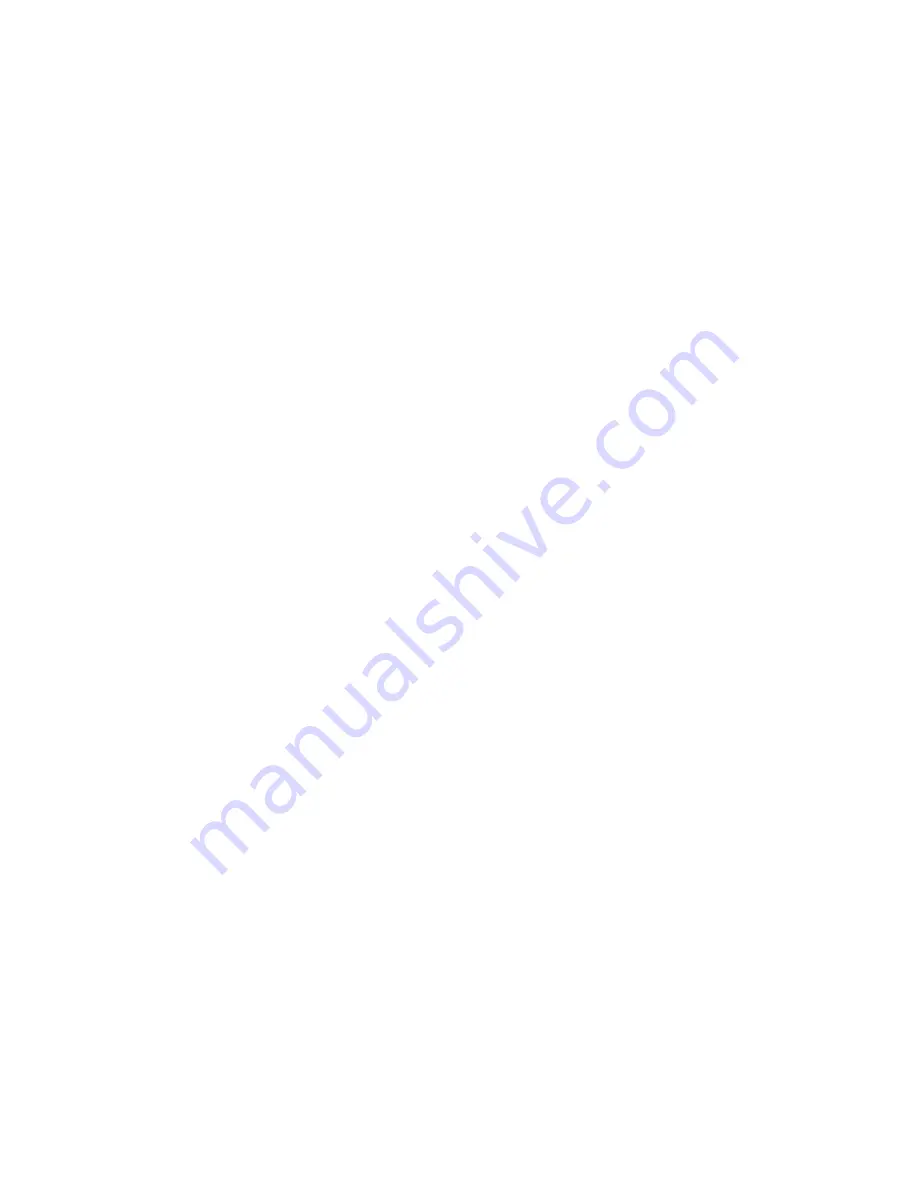
Model 3950/3951 ____________________________________________________________________________Specifications
7 - 2
Construction
Interior volume:
29 cu ft (823 liters)
Interior:
304 stainless steel, 2B finish
Exterior:
18-gauge cold rolled steel
Exterior Door:
Heated, triple pane tempered glass
Outer Door Gasket: Molded vinyl
Insulation:
2” fiberglass
Fittings
Access Port:
2.4” (6.1 cm) ID, one port per side
CO
2
Inlet: 1/4”
barbed
Sample Port:
Front mount, 1/4” barbed
Water Inlet:
1/4” MPT for automatic fill
Overflow Drain:
3/8” MPT
Condensate Drain:
3/8” FPT
Electrical
Model 3950:
100-120VAC, 50/60Hz, 1 PH, 10.0 FLA
Operating Range, including fluctuations-
90-125V, 50-60Hz
15A Breaker power switch
Model 3951:
200-230VAC, 50/60Hz, 1 PH, 6.0 FLA
Operating Range, including fluctuations-
180-250V, 50-60Hz
8A Breaker power switch
Power Switch:
2-pole circuit breaker
Accessory Outlet:
Voltage equal to the cabinet input,
75W max., 0.5mA leakage current
Interior Outlet:
Voltage equal to cabinet input,
230W max, 0.5 mA leakage current
Remote Alarm Contacts:
Deviation of temperature,
CO
2
& power. N/O & N/C
Unit BTU Output
115V/230V:
510 BTUH (150W)
Dimensions
Exterior:
38.0” W x 80.0” H x 33.0” F-B
(96.5 cm x 203.2 cm x 83.8 cm)
Interior:
31.0” W x 60.0” H x 27.0” F-B
(78.7 cm x 152.4 cm x 68.6 cm)
Weight:
500 lbs. (226.8 kg)
Accessories: (CI = Customer Install, FI = Factory Install)
224139
Stainless steel shelf, channels, CI
224155
Perforated shelf kit, CI
190239
Lexan inner door kit, FI
190591
Door cover, FI
190892
Door cover, CI
190164
Thru-wall access port, FI
500182
Reinforced floor with ramp to
accommodate cell roller, CI
190777
Reinforced floor with ramp to
accommodate cell roller, FI
191596
Carboy kit with 2 gal. carboy and
bracket, CI
1900005
Reinforced shelf kit to accommodate
Shaker, FI
190514
Door lock, FI
224161
Reinforced shelves, channels 150#,
CI
201155
Recorder 0-60°C, 7 day, single pen,
115V, CI
201156
Recorder 0-60°C, 7 day, single pen,
230V, CI
201159
Recorder 0-60°C, 7 day, dual pen,
115V, CI
201160
Recorder 0-60°C, 7 day, dual pen,
230V, CI
1900000
Built-in CO
2
Gas Guard, FI
190512
4-20mA output board, FI
190523
RS-485 interface, FI (compatible
with 1535 alarm monitor only)
190543
0-5 volt output board, FI
190544
0-1 volt output board, FI
Certification:
3950 Series - UL, CSA, CE
3951 Series – CSA, CE
Safety Specifications:
Altitude:
2,000 meters
Temperature:
5°C to 40°C
Humidity:
80% RH at or below 31°C, decreas-
ing linearly to 50% RH at 40°C
Mains Supply Fluctuations:
Operating Voltage Range
Installation Category II
Pollution Degree 2
Class of Equipment I