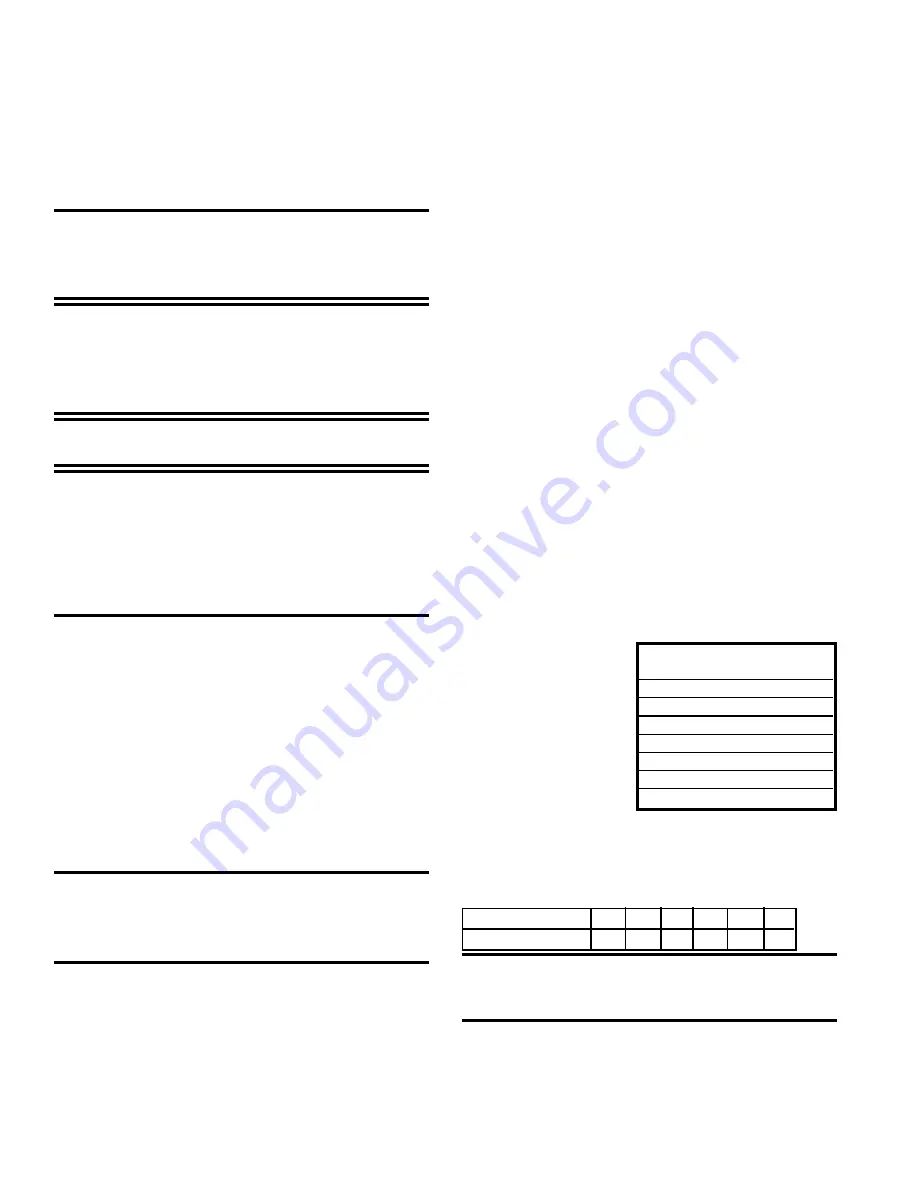
Form 405, Page 2
Separated-combustion units are designed to separate the air for com-
bustion and the flue products from the environment of the building in
which the unit is installed. Separated-combustion appliances are rec-
ommended for use in dust laden and some corrosive fume environments
or in buildings with negative pressure (up to .15" w.c.). If installed as a
separated-combustion system, the heater must be equipped with both
combustion air and exhaust piping to the outdoors. All Model CAUA
heaters must be vented to the outdoors.
WARNING: Should overheating occur, or the gas
supply fail to shut off, shut off the manual gas valve
to the appliance before shutting off the electrical
supply.
WARNING: Do not use this appliance if any part
has been under water. Immediately call a qualified
service technician to inspect the appliance and
replace any gas control which has been under
water.
CAUTION: Do not locate the heater where it may
be exposed to water spray, rain or dripping water.
HAZARD INTENSITY LEVELS
1. DANGER: Failure to comply will result in severe
personal injury or death and/or property damage.
