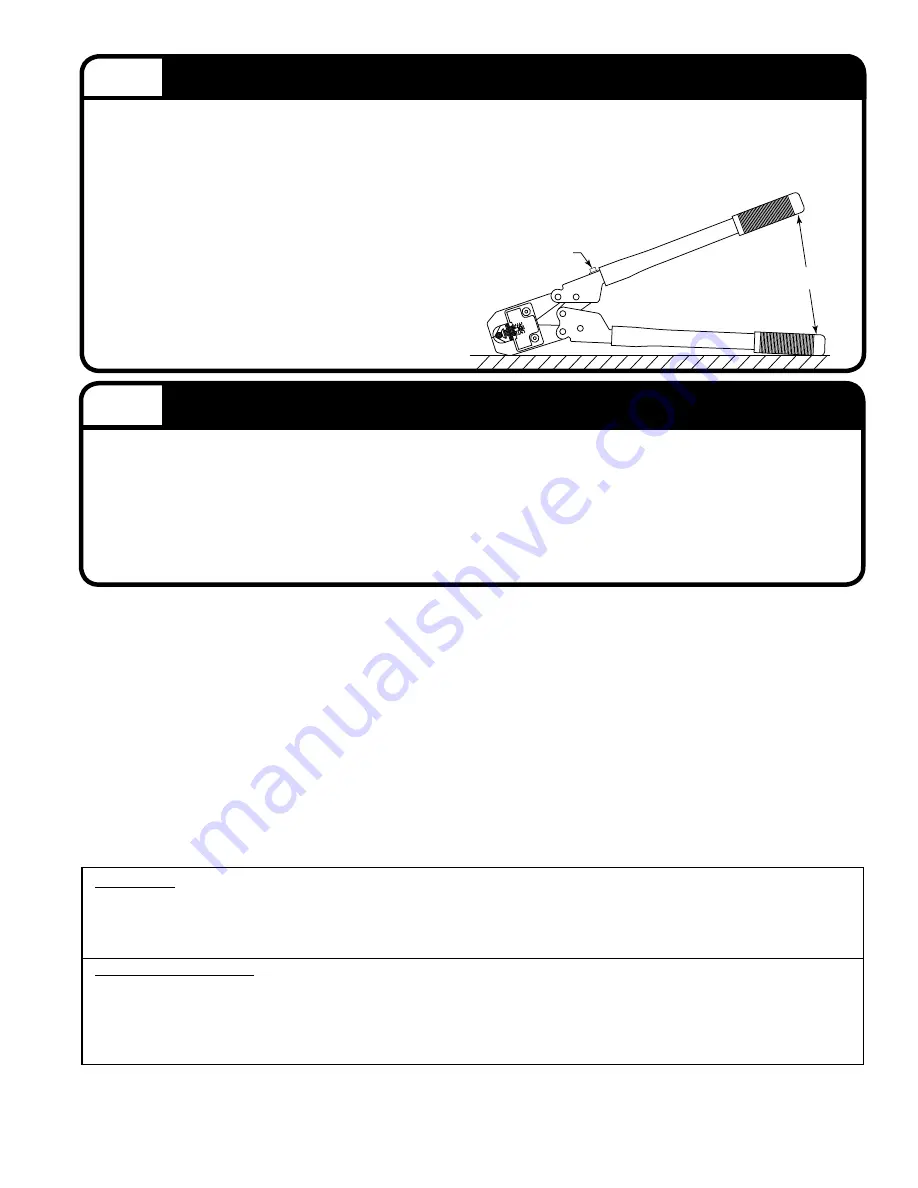
GAUGING PROCEDURE
03
For Parts or Service, contact the tool service center at 1-800-284-TOOL (8665).
CHECKING HANDLE ADJUSTMENT
1. Lay the tool on a flat surface as shown in Figure 3.
Open handle and release it so that it will close of its
own weight.
2. Measure the handle spread distance at the inner
surface of the handle tips as shown in Figure 3.
3. If the distance is 14”±1/2” the tool is adjusted
properly. If not, the tool should be adjusted.
HANDLE ADJUSTMENT PROCEDURE
02
© 2007 Thomas & Betts. All Rights Reserved.
Adjustment Screw
HANDLE ADJUSTMENT PROCEDURE
1. Turn Adjustment screw clockwise to increase
handle spread and counterclockwise to decrease
handle spread (Refer to Figure 3).
14” ±1/2”
Figure 3
TA01454 B page 2 of 2
WARRANTY: Thomas & Betts sells this product with the understanding that the user will perform all necessary tests to determine
the suitability of this product for the user’s intended application. Thomas & Betts warrants that this product will be free from defects
in materials and workmanship for the period stated on the enclosed warranty card. Upon prompt notification of any warranted
defect, Thomas & Betts will, at its option, repair or replace the defective product or refund the purchase price. Proof of purchase is
required. Misuse or unauthorized modification of the product voids all warranties.
Limitations and Exclusions:
THE ABOVE WARRANTY IS THE SOLE WARRANTY CONCERNING THIS PRODUCT, AND IS IN
LIEU OF ALL OTHER WARRANTIES EXPRESS OR IMPLIED, INCLUDING BUT NOT LIMITED TO ANY IMPLIED WARRANTY
OF MERCHANTABILITY OR FITNESS FOR A PARTICULAR PURPOSE, WHICH ARE SPECIFICALLY DISCLAIMED. LIABILITY
FOR BREACH OF THE ABOVE WARRANTY IS LIMITED TO COST OF REPAIR OR REPLACEMENT OF THE PRODUCT,
AND UNDER NO CIRCUMSTANCES WILL THOMAS & BETTS BE LIABLE FOR ANY INDIRECT, SPECIAL, INCIDENTAL OR
CONSEQUENTIAL DAMAGES.
Thomas & Betts Corporation
Memphis, Tennessee
www.tnb.com
1. Close the tool jaws until they bottom.
2. Select the side of the tool to be gauged (For copper or aluminum).
3. Move indenter until the pointer slot aligns with the selected cable size. The adjusting wheel should be in a
positive detented position. For copper cables select 2/0. For aluminum cables select 2 GA.
4. Gauge the crimping area with a suitable pin gauge. The gauge diameter must fall within .405 ±.010 for 2/0
copper cables and .350 ±.010 for 2 GA aluminum cables.