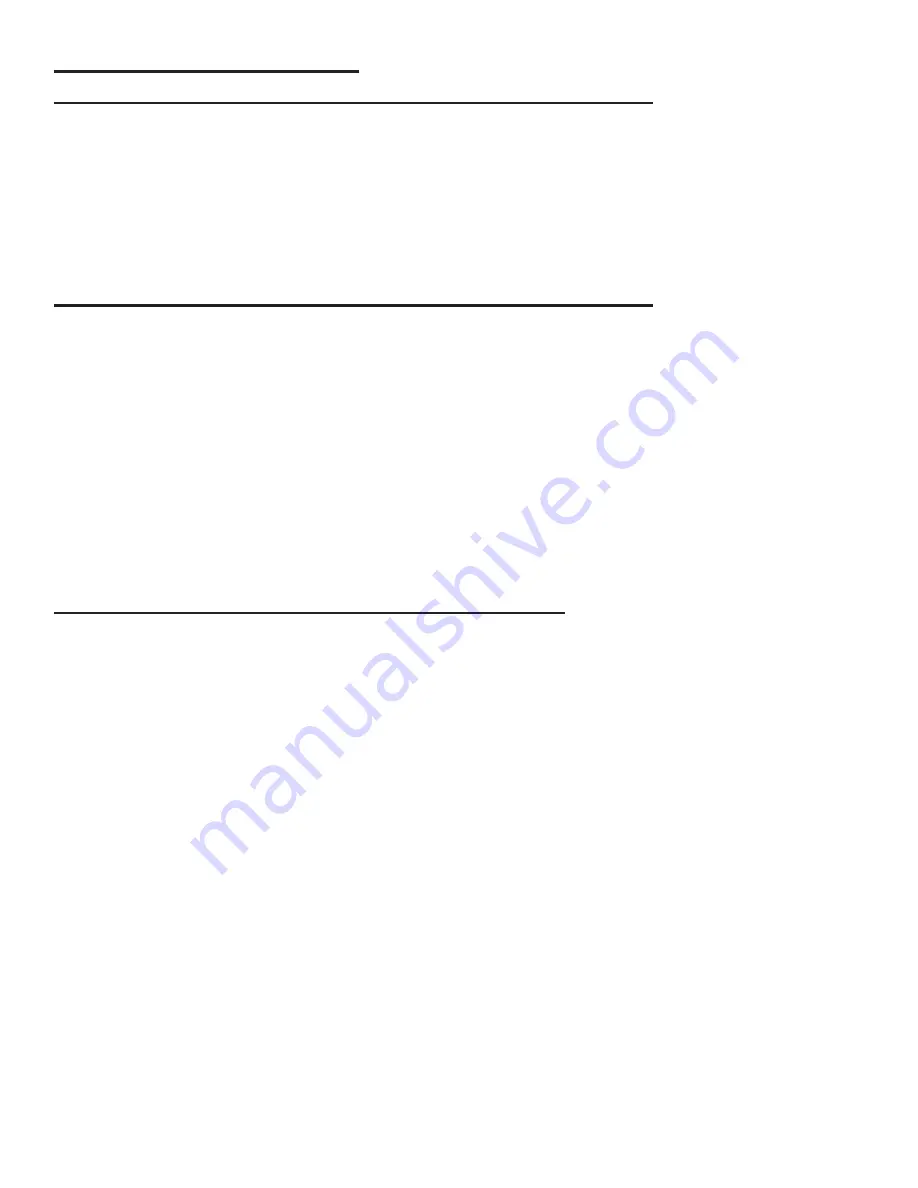
Section 3.0: Decommissioning
Troubleshooting in the field requires turning off the water and steam supply to the emergency safety
shower/eyewash system. Contact the plant safety manager/supervisor and follow proper procedures
for temporarily rendering the safety equipment unusable. Notify all personnel working in the area that
the emergency safety shower/eyewash equipment will be temporarily disabled.
Section 3.1: Troubleshooting and Repair Warning Statement
1.
Close the unit’s steam supply valve.
2.
Activate the shower and eyewash system for a minimum of two minutes to deplete the steam
pressure trapped between the steam supply shutoff valve and the unit.
3. To remove the yellow enclosure, face the unit with outlet connection on your right. Un-clip the side
clamps and pull the bottom of the front cover towards you. The back cover is attached to the heat
exchanger by a stainless bracket and end bolts.
4.
Once trouble shooting is complete, turn the steam supply on and activate the shower for at least
one minute to purge the system.
5.
Insert the temperature-reading device into the eyewash nozzle. Activate the eyewash and record
the temperature several times over a 5-10 minute cycle. Note movement of V3 indicator and o-ring
on the V2 capillary valve
.
Repeat this step for the shower, attaching the temperature-reading
device to the shower-head. Record temperatures, V3 indicator, and capillary valve movement.
Section 3.2: Decommissioning The Unit for Troubleshooting
1.
Close the unit’s steam supply valve.
2.
Activate the shower and eyewash system for a minimum of two minutes to deplete the steam
pressure trapped between the steam supply shutoff valve and the unit.
3. With the system activated, closer the water supply valve to the unit.
4.
To remove the yellow enclosure, face the unit with outlet connection on your right. Un-clip the side
clamps. Pull the bottom of the front cover towards you. The back cover is attached to the heat
exchanger by a stainless bracket and end bolts.
5.
Repair or replace components as needed.
6.
Open the water supply valve to the Heater. Once water is flowing open the steam valve slowly.
Allow he unit to run for at least one minute to purge the system.
7.
Insert the temperature-reading device into the eyewash nozzle. Activate the eyewash and record
the temperature several times over a 5-10 minute cycle. Note movement of V3 indicator and o-ring
on the V2 capillary valve
.
Repeat this step for the shower, attaching the temperature-reading
device to the shower-head. Record temperatures, V3 indicator, and capillary valve movement.
8.
Once the Heater is operating correctly close the steam supply line to the Heater.
9.
Activate the shower and eyewash system for a minimum of two minutes to deplete the steam
pressure trapped between the steam supply shutoff valve and the Heater.
10.
Turn the steam supply back on and activate the shower for at least one minute.
11.
Replace and secure the yellow enclosure.
Section 3.3: Decommissioning The Unit for Repairs
***WARNING: PIPING MAY BE HOT AND HOT WATER
MAY BE TRAPPED IN THE HEATER.
Page 6
Summary of Contents for THERM-O-MIX STATION
Page 13: ...Page 12 Appendix 1 Station Schematic...
Page 14: ...Appendix 2 Station Operating Logic Flow Chart Page 13...
Page 15: ...Page 14 Appendix 3 Typical Installation Schematic...
Page 16: ...Appendix 4 Labeled Station Line Drawing Page 15...
Page 17: ...Page 16 Appendix 5 Hoses and Hose Fittings Line Drawing...