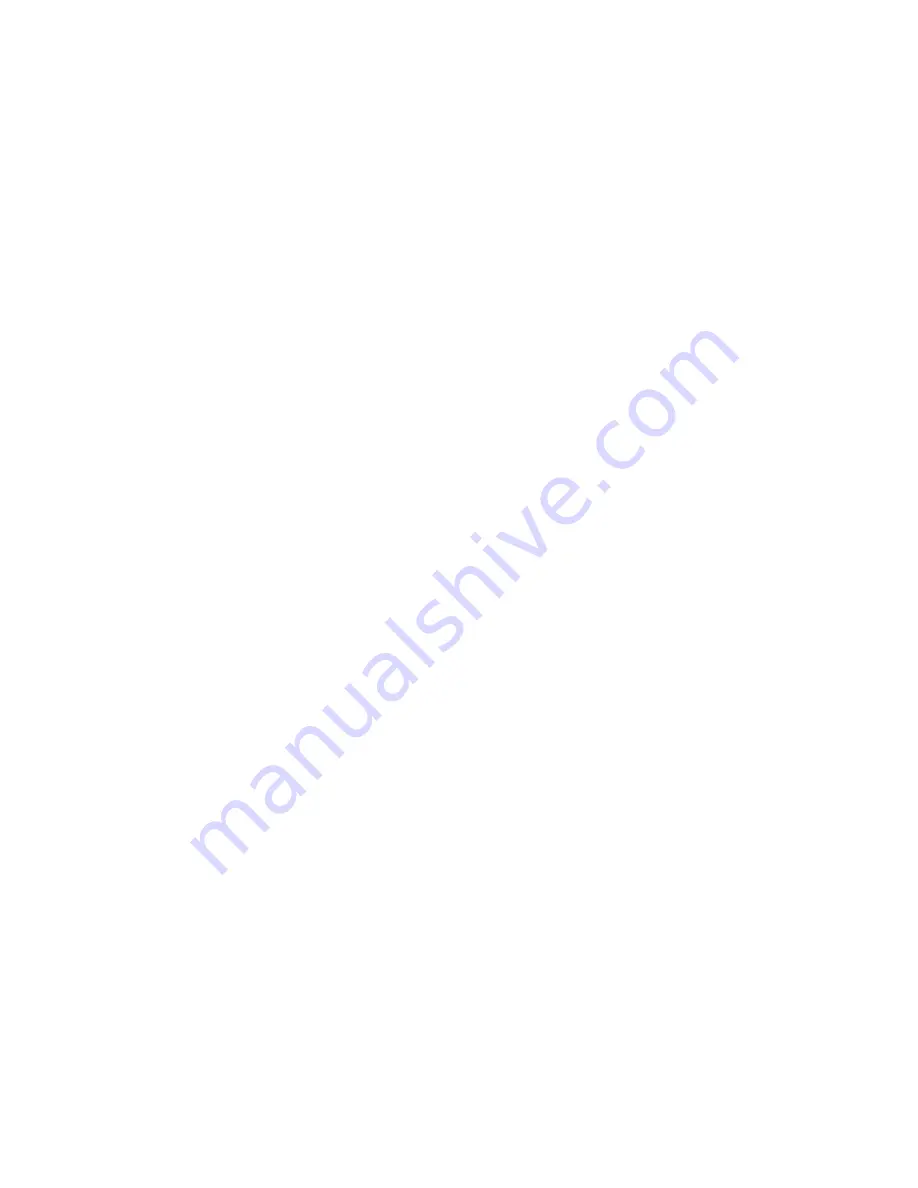
Important
For your future reference and then contacting the factory,
please have the following information readily available:
Model Number:
___________________________
Serial Number:
___________________________
Date Purchased:
___________________________
The above information can be found on the data plate attached
to the equipment. If available, please provide the date
purchased, the source of purchase (manufacturer or specific
agent/rep organization), and purchase order number.
IF YOU NEED ASSISTANCE:
SALES DIVISION
Phone:
1-866-984-3766
1-866-9-THERMO
LABORATORY PARTS and SERVICE
Phone:
1-800-438-4851
TECHNICAL SUPPORT
Phone:
1-800-438-4851