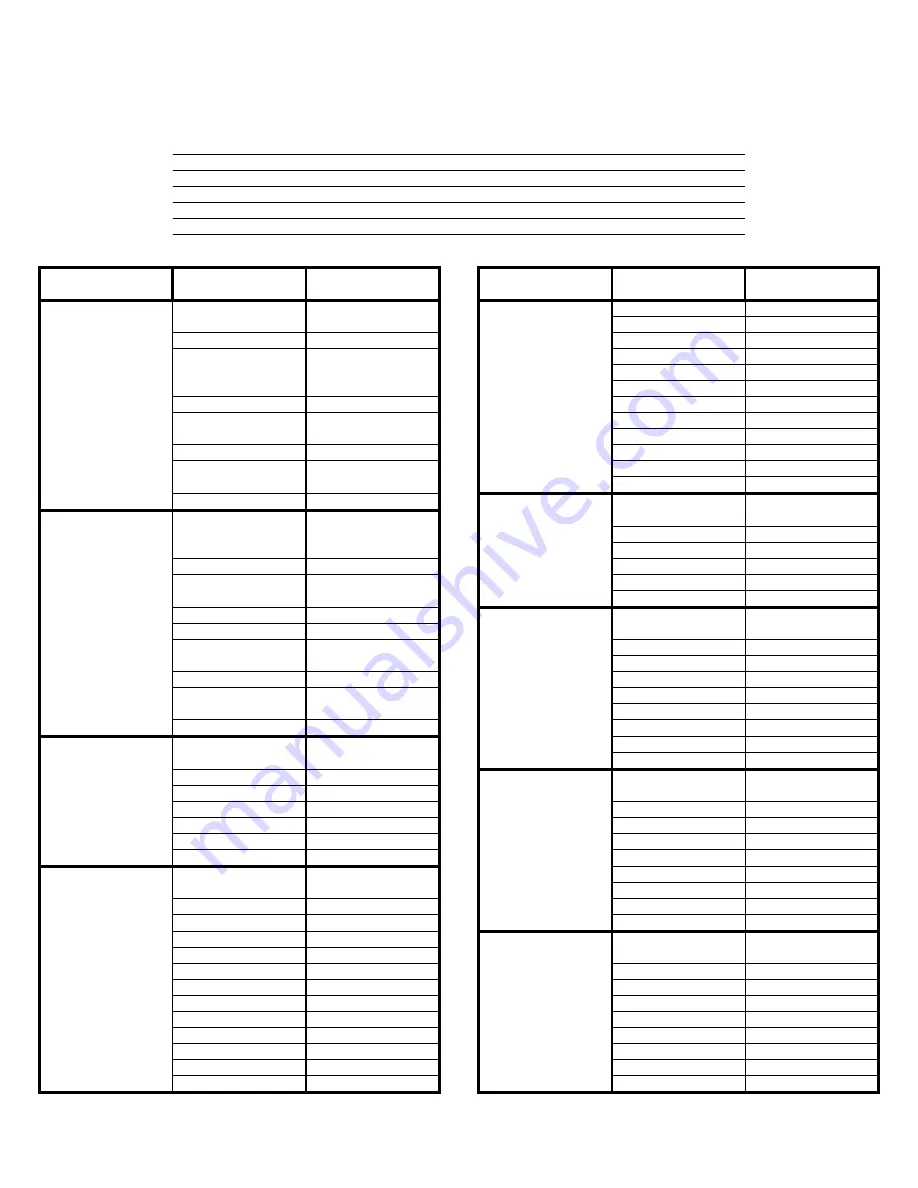
HONEYWELL TRULINE CONFIGURATION RECORD
SHT 1 OF 4
CUSTOMER:
JOB NUMBER:
UNIT SERIAL #:
CONTROL TYPE:
PREPARED BY:
DATE: / /
COMPLETED BY:
DATE: / /
GROUP
FUNCTION
VALUE OR
GROUP
FUNCTION
VALUE OR
PROMPT
PROMPT
SELECTION
PROMPT
PROMPT
SELECTION
TUNING1
PROP BD or
CHART
CHRTSPD
7 DAY
GAIN
HOUR/REV
RATE MIN
TIME DIV
21
RSET MIN or
MINOR DIV
FOUR
RESET RPM or
CONTINUE
NO
MAN RSET
CHART NAME
CYCSEC
HEADER
YES
PROP BD2 or
REMSW
NONE
GAIN2
WAKEMIN
RATE2MIN
WAKE HR
RSET2MIN or
WAKE DAY
RSET2RPM
WAKE MON
CYC2SEC
TIME
MINUTES
(CURRENT)
TUNING2
PROP BD or
HOURS
(CURRENT)
GAIN
DAY
(CURRENT)
RATE MIN
MONTH
(CURRENT)
RSET MIN or
YEAR
(CURRENT)
RSET PRM or
DAY
(CURRENT)
MAN RSET
CYCSEC
PEN1
PEN1
ENABLE
PROP BD2 or
PEN1IN
INPUT 1
GAIN2
CHART1HI
80
RATE2MIN
CHART1LO
-20
RSET2MIN or
PEN1ON
RSET2RPM
PEN1OFF
CYC2SEC
MAJORDIV
10
MINORDIV
10
SP RAMP1
SP RAMP
RNG1TAG
TEMP
TIME MIN
FINAL SP
PEN2
PEN2
ENABLE
SP RATE
PEN2IN
INPUT 2
EU/HR UP
CHART2HI
100
EU/HR DN
CHART2LO
0
SP PROG
PEN2ON
PEN2OFF
SP RAMP2
SP RAMP
MAJORDIV
10
TIME MIN
MINORDIV
10
FINAL SP
RING2TAG
% RH
SP RATE
EU/HR UP
PEN3
PEN3
DISABLE
EU/HR DN
PEN3IN
SP PROG
CHART3HI
CHART3LO
PEN3ON
PEN3OFF
MAJORDIV
MINORDIV
RING 3 TAG
HTRUCON3940.xls