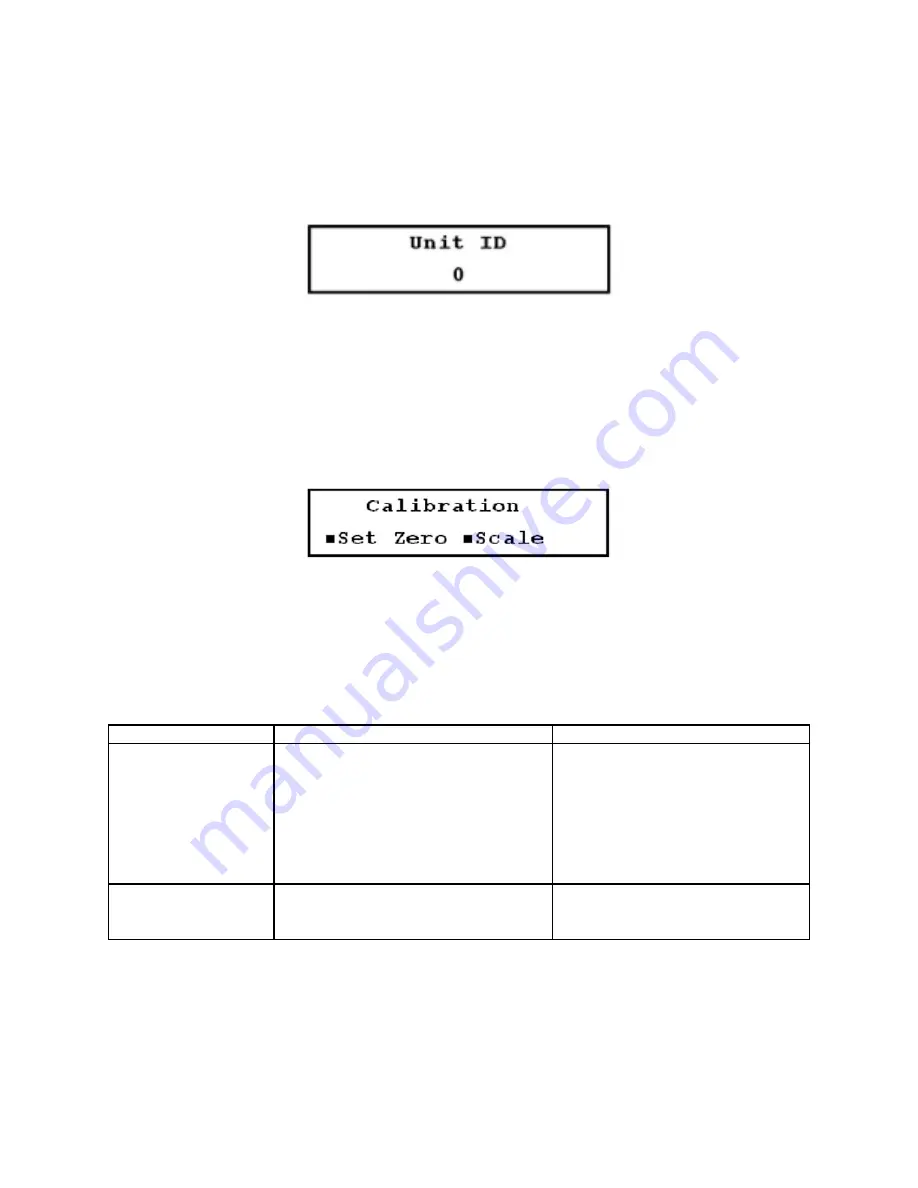
22
..... Additional setup menus within the OPTIONS submenu
6.
Unit ID (identification) Number
setup menu (49): This number is determined by the operator to identify
the specific instrument or site. Any whole number between 1 and 60,000 may be entered
(Figure 3.12-N, below).
F
IGURE
3.12-N
3.13 Additional Setup Menus Within the CALIBR Submenu
*Not included in the Quick Setup configuration
Within the
CALIBR
submenu is the
Calibration Group
menu (50) (Figure 3.13-A, below), which contains 4
setup menus:
Zero Set, Scale, SS Comp, Date
(Menus 51 through 54).
F
IGURE
3.13-A
3.13.1 Zero Set Calibration
An important step in assuring accurate flow measurement is the proper calibration of the instrument and
proper installation. The calibration methods must be performed for the particular pipe that is to be metered.
Table 3 (below) provides guidelines for selecting a calibration method.
Calibration Method
Function
Application
Zero set calibration
Zero flow set
Zeroes the instrument for an actual no
Installations where flow can be
flow condition
stopped
Manual zero set
Applies a manually entered offset to
Where an offset is required
all flow readings
Scale factor
Compensates for manufacturing
Set by the factory to the value
variations in the transducers
imprinted on the transducers
T
ABLE
3
After installing the meter, you may find that a small adjustment to the zero point (zero set calibration) is
required. Zero set calibration allows the meter to read very close to zero under zero flow conditions. There
are two zero set calibration methods in Menu 51: the zero flow set method and the manual zero set
method. View the zero point used by the flowmeter in either of these methods by selecting
Manual
in Menu
51.