
BD2-BD3
----
----
S-1
D6-D3
S5
244
212
252
244
102
96
103
102
800÷1030
710÷980
820÷1060
800÷1030
Stainless
steels
X12Cr13
X5CrNi1810
X8CrNi1910
X8CrNiMo1713
4001
4301
----
4401
----
Z5CN18.09
----
Z6CDN17.12
----
304 C 12
----
316 S 16
410
304
----
316
202
202
202
202
94
94
94
94
670÷885
590÷685
540÷685
490÷685
Copper alloys
Special brass
Bronze
Aluminium copper alloy G-CuAl11Fe4Ni4 UNI 5275
Special manganese/silicon brass G-CuZn36Si1Pb1 UNI5038
Manganese bronze SAE43 - SAE430
Phosphor bronze G-CuSn12 UNI 7013/2a
220
140
120
100
98
77
69
56,5
620÷685
375÷440
320÷410
265÷314
Cast iron
Gray pig iron G25
Spheroidal graphite cast iron GS600
Malleable cast iron W40-05
212
232
222
96
100
98
245
600
420
MATERIAL
CLASSIFICATION AND
CHOICE OF TOOL
9
Since the aim is to obtain excellent cutting quality, the vari-
ous parameters such as hardness of the material, shape
and thickness, transverse cutting section of the part to be
cut, selection of the type of cutting blade, cutting speed
and control of saw frame lowering.These specifications
must therefore be harmoniously combined in a single oper-
ating condition according to practical considerations and
common sense, so as to achieve an optimum condition that
does not require countless operations to prepare the ma-
chine when there are many variations in the job to be
performed.The various problems that crop up from time to
time will be solved more easily if the operator has a good
knoledge of these specifications.
WE THEREFORE RECOMMEND YOU TO ALWAYS USE
GENUINE "THOMAS" SPARE BLADES THAT GUARANTEE
SUPERIOR QUALITY AND PERFORMANCE.
9.1 - Definition of materials
The table at the foot of the page lists the characteristics of the
materials to be cut, so as to choose the right tool to use.
9.2 - Selecting blade
First of all the pitch of the teeth must be chosen, in the other
BLADE TEETH SELECTION TABLE
THICKNESS MM
Z CONTINUOUS
TOOTH DESIGN
Z COMBO
TOOTH DESIGN
TILL 1.5
14
10/14
FROM 1 TO 2
8
8/12
FROM 2 TO 3
6
6/10
FROM 3 TO 5
6
5/8
FROM 4 TO 6
6
4/6
MORE THAN 6
4
4/6
S = THICKNESS
words, the number of teeth per inch (25,4 mm) suitable for the
material to be cut, according to these criteria:
- parts with a thin and/or variable section such as profiles, pipes
and plate, need close toothing, so that the number of teeth
used simultaneously in cutting is from 3 to 6;
- parts with large transverse sections and solid sections need
widely spaced toothing to allow for the greater volume of the
shavings and better tooth penetration;
- parts made of soft material or plastic (light alloys, mild bronze,
teflon, wood, etc.) also require widely spaced toothing;
- pieces cut in bundles require combo tooth design.
9.3 - Teeth pitch
As already stated, this depends on the following factors:
- hardness of the material
- dimensions of the section
- thickness of the wall
Summary of Contents for SAR 460 SA G DIGIT
Page 21: ...21 SAR 460 SA G TAVOLA 1...
Page 22: ...22 SAR 460 SA G TAVOLA 2...
Page 23: ...23 SAR 460 SA G GRUPPO ARCO TAVOLA 3...
Page 24: ...24 SAR 460 SA G TAVOLA 4...
Page 25: ...25 SAR 460 SA G TAVOLA 5...
Page 26: ...26 SAR 460 SA G TAVOLA 6...
Page 27: ...27 SAR 460 SA G TAVOLA 7 1 SET 2 SET...
Page 30: ...30 SAR 460 SA G 11 SCHEMI ELETTRICI 11 1 Schema elettrico trifase THOMAS THOMAS...
Page 31: ...31 SAR 460 SA G THOMAS THOMAS...
Page 32: ...32 SAR 460 SA G THOMAS THOMAS...
Page 33: ...33 SAR 460 SA G THOMAS THOMAS...
Page 34: ...34 SAR 460 SA G THOMAS THOMAS THOMAS THOMAS...
Page 35: ...35 SAR 460 SA G 11 2 Schema elettrico idraulico...