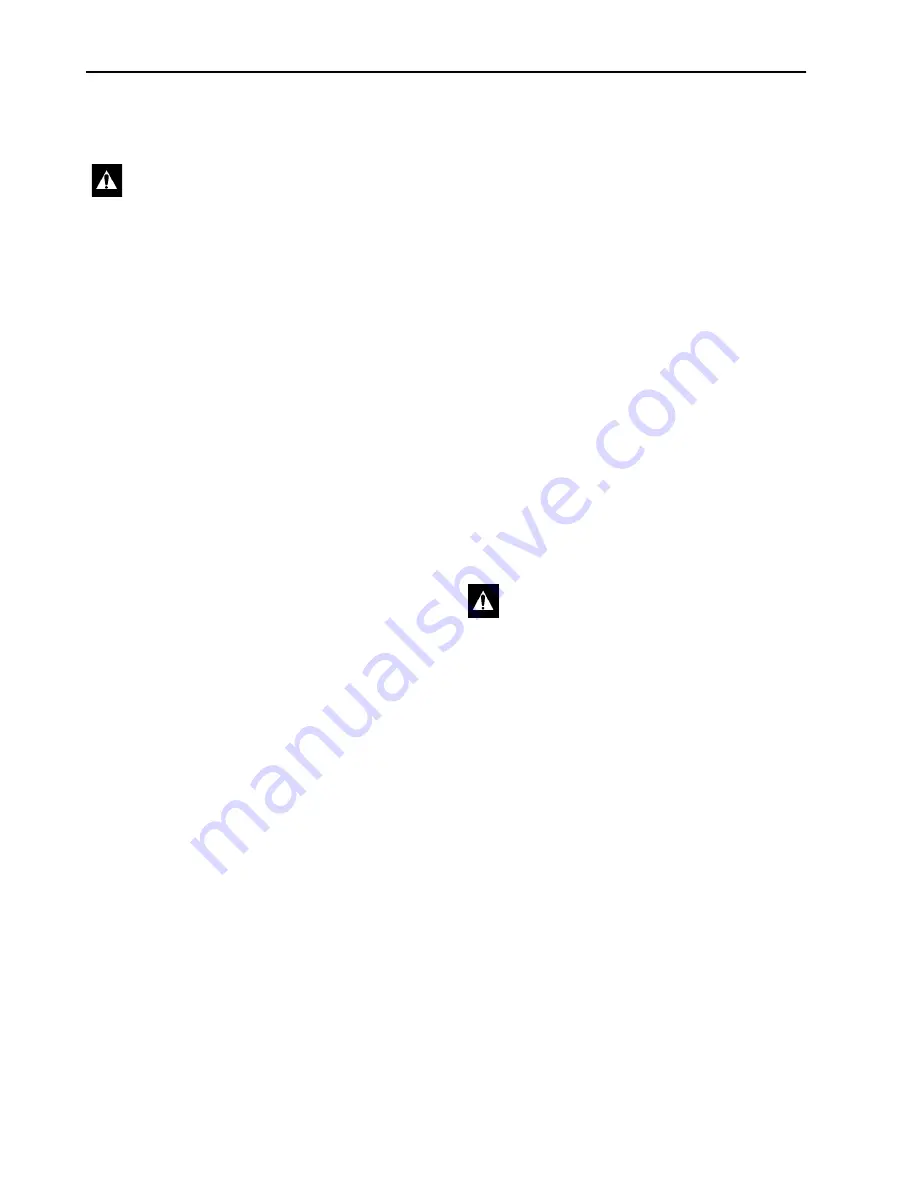
28
Disassembly and Reassembly
The following are suggested sequences for a full
disassembly and reassembly of the compressor.
Disassembly Sequence
1. Remove drive coupling.
2. Drain residual oil.
3. Remove manifold (four cylinder compressors
only).
4. Remove head, or heads from compressor
body.
5. Remove discharge valve plates from
cylinders.
6. Remove seal plate/mounting flange and
crankshaft seal.
7. Remove oil sump, internal oil filter (if so
equipped), and oil pickup screen.
8. Remove connecting rods, pistons and sleeves.
9. Remove oil pump.
10. Remove crankshaft.
11. Remove check valves.
Reassembly Sequence
1. Install check valves.
2. Install crankshaft.
3. Install oil pump.
4. Install connecting rods, pistons and sleeves.
5. Install oil pickup screen and internal oil filter
(if so equipped).
6. Install oil sump.
7. Install discharge valve plates.
8. Install head, or heads and manifold.
9. Install crankshaft seal and seal plate/mounting
flange.
10. Install drive coupling.
Fastener Torque Procedure
Use the following procedure when specific steps
are not provided.
1. Carefully remove any remaining gasket
material and clean both gasket surfaces
thoroughly.
2. Always use a new gasket and coat the gasket
with clean compressor oil just prior to
assembly.
3. Install all bolts (and washers) and pre-tighten
to 70% of the recommended torque, following
a criss-cross pattern.
4. Use a hand torque wrench and the same
criss-cross pattern to bring all bolts to final
torque. Hold bolts “On Torque” for a few
seconds.
Cleaning Components
Drive Coupling
Removal
There are several different types of drive
couplings and clutches used on the four cylinder
compressors in units manufactured by Thermo
King, but they are all held on by a single bolt
threaded into the end of the compressor
crankshaft. Once this bolt is removed, the
coupling or clutch can be removed from the shaft.
Remove the bolt and then use a puller to remove
the coupling or clutch.
CAUTION: When servicing compressors,
make sure all parts are reinstalled in their
original locations. Carefully mark similar
components, and pay special attention to
fastener length to ensure they are
reinstalled correctly.
CAUTION: Do not bead blast compressor
components clean. The abrasive media
can become embedded in castings, free
itself during compressor operation, and
damage the compressor. Only use
chemical solvents that leave no oily
residue, such as naphtha, lacquer thinner,
or brake cleaner to clean compressor
components. The solvents must be
nonchlorinated. Crocus cloth may be used
to remove rust or oxidation from external
compressor components.