2. WARNING: Failure to comply could result in severe
personal injury or death and/or property damage.
3. CAUTION: Failure to comply could result in minor
personal injury and/or property damage.
1. Installation Codes
These units must be installed in accordance with local building codes. In
the absence of local codes, in the United States, the unit must be in-
stalled in accordance with the National Fuel Gas Code ANSI Z223.1a
(latest edition). A Canadian installation must be in accordance with the
CAN/CGA B149.1 and B149.2 Installation Code for Gas Burning Ap-
pliances and Equipment. These codes are available from CSA Informa-
tion Services, 1-800-463-6727. Local authorities having jurisdiction
should be consulted before installation is made to verify local codes and
installation procedure requirements.
2. Warranty
Refer to the limited warranty information on the Warranty Card in the
"Owner's Envelope".
Warranty is void if ...
a. Wiring is not in accordance with the diagram furnished with the
heater.
b. The unit is installed without proper clearance to combustible
materials.
3. Uncrating and Preparation
This unit was test operated and inspected at the factory prior to crating
and was in operating condition. If the heater has incurred any damage in
shipment, file a claim with the transporting agency.
Check the rating plate for the gas specifications and electrical character-
istics of the heater to be sure that they are compatible with the gas and
electric supplies at the installation site.
Read this booklet and become familiar with the installation require-
ments of your particular heater. If you do not have knowledge of local
GENERAL (Cont'd)
5. Mounting
the Heater
Check the supporting structure to be used to verify that it has suffi-
cient load-carrying capacity to support the weight of the unit. The
heater must be level.
Approximate Net Weight (lbs)
Size
150
200
250
300
350 400
Weight (lbs)
288
300
380
394
445
460
WARNING: Unit must be level for proper
operation. Do not place or add additional weight
to the heater. See Hazard Levels, page 2.
Determine the position of the heater with regard to venting, combus-
tion air, gas supply connection, electrical supply connection, and inlet
air opening. Either cut out the inlet air opening (requires tin snips or
aviation shears) now or when attaching ductwork or filter cabinet. Use
caution when cutting the opening as the cut edges of the metal will be
sharp. NOTE: If ordered with an optional inlet base, the heater is
shipped with a bottom inlet air opening.
requirements, check with the local gas company or any other local
agencies who might have requirements concerning this installation.
Before beginning, make preparations for necessary supplies, tools, and
manpower.
Shipped-Separate Accessories
•
Concentric Adapter and Vent Terminal - If the heater is installed
as a separated-combustion system, a concentric adapter assembly
is required. The concentric adapter and parts are shipped in a sepa-
rate carton. Be sure that the shipped-separate carton is at the instal-
lation site. See Paragraph 7A.
•
Filter Cabinet - The return air filter cabinet is shipped separately
for field installation over the inlet air opening of the heater. The inlet
air opening location is determined by the application. The filter
cabinet can attach at the opening on either the rear, the left side, or
right side of the unit. Follow the installation instructions included
with the cabinet.
•
Cased Cooling Coil - Model ACU cooling coils are designed for
the Model CAUA heaters. The coil cabinet is shipped separately
for installation over the discharge opening of the heater.
•
Mixing Cabinet - If outside air is desirable, a mixing cabinet with
dampers is available. The mixing cabinet is field attached to the rear
of the unit. Check to be sure that the mixing box is the configuration
ordered. Follow the installation instructions included with the
shipped-separate package.
•
Inlet Base - If an optional inlet base is included, follow the instruc-
tions included with the inlet base to select the location. The heater
mounts on the inlet base; heater has a bottom inlet air opening.
•
Discharge Plenum - The discharge plenum is shipped separately
for installation over the discharge opening of the heater. If the dis-
charge plenum and a cased cooling coil are part of the installation,
the discharge plenum is factory attached to the cooling coil casing.
Also, shipped with the heater are the parts needed to install a conden-
sate drain (needed if installing a cooling coil). Other shipped-separate
options could include a gas shutoff valve, a thermostat, a thermostat
guard, and/or a vent cap. Make sure all parts are at the site before
beginning installation.
4. Clearances
Unit must be installed so that
the clearances in the table are
provided for service and in-
spection and for proper spac-
ing from combustible con-
struction.
Required Clearances
(All Sizes)
Right Side
0" (0mm)
Left Side
0" (0mm)
Front
36" (914mm)
Rear
0" (0mm)
Bottom
0" (0mm)
Flue Connector
6" (152mm)
Top
1" (25mm)