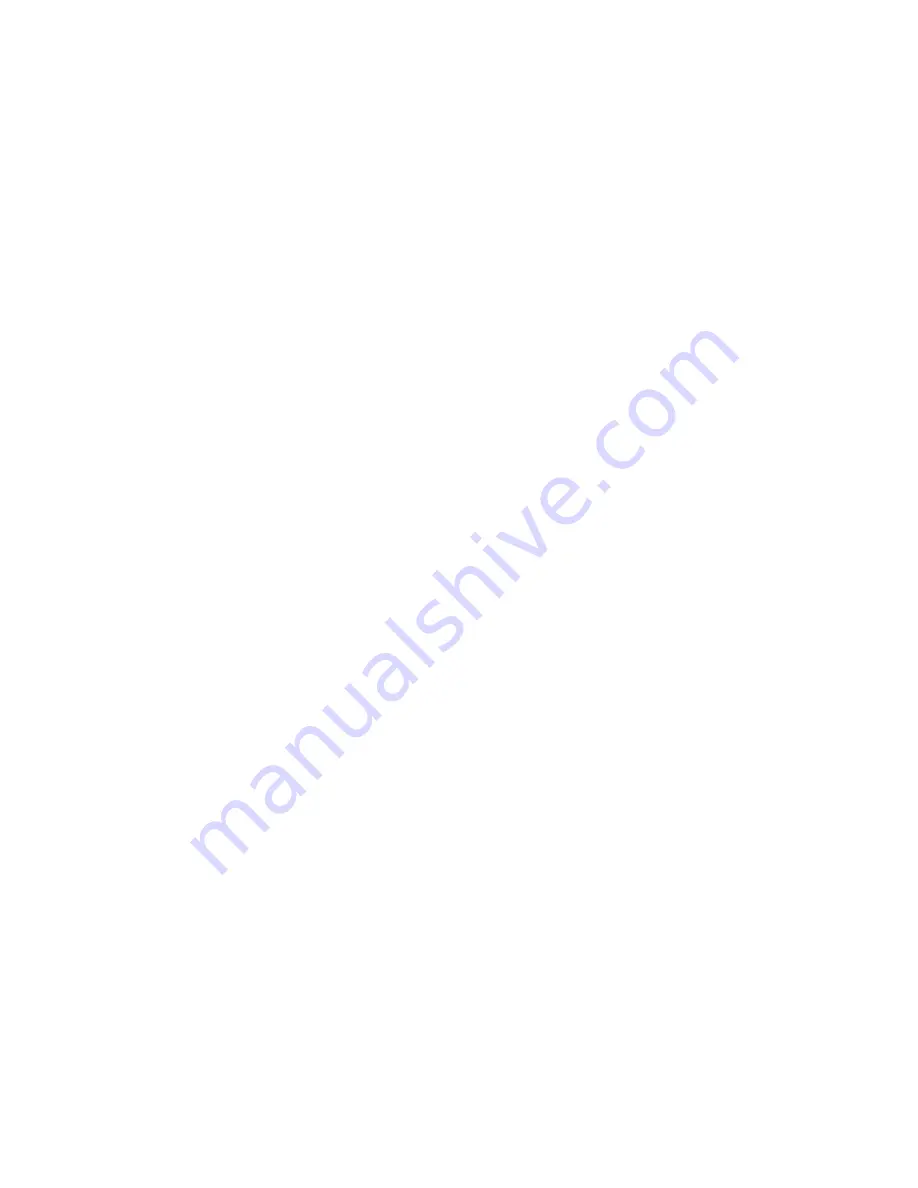
33
The heat exchanger may also be cleaned through the flue pipe connection. With the
furnace turned off and at room temperature, carefully remove the vent connector and
the heat exchanger flue pipe, if equipped, to inspect and clean the heat exchanger.
The inner radiator of the heat exchanger may be cleaned from the inside of the
combustion chamber. This involves removal of the burner and the burner mounting
plate from the heat exchanger.
Using a portable light source with a mirror inserted through and into the heat exchanger,
check for an accumulation of soot, scale, and particulate matter on the walls and in the
base of the drum, or on the floor of the combustion chamber. If a significant
accumulation is present, it should be removed. Use a flexible wire brush to loosen the
deposits on the heat exchanger walls. Remove any loose foreign material using a
vacuum cleaner.
Replace all gaskets, if removed, with new (unused) gaskets. Reassemble the burner
mounting plate, burner flange, and new gaskets in the reverse order they were
removed. Using a new cleanout cover gasket, reinstall the cleanout cap and tighten the
nut on the T-bolt enough to establish a good seal at the joint with the heat exchanger.
Reassemble the cleanout cover trim panel to the furnace using the original hardware.
Flue and Chimney
At least once a year, thoroughly inspect the heat exchanger flue pipe, the vent
connector, the chimney, or vent, and the barometric damper for signs of sagging, loose
connections, excessive corrosion, and deterioration. Clean, repair, or replace any
components for continued safe and proper operation of the furnace.
Summary of Contents for VC-BBP Spirit Series
Page 39: ...39 APPENDIX B ELECTRICAL DIAGRAMS VH BBP VH BNP VLF BBP VLF BNP VLR BBP VLR BNP Models...
Page 40: ...40 VC BBP VC BNP Models...
Page 47: ...47 APPENDIX D REPLACEMENT PARTS Highboy Model...
Page 48: ...48 Lowboy Front Flue Model...
Page 49: ...49 Lowboy Rear Flue Model...
Page 50: ...50 Horizontal Counterflow Model...
Page 51: ...51...
Page 52: ...52...